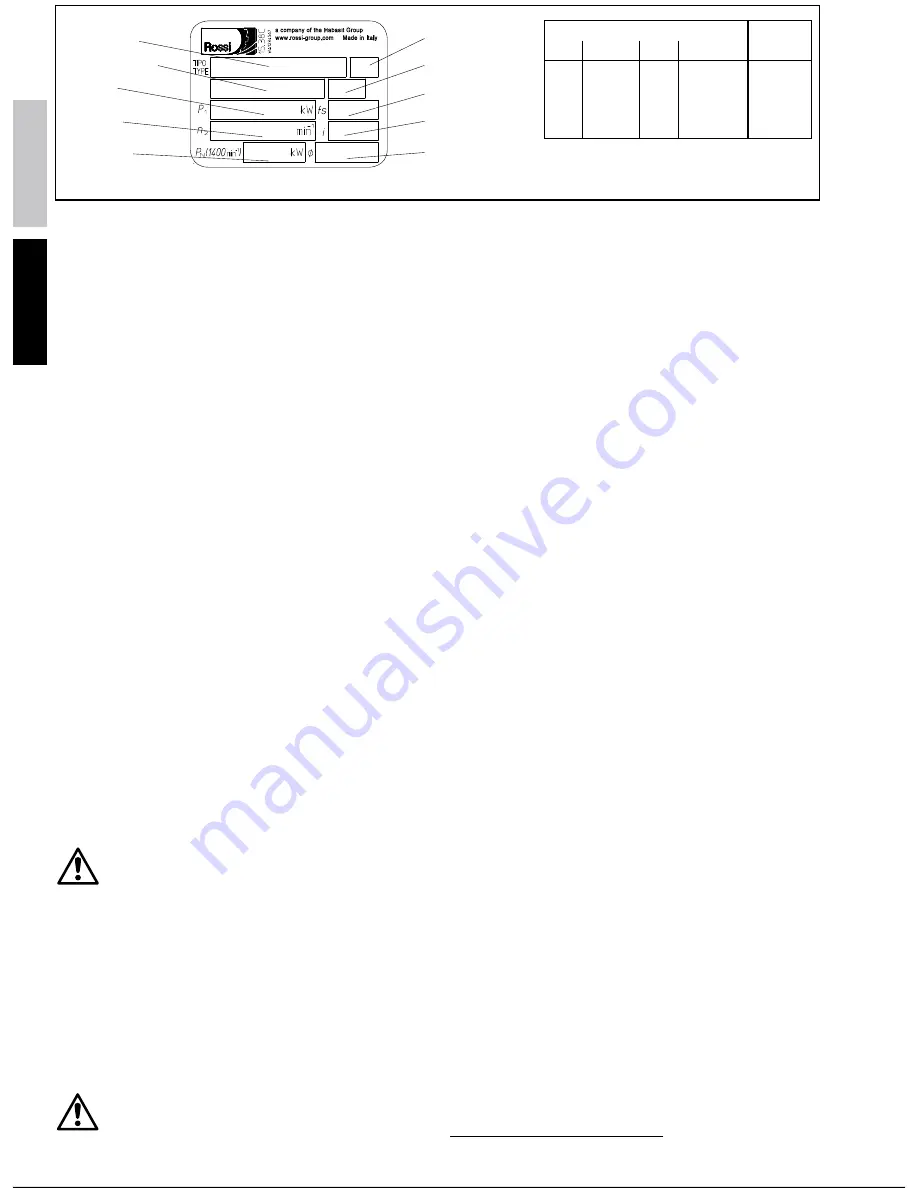
IT
EN
Unless otherwise agreed in the order, products are adequately
packed: on pallet, protected with a polyethylene film, wound with
adhesive tape and strap (bigger sizes); in carton pallet, wound with
adhesive tape and strap (smaller sizes); in carton boxes wound with
tape (for small dimensions and quantities). If necessary, gear redu-
cers are conveniently separated by means of anti-shock foam cells or
of filling cardboard.
Do not stock packed products on top of each other.
4 - Storing
Surroundings should be sufficiently clean, dry and free from ex-
cessive vibrations (
v
eff
ø
0,2 mm/s) to avoid damage to bearings (ex-
cessive vibration should also be guarded during transit, even if within
wider range) and ambient storage temperature should be 0
4
+40 °C:
peaks of 10 °C above and below are acceptable.
The gear reducers filled with oil must be positioned according to the
mounting position mentioned on the order during transport and storage.
Every six months rotate the shafts (some revolutions are sufficient)
to prevent damage to bearings and seal rings.
Assuming normal surroundings and the provision of adequate pro-
tection during transit, the unit is protected for storage up to 1 year.
For a 2 year storing period in normal surroundings it is necessary to
pay attention also to following instructions:
– generously grease the sealings, the shafts and the unpainted
machined surfaces, if any, and periodically control conservation
state of the protective anti-rust oil;
– for gear reducers and gearmotors supplied without oil: insert anti-
condensation pastilles into the gear reducers to be replaced befo-
re due date and remove them before commissioning (as alternati-
ve completely fill the gear reducers with lubrication oil and the
specified level before commissioning).
For storages longer than 2 years or in aggressive surroundings or
outdoors, consult Rossi.
5 - lnstallation
5.1 - General
Before the installation, verify that:
– there were no damages during the storing or the transport;
– design is suitable to the environment (temperature, atmosphere,
etc.);
– electrical connection (power supply, etc.) corresponds to motor
name plate data;
– used mounting position corresponds to the one stated in name
plate.
Attention!
When lifting and transporting the gear reducer
or gearmotor use through holes or tapped holes of the
gear reducer casing; be sure that load is properly balanced
and provide lifting systems, and cables of adequate sec-
tion. If necessary, gear reducer and gearmotor masses are stated
in Rossi technical catalogues.
Be sure that the structure on which gear reducer or gearmotor is
fitted is plane, levelled and sufficiently dimensioned in order to assu-
re fitting stability and vibration absence (vibration speed
v
eff
ø
3,5
mm/s for
P
N
ø
15 kW and
v
eff
ø
4,5 mm/s for
P
N
> 15 kW are accep-
table), keeping in mind all transmitted forces due to the masses, to
the torque, to the radial and axial loads.
For the dimensions of fixing screws of gear reducer feet and the
depth of tapped holes consult the Rossi technical catalogues.
Carefully select the length of fixing screws when using tapped holes
for gear reducer fitting, in order to assure a sufficient meshing thread
length for the correct gear reducer fitting to the machine without
breaking down the threading seat.
Attention! Bearing life and good shaft and coupling
running depend on alignment precision between the
shafts.
Carefully align the gear reducer with the motor and
the driven machine (with the aid of shims if need be, for
gear reducers size
ù
400 use level tapped holes), interposing flexible
couplings whenever possible.
Incorrect alignment
may cause
breakdown of shafts and/or bear-
ings
(which may cause overheatings) which may represent
heavy
danger for people
.
Do not use motor eyebolts when lifting the gearmotors.
Position the gear reducer or gearmotor so as to allow a free passage
of air for cooling both gear reducer and motor (especially at their fan
side).
Avoid: any obstruction to the air flow; heat sources near the gear
reducer that might affect the temperature of cooling air and of gear
reducer (for radiation); insufficient air recycle and applications hinder-
ing the steady dissipation of heat.
Mount the gear reducer or gearmotor so as not to receive vibrations.
Mating surfaces (of gear reducer and machine) must be clean and suffi-
ciently rough (approximately
R
a
ù
6,3
m
m) to provide a good friction
coefficient: remove by a scraper or solvent the eventual paint of gear
reducer coupling surfaces.
When external loads are present use pins or locking blocks, if ne-
cessary.
When fitting gear reducer and machine and/or gear reducer and even-
tual flange
B5
it is recommended to use
locking adhesives
on the
fastening screws (also on flange mating surfaces).
Before wiring-up the gearmotor make sure that motor voltage corre-
sponds to input voltage. If direction of rotation is not as desired,
invert two phases at the terminals.
Y-
D
starting should be adopted for no-load starting (or with a very
small load) and for smooth starts, low starting current and limited
stresses, if requested.
If overloads are imposed for long periods or if shocks or danger of
jamming are envisaged, then motor-protection, electronic torque li-
miters, fluid couplings, safety couplings, control units or other similar
devices should be fitted.
Usually protect the motor with a thermal cut-out
however,
where duty cycles involve a high number of on-load starts, it is nec-
essary to utilise
thermal probes
for motor protection (fitted on the
wiring); magnetothermic breaker is unsuitable since its threshold
must be set higher than the motor nominal current of rating.
Connect thermal probes, if any, to auxiliary safety circuits
.
Use varistors and/or RC filters to limit voltage peaks due to con-
tactors.
When gear reducer is equipped with a backstop device
1)
, provide a
protection system where a backstop device breaking could cause
personal injury or property damage.
Whenever a leakage of lubricant could cause heavy damages, increase
the frequency of inspections and/or envisage appropriate control devic-
es (e.g.: remote level gauge, lubricant for food industry, etc.).
In polluting surroundings, take suitable precautions against lubricant
contamination through seal rings
or other.
For outdoor installation or in a hostile environment (atmospheric cor-
rosivity category
C3
according to ISO 12944-2), protect the gear
reducer or gearmotor with a proper dual-compound anticorrosion paint;
added protection may be afforded by applying water-proof grease
(especialIy around the rotary seating of seal rings and at shaft end
access points).
Gear reducers and gearmotors should be protected whenever pos-
sible and by appropriate means from solar radiation and extremes of
weather: protection
becomes essential
when high or low speed
shafts are vertically disposed or when the motor is installed vertical
with fan uppermost.
For ambient temperature greater than +40 °C or less than 0 °C, con-
sult Rossi.
When gear reducer or gearmotor is supplied with water cooling by
coil or independent cooling unit, see ch 7.
1) The presence on gear reducer of backstop device is stated by the arrow near the low
speed shaft, indicating the free rotation, excluding shaft mounted gear reducers where
B or C designs are stated (see Rossi technical catalogues).
Designation (see
table on the right)
Non-standard designs
Motor power
Gearmotor
output speed
Gear reducer
nominal power
Two months and year
of manufacture
Mounting position (when
differing from IM B3
or B5)
Gearmotor
service factor
Transmission
ratio
Ø Flange - motor
shaft
Fig. 1 (for more information, see Rossi technical catalogs; consult us).
Designation
Product
Machine Train of gears
Size
Design
R, MR
V, IV, 2IV
32 ... 250 UO ...
Worm
R, MR
2I, 3I
32 ... 180 FC ..., PC ..., UC ...
Coaxial
R, MR
I, 2I, 3I, 4I
40 ... 631 UP ...
Parallel shafts
R, MR
CI, ICI, C2I, C3I 40 ... 631 UO ...
Right angle shafts
R
C
80 ... 320 PO ..., FO ...
Right angle shafts
R
2I
85 ... 250 OP
Shaft mounted
Note
: Starting from 04/05/2010 the company name ROSSI MOTORIDUTTORI S.p.A. has been changed into Rossi S.p.A., and the nameplates have been updated accordingly.
Attention!
for the maintenance, installation of gear reducers coupled with synchronous and asynchronous servomotors (even if with a different name plate) follow the instructions of present handbook.
Summary of Contents for Ariete NS3015P
Page 1: ...Revision Instructions Manual Translation of the original instructions Ariete NS3015P 13490 0...
Page 12: ...GEA Niro Soavi...
Page 19: ...0 0 12 3 3 3 3 4 5 5 6 7 3 8 9 7...
Page 171: ......
Page 173: ......
Page 175: ......
Page 177: ......
Page 181: ......
Page 182: ...E E F E F E F E F E E E 79 6 09 10 6 09 10 3 0 60 9 B 01 607 06 10 9 1 6 09 9 6 7 0 706 9 0...
Page 183: ......
Page 184: ......
Page 186: ......
Page 188: ...PHONE 39 0 521 965411 FAX 39 0 521 242819...
Page 190: ......
Page 192: ......
Page 194: ......
Page 196: ......
Page 198: ......
Page 200: ......
Page 201: ......
Page 204: ......
Page 205: ......
Page 206: ......
Page 207: ......
Page 208: ......
Page 209: ......
Page 210: ......
Page 211: ......
Page 212: ......
Page 213: ......
Page 214: ......
Page 215: ......
Page 216: ......
Page 221: ...GEA Niro Soavi Ref Part Code Description Description 7 01 1 9564 9000 002 MOTORE MOTOR...
Page 222: ...GEA Niro Soavi Ref Part Code Description Description 7 01 2 9565 2316 562 MOTORE MOTOR...
Page 275: ...55 PYCCKN PYCCKN...
Page 276: ...56...
Page 277: ...57 PYCCKN...
Page 278: ...58...
Page 280: ...60...
Page 281: ...61 PYCCKN...
Page 282: ......
Page 294: ...GEA Niro Soavi Ref Part Code Description Description 7 01 5 9533 4064 000 RIDUTTORE GEARBOX...
Page 296: ......
Page 316: ...IT EN 1RWH 1RWHV...
Page 320: ...IT EN...