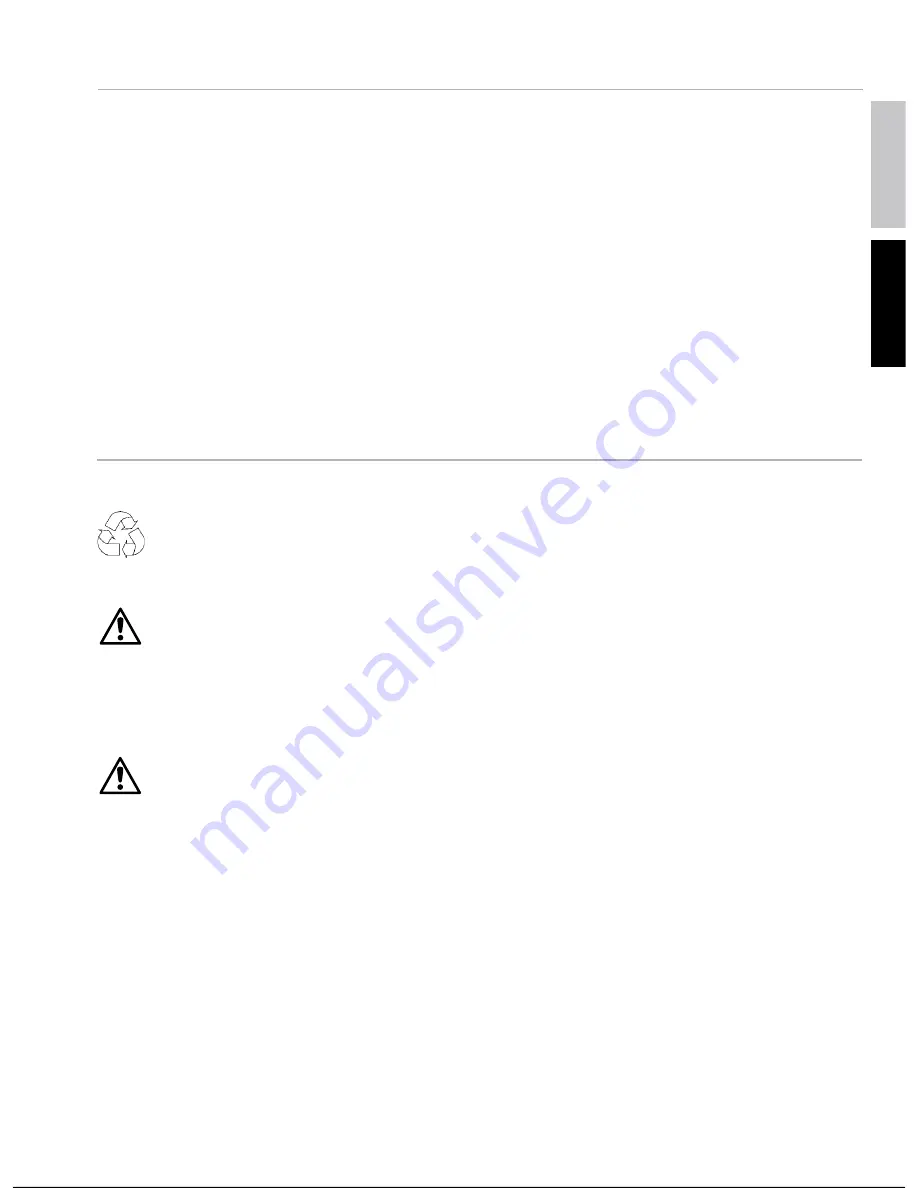
IT
EN
Contents
1 - General safety instructions
13
2 - Operating conditions
13
3 - How supplied
13
3.1 - Receipt
13
3.2 - Name plate
13
3.3 - Painting
13
3.4 - Protections and packing
13
4 - Storing
14
5 - Installation
14
5.1 - General
14
5.2 - Fitting of components to shaft ends
15
5.3 - Shaft-mounting
15
5.4 - Hollow low speed shaft
15
6 - Lubrication
18
6.1 - General
18
6.2 - Lubrication table
16
6.3 - Extruder support lubrication
18
7 - Cooling system
18
7.1 - Cooling by fan
18
Operating instructions gear reducers and gearmotors
7.2 - Water cooling by coil
18
7.3 - Independent cooling unit
18
8 - Commissioning
18
9 - Maintenance
18
9.1 - General
18
9.2 - Coil
19
9.3 - Seal rings
19
9.4 - Motor replacement
19
9.5 - Bearings
19
9.6 - Metal filler plug with filter and valve
19
10 - Sound levels
19
Painting table
20
Table of tightening torques for axial fastening
bolts and shrink disc
20
Table of tightening torques for fastening
bolts (foot and flange)
20
Table of tightening torques for plugs
20
Gear reducer troubles: causes and
corrective actions
21
Recycling
(keeping in mind the instructions in force):
– the elements of casing, gear pairs, shafts and bearings of gear
reducer must be transformed into steel scraps. The ele-
ments in grey cast iron will be subjected to the same tre-
atment if there is no particular instruction;
– the worm wheels are made in bronze and must be treated
adequately;
– exhausted oils must be recycled and treated according to the
instructions.
The paragraphs marked with present symbol contain
dispositions to be strictly respected in order to assure
personal
safety
and to avoid any
heavy damages
to the
machine or to the system (e.g.: works on live parts, on lif-
ting machines, etc.); the responsible for the installation or mainte-
nance must scrupulously
follow all instructions contained in
present handbook.
1 - General safety instructions
Gear reducers and gearmotors present dangerous parts because
they may be:
– live;
– at temperature higher than +50 °C;
– rotating during the operation;
– eventually noisy (sound levels > 85 dB(A)).
An incorrect installation, an improper use, the removing or disconnec-
tion of protection devices, the lack of inspections and maintenance,
improper connections may cause severe personal injury or property
damage. Therefore the component must be moved, installed, commis-
sioned, handled, controlled, serviced and repaired
exclusively by
responsible qualified personnel
(definition to IEC 364).
It is recommended to pay attention to all instructions of present
handbook, all instructions relevant to the system, all existing safety
laws and standards concerning correct installation.
Attention!
Components in non-standard design or with constructive
variations may differ in the details from the ones described here fol-
lowing and may require additional information.
Attention!
For the installation, use and maintenance of the electric
motor (standard, brake or non-standard motor) and/or the electric sup-
ply device (frequency converter, soft-start, etc.) and accessories, if any
(flow indicators, independent cooling unit, thermostat, ecc) consult the
attached specific documentation. If necessary, require it.
Attention!
For any clarification and/or additional information consult
Rossi and specify all name plate data.
Gear reducers and gearmotors of present handbook are normally
suitable for installations in industrial areas:
additional protection
measures,
if necessary for different employs, must be adopted and
assured by the person responsible for the installation.
IMPORTANT: the components supplied by Rossi must be incorpora-
ted into machinery and
should not be commissioned before the
machinery in which the components have been incorporated
conforms to:
–
Machinery directive 2006/42/EC and subsequent updatings;
in particular, possible safety guards for shaft ends not being
used and for eventually accessible fan cover passages (or
other) are the Buyer’s responsibility;
–
«Electromagnetic compatibility (EMC)» directive 2004/108/
EC and subsequent updatings.
When operating on gear reducer (gearmotor) or on components
connected to it
the machine must be at rest:
disconnect motor
(including auxiliary equipments) from power supply, gear reducer
from load, be sure that safety systems are on against any accidental
starting and, if necessary, pre-arrange mechanical locking devices (to
be removed before commissioning).
If deviations from normal operation occur (temperature increase,
unusual noise, etc.) immediately switch off the machine.
The products relevant to this handbook correspond to the technical
level reached at the moment the handbook is printed. ROSSI MO-
TORIDUTTORI reserves the right to introduce, without notice, the
necessary changes for the increase of product performances.
2 - Operating conditions
Gear reducers are designed for industrial applications according to
name plate data, at ambient temperature 0
4
+40 °C (with peaks at
-10 °C and +50 °C), maximum altitude 1 000 m.
Not allowed running conditions: application in aggressive environ-
ments having explosion danger, etc. Ambient conditions must com-
ply with specifications stated on name plate.
3 - How supplied
3.1 - Receipt
At receipt verify that the unit corresponds to the one ordered and has
not been damaged during the transport, in case of damages, report
them immediately to the courier.
Avoid commissioning gear reducers and gearmotors, that are even if
slightly damaged.
3.2 - Name plate
Every gear reducer presents a name plate in anodised aluminium
containing main technical information relevant to operating and con-
structive specifications and defining, according to contractual agree-
ments, the application limits (see fig. 1); the name plate must not be
removed and must be kept integral and readable. All name plate data
must be specified on eventual spare part orders.
3.3 - Painting
Products are painted according to the painting table shown on page 20.
Before adding further coats of paint (use dual-compound paints only),
properly protect the seal rings (which must neither be damaged nor
painted), degrease and sand the gear reducer (or gearmotor) surfaces.
3.4 - Protections and packing
Overhanging free shaft ends and hollow shafts are treated with protec-
tive anti-rust long life oil and protected with a plastic (polyethylene) cap
(only up to D
ø
48 mm for overhanging shafts, D
ø
110 mm for hollow
shafts). All internal parts are protected with protective anti-rust oil.
Summary of Contents for Ariete NS3015P
Page 1: ...Revision Instructions Manual Translation of the original instructions Ariete NS3015P 13490 0...
Page 12: ...GEA Niro Soavi...
Page 19: ...0 0 12 3 3 3 3 4 5 5 6 7 3 8 9 7...
Page 171: ......
Page 173: ......
Page 175: ......
Page 177: ......
Page 181: ......
Page 182: ...E E F E F E F E F E E E 79 6 09 10 6 09 10 3 0 60 9 B 01 607 06 10 9 1 6 09 9 6 7 0 706 9 0...
Page 183: ......
Page 184: ......
Page 186: ......
Page 188: ...PHONE 39 0 521 965411 FAX 39 0 521 242819...
Page 190: ......
Page 192: ......
Page 194: ......
Page 196: ......
Page 198: ......
Page 200: ......
Page 201: ......
Page 204: ......
Page 205: ......
Page 206: ......
Page 207: ......
Page 208: ......
Page 209: ......
Page 210: ......
Page 211: ......
Page 212: ......
Page 213: ......
Page 214: ......
Page 215: ......
Page 216: ......
Page 221: ...GEA Niro Soavi Ref Part Code Description Description 7 01 1 9564 9000 002 MOTORE MOTOR...
Page 222: ...GEA Niro Soavi Ref Part Code Description Description 7 01 2 9565 2316 562 MOTORE MOTOR...
Page 275: ...55 PYCCKN PYCCKN...
Page 276: ...56...
Page 277: ...57 PYCCKN...
Page 278: ...58...
Page 280: ...60...
Page 281: ...61 PYCCKN...
Page 282: ......
Page 294: ...GEA Niro Soavi Ref Part Code Description Description 7 01 5 9533 4064 000 RIDUTTORE GEARBOX...
Page 296: ......
Page 316: ...IT EN 1RWH 1RWHV...
Page 320: ...IT EN...