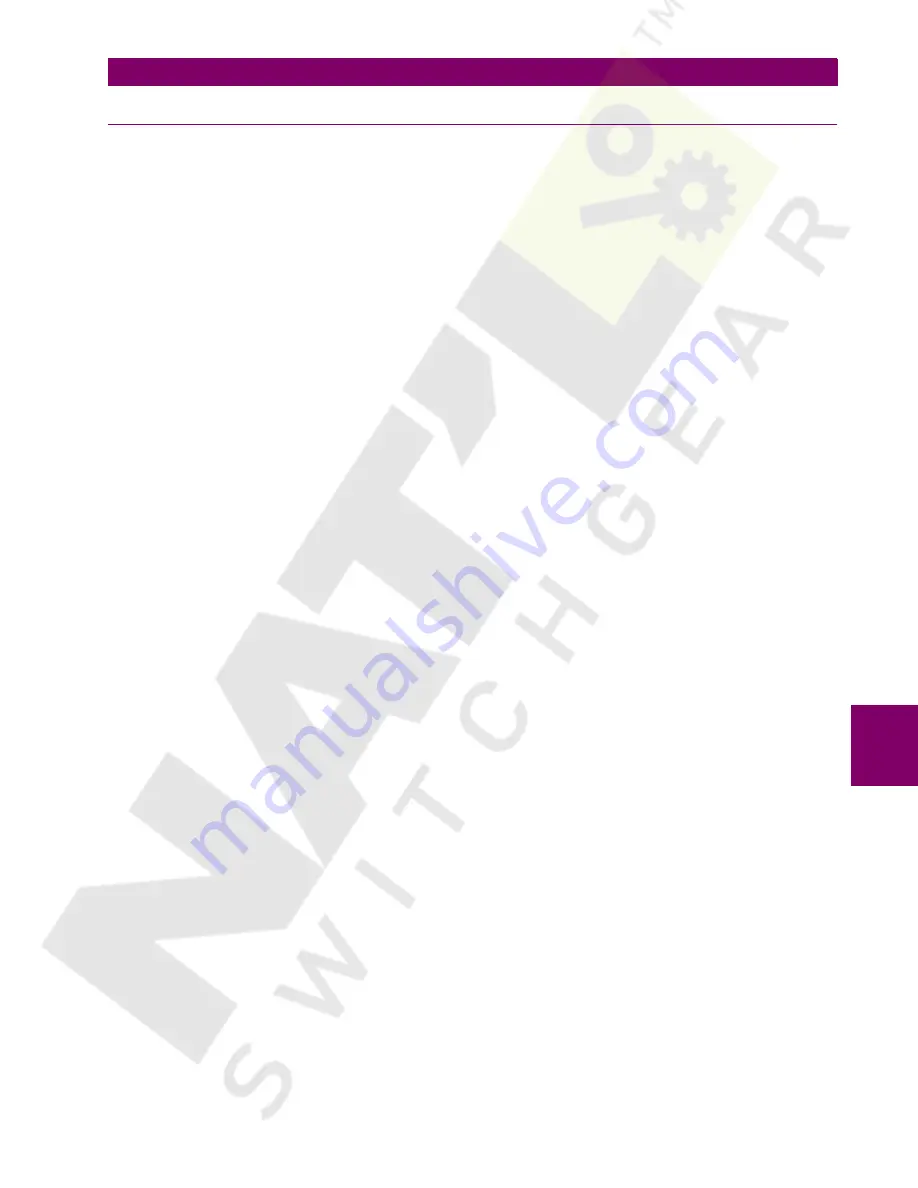
GE Power Management
750/760 Feeder Management Relay
17-
63
17 COMMISSIONING
17.9 CONTROL SCHEMES
17
17.9.6 UNDERFREQUENCY RESTORATION
a) PROCEDURE FOR LOGIC AND TIMERS
1.
Make connections for this test per Figure 17–1: RELAY TEST WIRING – WYE CONNECTION or Figure
17–2: RELAY TEST WIRING – DELTA CONNECTION on page 17–4.
2.
Note that
UNDERFREQUENCY 1
must be programmed, with the function as
Trip
,
MINIMUM VOLTAGE
as 0, and
UNDERFREQUENCY 2
must be
Disabled
.
3.
Assert or De-assert a logic input to simulate a closed breaker.
4.
Inject a voltage at nominal voltage and frequency into the bus voltage phase A input.
5.
Initially set
UNDERFREQUENCY RESTORATION
setpoint to
Alarm
, and other setpoints as required.
6.
Reduce the frequency to below the underfrequency pickup level. After the programmed delay
UNDERFRE-
QUENCY 1
should cause a trip, which should not initiate underfrequency restoration as the breaker is
closed. Diagnostic message "Ufreq Restore Init" should not be displayed.
7.
Assert or De-assert a logic input to simulate an open breaker, which should initiate underfrequency resto-
ration. The diagnostic alarm message and LED should be displayed, and any output relays programmed to
operate for this condition should operate.
8.
Change the Underfrequency Restoration function setpoint to Control, and the diagnostic message should
change to control and the ALARM LED should turn off. Return this setpoint to Alarm.
9.
Assert logic input Block Restoration. The diagnostic alarm message and LED should be removed from the
display, and any output relays that operated should reset.
10. De-assert the logic input. The alarm message and LED should again be displayed and output relays oper-
ated. After the delay programmed in
INCOMPLETE SEQUENCE TIME
, the alarm message and LED should be
removed from the display and output relays reset.
11. Return the reduced frequency to nominal, resetting both the underfrequency trip condition and underfre-
quency restoration.
12. Reduce frequency until Underfrequency 1 trips, then immediately return the frequency to nominal. The
diagnostic alarm message and LED should be displayed, and output relays operated.
13. Provide a Reset to the relay, and the alarm message and LED should be removed from the display and
output relays reset. Remove the Reset.
14. Arrange the interval timer to start on appearance of voltage and stop when the 2 CLOSE relay operates.
15. Turn the voltage, of a frequency to cause an Underfrequency 1 trip, off. Reset the timer.
16. Turn the voltage on. The 2 CLOSE relay should operate after the delay programmed in setpoint
UNDER-
FREQ RESTORE DELAY
.
17. If Underfrequency 2 initiation is to be checked, change
UNDERFREQUENCY RESTORATION
to
Disabled
,
UNDERFREQUENCY 1
to
Disabled
,
UNDERFREQUENCY 2
to
Trip
and repeat steps 3 through 7.
b) PROCEDURE TO CHECK MINIMUM VOLTAGE
1.
Assert or De-assert a logic input to simulate an open breaker.
2.
Set
UNDERFREQ RESTORE DELAY
to
0
.
3.
Inject a voltage below the
UNDERFREQ RESTORE MIN VOLTS
level into the bus voltage input of the relay.
4.
Reduce the injected frequency to cause an underfrequency trip, then increase the frequency to nominal.
5.
Slowly raise
V
a
until the 2 CLOSE relay operates. This is the operating level of setpoint
UNDERFREQ
RESTORE MIN VOLTS
.
Summary of Contents for 750
Page 2: ......
Page 4: ......
Page 124: ...8 14 750 760 Feeder Management Relay GE Power Management 8 12 INSTALLATION 8 S1 RELAY SETUP 8 ...
Page 488: ...A 4 750 760 Feeder Management Relay GE Power Management A 1 FIGURES AND TABLES APPENDIXA A ...
Page 492: ...C 2 750 760 Feeder Management Relay GE Power Management C 1 WARRANTY INFORMATION APPENDIXC C ...
Page 502: ...x 750 760 Feeder Management Relay GE Power Management INDEX ...
Page 503: ...GE Power Management 750 760 Feeder Management Relay NOTES ...