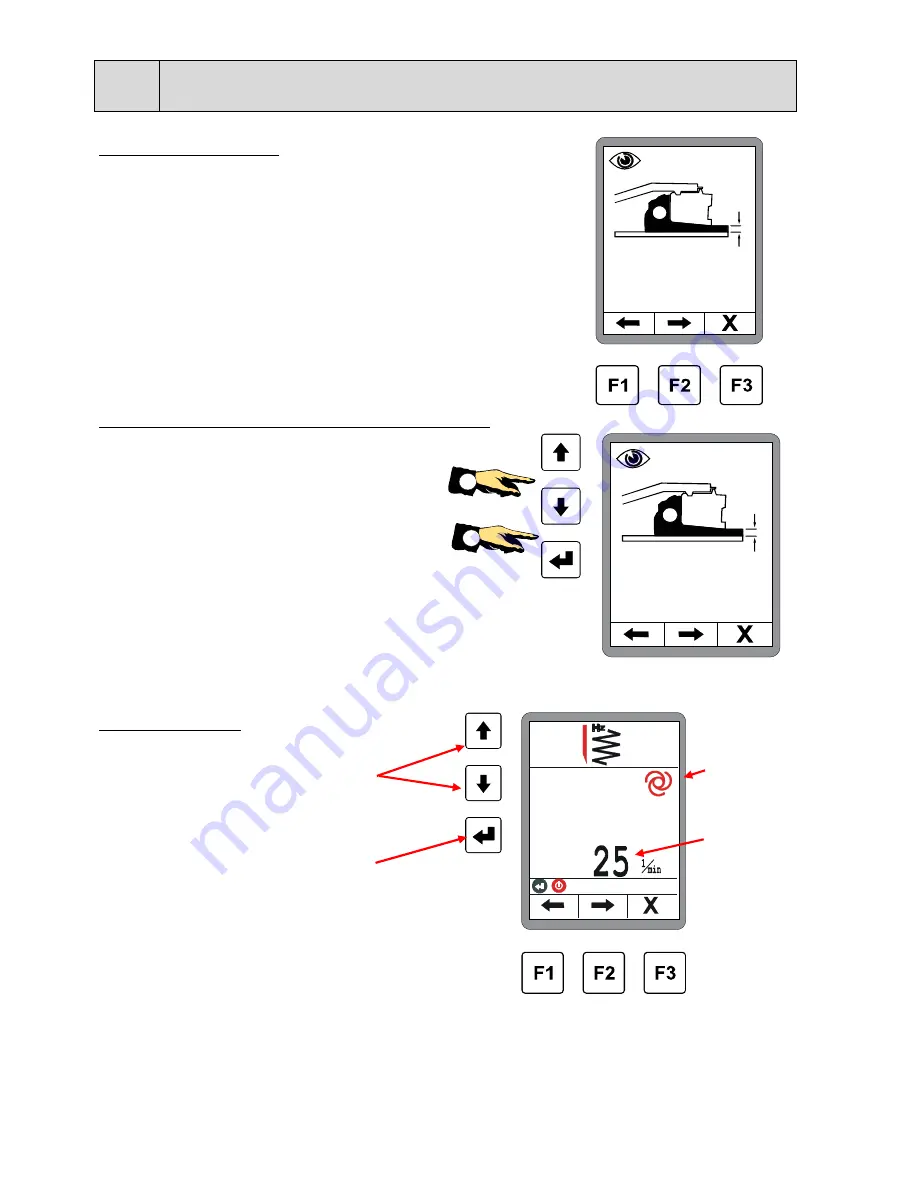
74
8 Operation in general
Layer thickness display:
This window appears only if the layer thickness has been
activated, and the corr. Sensors are connected.
(See also 8.11.1 Configuration menu)
Quick adjustment of the layer thickness display:
Adjustment of the displayed layer
thickness as following:
1.) Press and hold ENTER key, and
2.) to adjust the value in parallel
with the UP / DOWN buttons.
Tamper frequency:
The nominal value can be changed using the
up/down buttons.
The ENTER button changes over the operating
mode of the control circuit.
(Manual <---> Automatic)
ATTENTION!
Press any button to accept the
adjusted settings.
Operating
mode
Nominal value
c m
11. 2
c m
11. 2
2
1