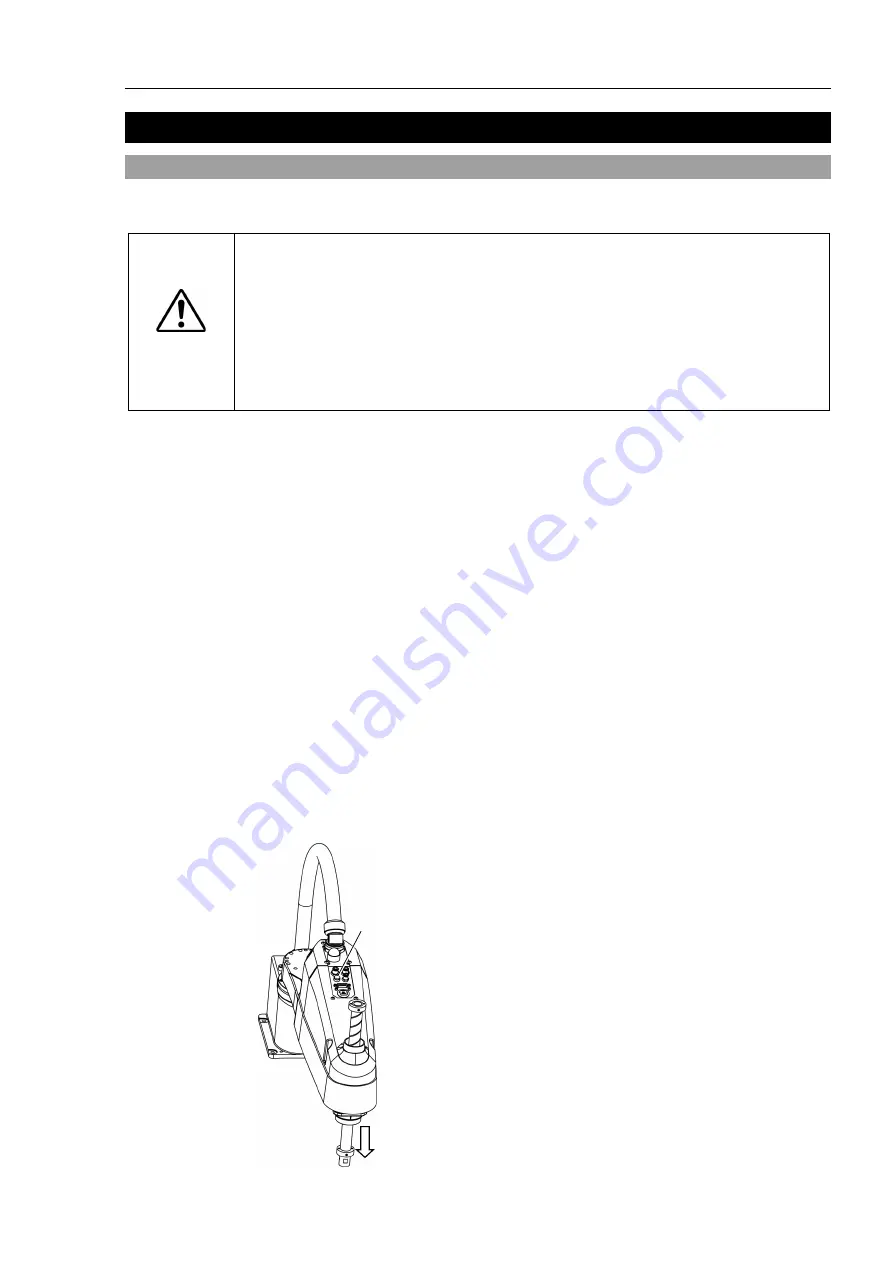
Setup & Operation 4. Setting of End Effectors
LS10-B Rev.6
33
4. Setting of End Effectors
4.1 Attaching an End Effector
Users are responsible for making their own end effector(s). Before attaching an end
effector, observe these guidelines.
CAUTION
■
If you use an end effector equipped with a gripper or chuck, connect wires and/or
pneumatic tubes properly so that the gripper does not release the work piece
when the power to the robot system is turned OFF. Improper connection of the
wires and/or pneumatic tubes may damage the robot system and/or work piece
as the work piece is released when the Emergency Stop switch is pressed.
I/O outputs are configured at the factory so that they are automatically shut off (0)
by power disconnection, the Emergency Stop switch, or the safety features of the
robot system.
Shaft
- Attach an end effector to the lower end of the shaft.
For the shaft dimensions, and the overall dimensions of the Manipulator, refer to S
etup
& Operation: 2. Specifications.
- Do not move the upper limit mechanical stop on the lower side of the shaft.
Otherwise, when “Jump motion” is performed, the upper limit mechanical stop may hit
the Manipulator, and the robot system may not function properly.
- Use a split muff coupling with an M4 bolt or larger to attach the end effector to the
shaft.
Brake release switch
- Joint #3 and #4 cannot be moved up/down by hand because the electromagnetic brake
is applied to the joint while power to the robot system is turned OFF.
This prevents the shaft from hitting peripheral equipment in the case that the shaft is
lowered by the weight of the end effector when the power is disconnected during
operation, or when the motor is turned OFF even though the power is turned ON.
To move Joint #3 up/down or rotate Joint #4 while attaching an end effector, turn ON
the Controller and move the joint up/down or rotate the joint while pressing the brake
release switch.
This button switch is a momentary-type; the brake is released only while the button
switch is being pressed
- Be careful of the shaft while the brake release switch is being pressed because the shaft
may be lowered by the weight of the end effector.
Brake release switch
Shaft may be lowered by the
weight of the end effector.
Summary of Contents for LS10-B
Page 1: ...Rev 6 EM204R4257F SCARA ROBOT LS10 B series MANIPULATOR MANUAL ...
Page 2: ...MANIPULATOR MANUAL LS10 B series Rev 6 ...
Page 8: ...vi LS10 B Rev 6 ...
Page 12: ...TABLE OF CONTENTS x LS10 B Rev 6 ...
Page 14: ......
Page 25: ...Setup Operation 1 Safety LS10 B Rev 6 13 LS10 B Figure LS10 B702S ...
Page 65: ...Setup Operation 5 Motion Range LS10 B Rev 6 53 Standard model LS10 B S ...
Page 66: ...Setup Operation 5 Motion Range 54 LS10 B Rev 6 Cleanroom model LS10 B C ...
Page 68: ......
Page 89: ...Maintenance 4 Cable LS10 B Rev 6 77 4 2 Wiring Diagrams 4 2 1 Signal Cable ...
Page 90: ...Maintenance 4 Cable 78 LS10 B Rev 6 4 2 2 Power Cable ...