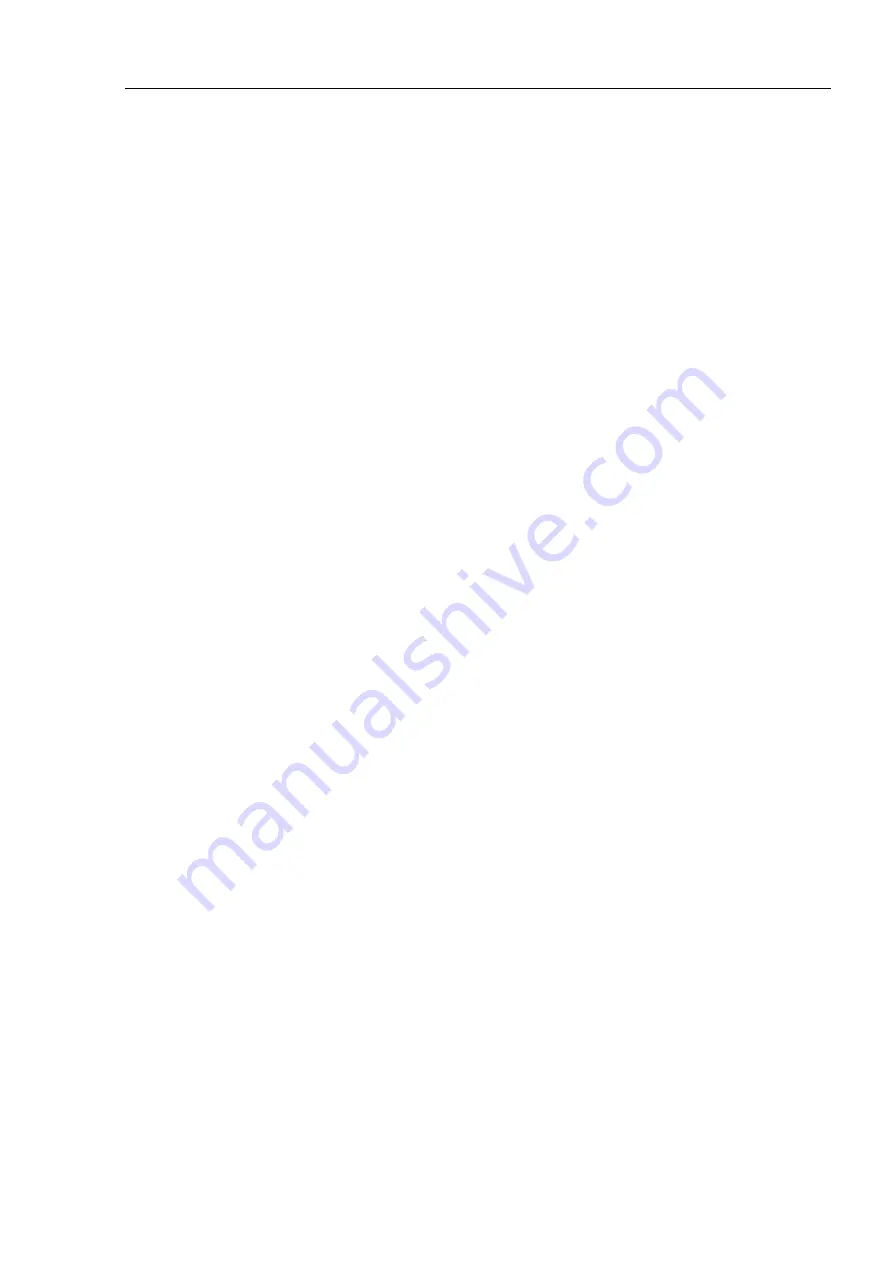
Maintenance 13. Calibration
LS10-B Rev.6
161
Calibration Using Right / Left Arm Orientations
(1) Check the point data for calibration
Use a point you can easily verify the accuracy within the work envelop of both right
and left arm. Then, check the number of points you want to use.
(2) EPSON RC+ menu-[Tools]-[Robot Manager]-[Control Panel] and click the MOTOR
ON.
(3) Click the <Free All> button to free all joints from servo control. Now, you can move
arms by hands.
(4) Move the arms to the position of point data for calibration in rightly arm orientation.
(5) From the current position, teach any point data number unused.
This point is now called P1.
Specify the point number “1” and click the <Teach> button in the [Jog & Teach].
(6) Click the Lock All in the [Control Panel] to lock all joints under servo control.
(7) Switch to the lefty arm orientation. Then, move the arm to the same point.
>Jump P1/L:Z(0) '
Change the arm orientation from righty to lefty
Z is the maximum position
* If there is interference on the way from right to lefty, click the Free All in the [Control
Panel] and change the arm orientation to lefty by hands. Then, go to the step (6),
(7).
(8) The joints are slightly out of position.
Adjust the gap with the
−
Z in the Jogging group in the [Jog & Teach]. Then, teach
another point data number unused. This point is now called P2.
Specify point number “P2” and click the <Teach> button in [Jog & Teach].
(9) Input the new Hofs value.
> Hofs Hofs (1), Hofs (2) + (Ppls(P1,2) + Ppls(P2,2)) /
2, Hofs(3), Hofs(4)
(10) From the current lefty arm orientation (the position in the step (8)), teach the point data
number used in the step (8). This point is called P2.
Specify point number “P2” and click the <Teach> button in [Jog & Teach].
(11) Switch to the righty arm orientation. Then, make sure the manipulator move to the
correct position.
>Jump P2/R
'
Change the arm orientation from lefty to righty
* If there is any interference on the way from lefty to righty, click the Free All in the
[Control Panel] and change the arm orientation to righty by hands. Then, go to the
step (6), (11).
(12) Move the manipulator to other point data and make sure it moves to the correct position.
Teach some more points if required.
* Delete the two points taught for the Joint #2 calibration.
Summary of Contents for LS10-B
Page 1: ...Rev 6 EM204R4257F SCARA ROBOT LS10 B series MANIPULATOR MANUAL ...
Page 2: ...MANIPULATOR MANUAL LS10 B series Rev 6 ...
Page 8: ...vi LS10 B Rev 6 ...
Page 12: ...TABLE OF CONTENTS x LS10 B Rev 6 ...
Page 14: ......
Page 25: ...Setup Operation 1 Safety LS10 B Rev 6 13 LS10 B Figure LS10 B702S ...
Page 65: ...Setup Operation 5 Motion Range LS10 B Rev 6 53 Standard model LS10 B S ...
Page 66: ...Setup Operation 5 Motion Range 54 LS10 B Rev 6 Cleanroom model LS10 B C ...
Page 68: ......
Page 89: ...Maintenance 4 Cable LS10 B Rev 6 77 4 2 Wiring Diagrams 4 2 1 Signal Cable ...
Page 90: ...Maintenance 4 Cable 78 LS10 B Rev 6 4 2 2 Power Cable ...