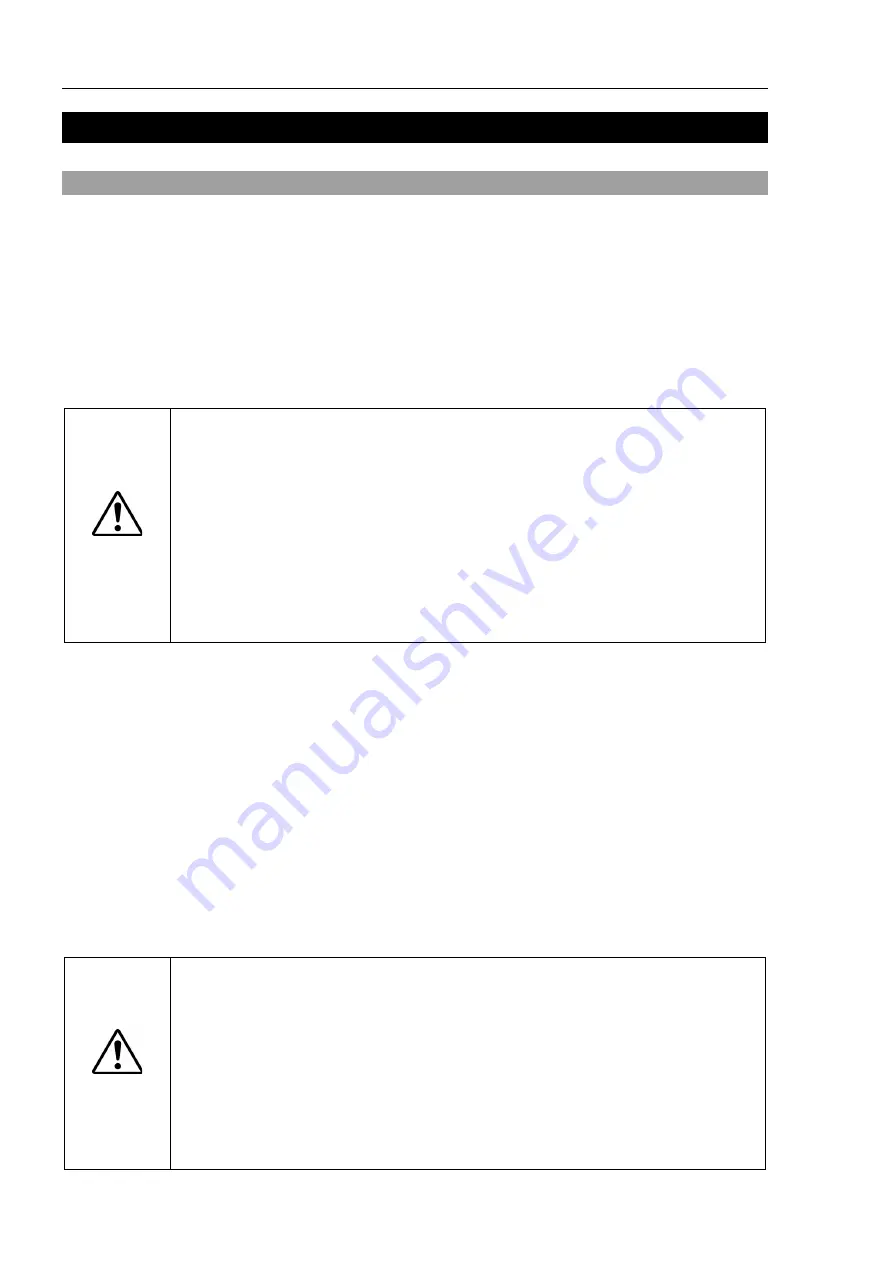
C8 Maintenance 16. Calibration
410
C Series Maintenance Manual Rev.2
16. Calibration
16.1 Overview
After parts have been replaced (motors, reduction gear units, timing belts, etc.), the
Manipulator cannot perform positioning properly because a gap exists between the origin
stored in each motor encoder and its corresponding origin stored in the Controller.
Therefore, it is necessary to match these origins after replacing the parts.
The process of aligning the two origins is called “Calibration”. Note that calibration is not
the same as teaching*.
* “Teaching” means to teach the Controller coordinate points (including poses) anywhere
in the operating area of the Manipulator.
WARNING
■
To ensure safety, a safeguard must be installed for the robot system. For details
on the safeguard, refer to the
Installation and Design Precautions
in the
Safety
chapter of the
EPSON RC+ User’s Guide
.
■
Before operating the robot system, make sure that no one is inside the
safeguarded area. The robot system can be operated in the mode for teaching
even when someone is inside the safeguarded area. The motion of the
Manipulator is always in restricted (low speeds and low power) status to secure
the safety of an operator. However, operating the robot system while someone
is inside the safeguarded area is extremely hazardous and may result in serious
safety problems in case that the Manipulator moves unexpectedly.
In EPSON RC+, a coordinate point including the arm pose is defined as “point” and its data
is called “point data”.
There are two methods to move the Manipulator during calibration.
- Releasing the electromagnetic brake and moving the arms manually.
For details, refer to the
C Series Manual C8 Manipulator 1.5 How to Move Arms with the
Electromagnetic Brake
.
- Moving the Manipulator using Jog & Teach.
Moving the Manipulator while releasing the electromagnetic brake involves risk as
described below.
It is recommended to move the Manipulator using Jog & Teach.
CAUTION
■
Normally, release the brake of joints one by one. Take extra care if you need to
release the brakes of two or more joints simultaneously. Releasing the brakes of
two or more joints simultaneously may cause hands and fingers to be caught
and/or equipment damage to or malfunction of the Manipulator as the arms of the
Manipulator may move in unexpected directions.
■
Be careful of the arm falling when releasing the brake.
While the brake is being released, the Manipulator’s arm falls by its own weight.
The arm falling may cause hands and fingers to be caught and/or may cause
equipment damage to or malfunction of the Manipulator.
Summary of Contents for C Series
Page 1: ...Rev 2 EM221R5039F 6 Axis Robots C series Maintenance Manual ...
Page 2: ...Manipulator manual C4 series Maintenance Manual Rev 2 ...
Page 20: ...Table of Contents xviii C Series Maintenance Manual Rev 2 ...
Page 22: ......
Page 69: ...C4 Maintenance 4 Cable Unit C Series Maintenance Manual Rev 2 49 ...
Page 70: ...C4 Maintenance 4 Cable Unit 50 C Series Maintenance Manual Rev 2 ...
Page 72: ...C4 Maintenance 4 Cable Unit 52 C Series Maintenance Manual Rev 2 ...
Page 73: ...C4 Maintenance 4 Cable Unit C Series Maintenance Manual Rev 2 53 ...
Page 74: ...C4 Maintenance 4 Cable Unit 54 C Series Maintenance Manual Rev 2 4 2 2 Power Cable ...
Page 75: ...C4 Maintenance 4 Cable Unit C Series Maintenance Manual Rev 2 55 ...
Page 196: ......
Page 283: ...C8 Maintenance 4 Cable Unit C Series Maintenance Manual Rev 2 263 ...
Page 284: ...C8 Maintenance 4 Cable Unit 264 C Series Maintenance Manual Rev 2 ...
Page 286: ...C8 Maintenance 4 Cable Unit 266 C Series Maintenance Manual Rev 2 C8 A1401 C8XL ...
Page 442: ...C8 Maintenance 18 C8 Option Parts List 422 C Series Maintenance Manual Rev 2 ...
Page 444: ......
Page 516: ...C12 Maintenance 4 Cable Unit 496 C Series Maintenance Manual Rev 2 ...
Page 517: ...C12 Maintenance 4 Cable Unit C Series Maintenance Manual Rev 2 497 ...
Page 518: ...C12 Maintenance 4 Cable Unit 498 C Series Maintenance Manual Rev 2 4 2 2 Power Cable ...
Page 519: ...C12 Maintenance 4 Cable Unit C Series Maintenance Manual Rev 2 499 ...