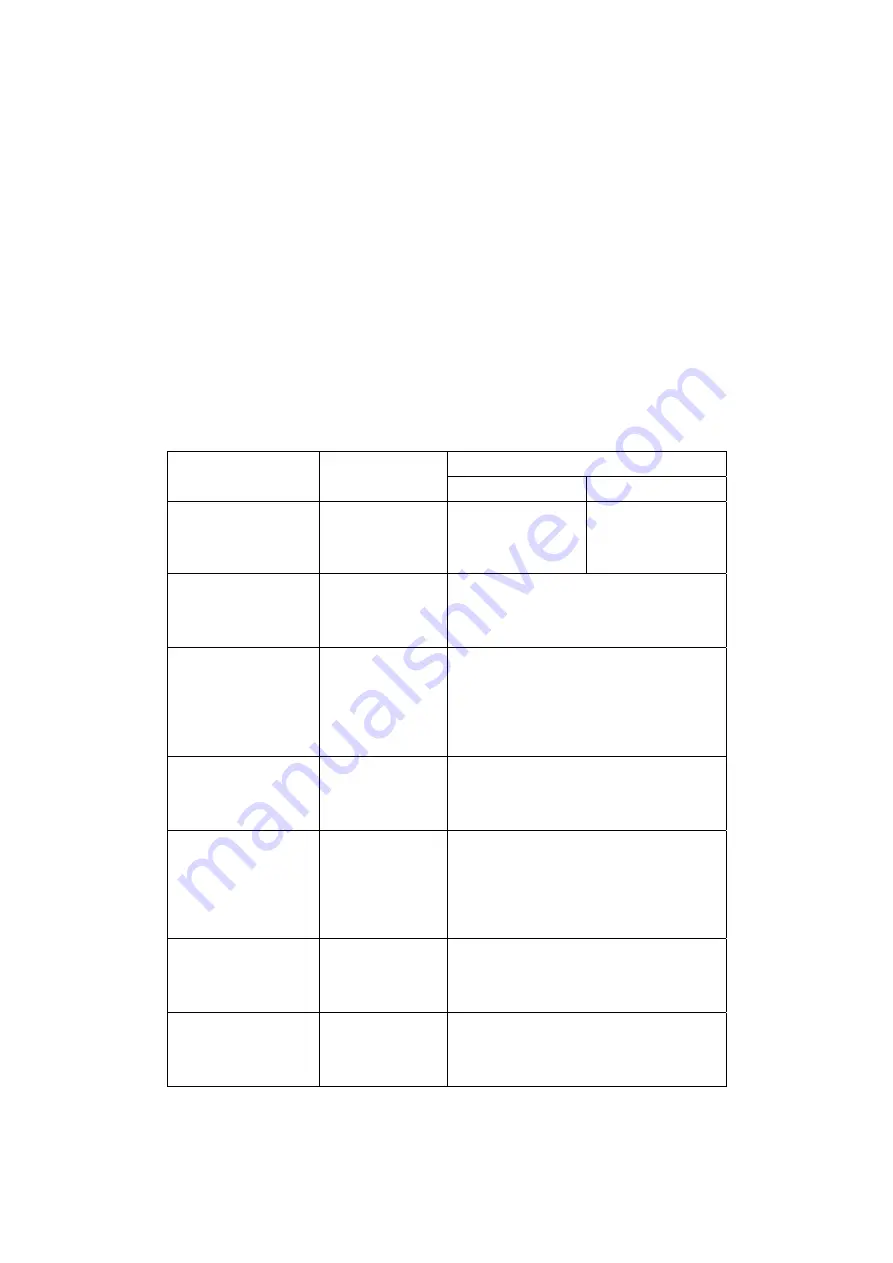
80-0000010B OM
222
4.2.7 PTO use
The rules on engagement and disengagement of rear and side semi-continuous
power take-off shafts are given in subsection 2.15 “Power take-off shafts control”.
The rear power take-off shaft operation is controlled by means of tachospeedometer
(integrated indicator) as described in subsection 2.7 “Tachospeedometer”.
ATTENTION: WHILE OPERATING WITH POWER TAKE-OFF SHAFTS, OBSERVE
ALL SAFETY MEASURES OF PTO OPERATION THAT ARE LISTED IN THE THIS OPERA-
TION MANUAL!
ATTENTION: TO PREVENT IMPACT LOADS, ENGAGE THE REAR PTO AT ENGINE
SPEED CLOSE TO MINIMUM (BETWEEN 1000 AND 1100 RPM), THEN ENGINE SPEED
SHOULD BE INCREASED.
The rear PTO of the tractor is equipped with shaft end PTO-1c under GOST 3480 (8
splines, 540 rpm). Against order, shaft end PTO-1 (6 splines, 540 rpm) and PTO-2 under
GOST 3480 (21 splines, 1000 rpm) can be attached to the tractor’s SPTA kit.
Table 4.2.1 – Rear PTO operation modes
PTO drive
Shaft end type
Rotation frequency, rpm
of PTO
of engine
Continuous
PTO 1С
PTO 1
PTO 2
540
540
1000
1632
1632
1673
Ground-speed
with rear tyres
15.5R38 mounted
PTO 1С
PTO 1
PTO 2
- 3.445 rev/m of track
Ground-speed
with rear tyres
18.4R34
of model F-11
mounted
PTO 1С
PTO 1
PTO 2
- 3.36 rev/m of track
Ground-speed
with rear tyres
18.4R30 mounted
PTO 1С
PTO 1
PTO 2
- 3.52 rev/m of track
Ground-speed
with rear tyres
18.4/78-30
(18,4 L30)
mounted
PTO 1С
PTO 1
PTO 2
- 3.59 rev/m of track
Ground-speed
with rear tyres
16.9R38 mounted
PTO 1С
PTO 1
PTO 2
- 3.23 rev/m of track
Ground-speed
with rear tyres
16.9R38 mounted
PTO 1С
PTO 1
PTO 2
- 3.70 rev/m of track
Summary of Contents for 80.1 Series
Page 1: ...BELARUS 80 1 82 1 820 80 0000010B OM OPERATION MANUAL 2015 ...
Page 15: ...80 0000010B OM 15 Figure 1 1 3 Tractor BELARUS 820 ...
Page 274: ...80 0000010B OM 274 ...
Page 378: ...80 0000010B OM 378 Service bulletins ...
Page 379: ......
Page 380: ......
Page 381: ......