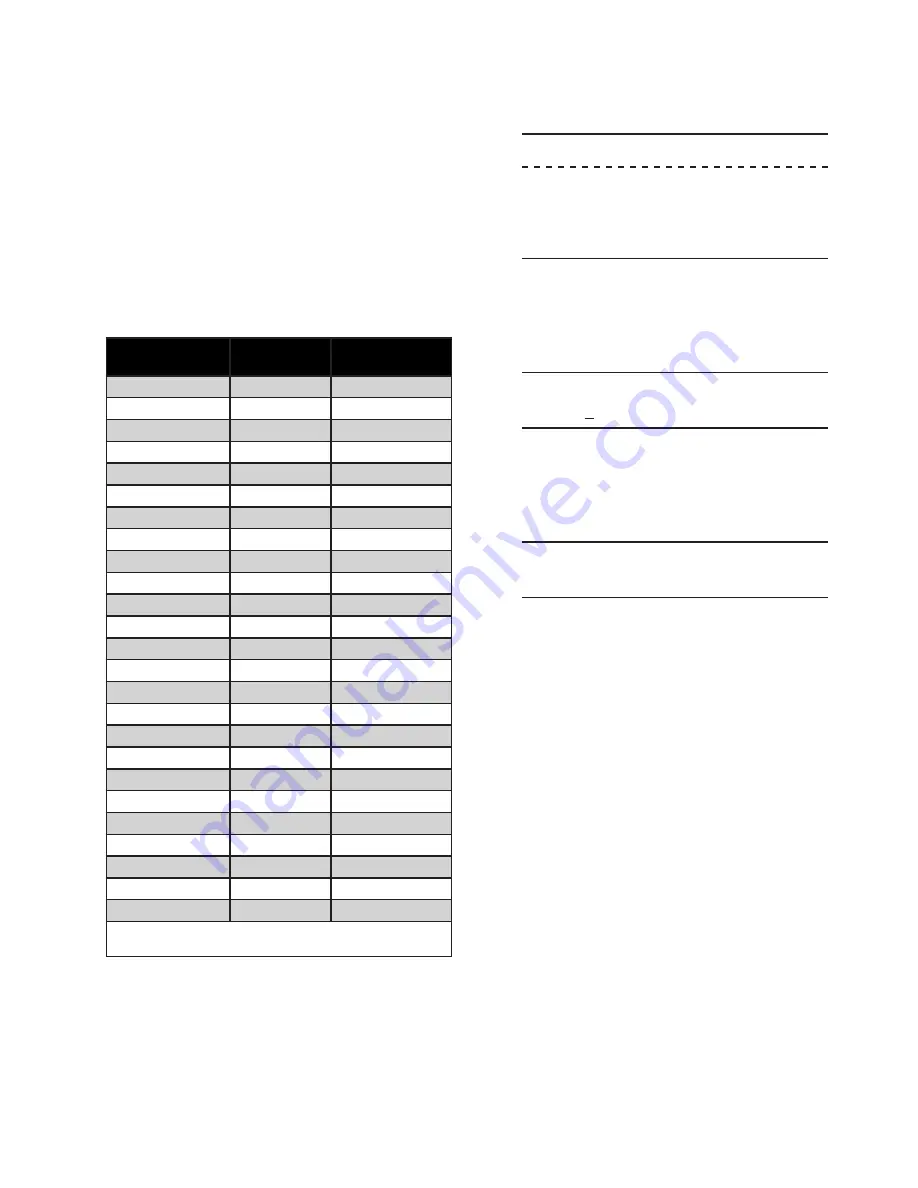
6–69
Testing – 6
Output Relay Test (Output Relays 1–23 and 25)
NOTE
: This test does not include testing of Power
Supply Relay (Output Relay 24).
1.
Ensure the protected equipment is in a
configuration/state that can support relay
output testing.
2.
Confirm the positions of the outputs in
the unoperated or
OFF
position. This can
be accomplished by connecting a DMM
(Digital Multimeter) across the appropriate
contacts and confirming open or closed.
The de-energized or
OFF
position for
outputs 1 through 25 are listed in Table 6-1.
Relay Output
Number
Normally
Open Contact
Normally Closed
Contact*
1
33-34
--
2
31-32
--
3
29-30
--
4
27-28
--
5
25-26
--
6
23-24
--
7
21-20
21-22
8
17-18
18-19
9
104-105
--
10
102-103
--
11
100-101
--
12
98-99
--
13
96-97
--
14
94-95
--
15
92-93
--
16
90-91
--
17
88-89
--
18
86-87
--
19
84-85
--
20
82-83
--
21
80-81
--
22
78-79
--
23
76-77
--
Power Supply (24)
--
12-13
Self-Test (25)
14-15
15-16
* “Normal” position of the contact corresponds to the OFF
(de-energized) state of the relay.
Table 6‑1 Output Contacts
3.
If the relay is already in the Diagnostic
Mode, then go to Step 4.
If the relay is NOT in the Diagnostic Mode,
then enter the relay diagnostic mode by
performing the steps described in the
Entering Relay Diagnostic Mode section
of this chapter, then go to Step 4.
4.
Ensure that the Diagnostic Menu is
selected to OUTPUT (Upper Case).
OUTPUT TEST (RELAY)
OUTPUT
input led target
button disp
com1 com2 com3 clock
led cal factory
If OUTPUT is not selected (Upper Case),
then use the Right/Left arrow pushbuttons
to select OUTPUT.
5. Press
ENTER
, the relay will display the
following:
RELAY NUMBER
1
6.
Select the Output Relay (from Table 6-1)
to be tested, utilizing the Up/Down arrow
pushbuttons.
7. Press
ENTER
. The following will be
displayed for the selected relay:
RELAY NUMBER 1
OFF on
8. Select
ON
(Upper Case) utilizing the Right
arrow pushbutton. The relay will respond
as follows:
a. Output relay energizes (On position)
b. Appropriate red
OUTPUT
LED
illuminates, if equipped.
If testing all output relays, then press
EXIT
to return to the output relay selection
menu, then repeat Steps 6, 7 and 8 for
each output relay.
9.
The DMM can now be used to verify that
the output relay contact is in the operated
or
ON
position. The readings should be the
opposite of the initial reading determined
in Step 2.
10.
When output relay testing is complete
then restore all output relays to their
de-energized or
OFF
positions listed in
Table 6-1 and press
EXIT
to return to the
Diagnostic Menu.
11.
If all Diagnostic Testing is complete, then
exit the diagnostic menu by pressing
EXIT
,
PRESS EXIT TO EXIT DIAGNOSTIC
MODE
is displayed, then press
EXIT
a
second time.
Summary of Contents for M-3425A
Page 1: ...Instruction Book M 3425A Generator Protection ...
Page 38: ...This Page Left Intentionally Blank ...
Page 43: ...This Page Left Intentionally Blank ...
Page 57: ...xiv M 3425A Instruction Book This Page Left Intentionally Blank ...
Page 63: ...M 3425A Instruction Book 1 6 This Page Left Intentionally Blank ...
Page 95: ...M 3425A Instruction Book 2 32 This Page Left Intentionally Blank ...
Page 97: ...M 3425A Instruction Book 3 2 Figure 3 2 IPScom Main Screen ...
Page 123: ...M 3425A Instruction Book 3 28 Figure 3 30 View Sequence of Events Recorder Screen ...
Page 131: ...M 3425A Instruction Book 3 36 This Page Left Intentionally Blank ...
Page 162: ...4 31 System Setup and Setpoints 4 Figure 4 15 IPScom Relay Setup System Dialog Screen ...
Page 183: ...4 52 M 3425A Instruction Book Figure 4 32 Volts Per Hertz 24 Setpoint Ranges ...
Page 187: ...4 56 M 3425A Instruction Book Figure 4 34 Sync Check 25 Setpoint Ranges ...
Page 202: ...4 71 System Setup and Setpoints 4 Figure 4 50 49 Function Overload Curves ...
Page 203: ...4 72 M 3425A Instruction Book Figure 4 51 Stator Thermal Protection 49 Setpoint Ranges ...
Page 215: ...4 84 M 3425A Instruction Book Figure 4 62 Phase Overvoltage 59 Setpoint Ranges ...
Page 239: ...4 108 M 3425A Instruction Book Figure 4 80 Out of Step 78 Setpoint Ranges ...
Page 242: ...4 111 System Setup and Setpoints 4 Figure 4 82 Frequency 81 Setpoint Ranges ...
Page 261: ...M 3425A Instruction Book 5 6 Figure 5 5 Mounting Dimensions for GE L 2 Cabinet H3 and H4 ...
Page 277: ...M 3425A Instruction Book 5 22 Figure 5 14 M 3425A Circuit Board ...
Page 278: ...Installation 5 5 23 Figure 5 15 M 3425A Circuit Board Expanded I O ...
Page 280: ...Installation 5 5 25 Figure 5 17 20 Hz Frequency Generator Housing Panel Surface Mount ...
Page 281: ...M 3425A Instruction Book 5 26 Figure 5 18 20 Hz Frequency Generator Housing Panel Flush Mount ...
Page 282: ...Installation 5 5 27 Figure 5 19 20 Hz Band Pass Filter Housing Panel Surface Mount ...
Page 283: ...M 3425A Instruction Book 5 28 Figure 5 20 20 Hz Band Pass Filter Housing Panel Flush Mount ...
Page 284: ...Installation 5 5 29 Figure 5 21 20 Hz Measuring Current Transformer 400 5 A CT ...
Page 421: ...D 2 M 3425A Instruction Book Figure D 1 Volts Hz 24 Inverse Curve Family 1 Inverse Square ...
Page 422: ...Inverse Time Curves Appendix D D 3 Figure D 2 Volts Hz 24 Inverse Family Curve 2 ...
Page 423: ...D 4 M 3425A Instruction Book Figure D 3 Volts Hz 24IT Inverse Curve Family 3 ...
Page 424: ...Inverse Time Curves Appendix D D 5 Figure D 4 Volts Hz 24IT Inverse Curve Family 4 ...
Page 427: ...D 8 M 3425A Instruction Book Figure D 5 BECO Definite Time Overcurrent Curve ...
Page 428: ...Inverse Time Curves Appendix D D 9 Figure D 6 BECO Inverse Time Overcurrent Curve ...
Page 429: ...D 10 M 3425A Instruction Book Figure D 7 BECO Very Inverse Time Overcurrent Curve ...
Page 430: ...Inverse Time Curves Appendix D D 11 Figure D 8 BECO Extremely Inverse Time Overcurrent Curve ...
Page 437: ...D 18 M 3425A Instruction Book Figure D 15 IEEE Extremely Inverse Time Overcurrent Curves ...
Page 469: ...F 30 M 3425A Instruction Book This Page Left Intentionally Blank ...
Page 479: ...H 2 M 3425A Instruction Book This Page Left Intentionally Blank ...