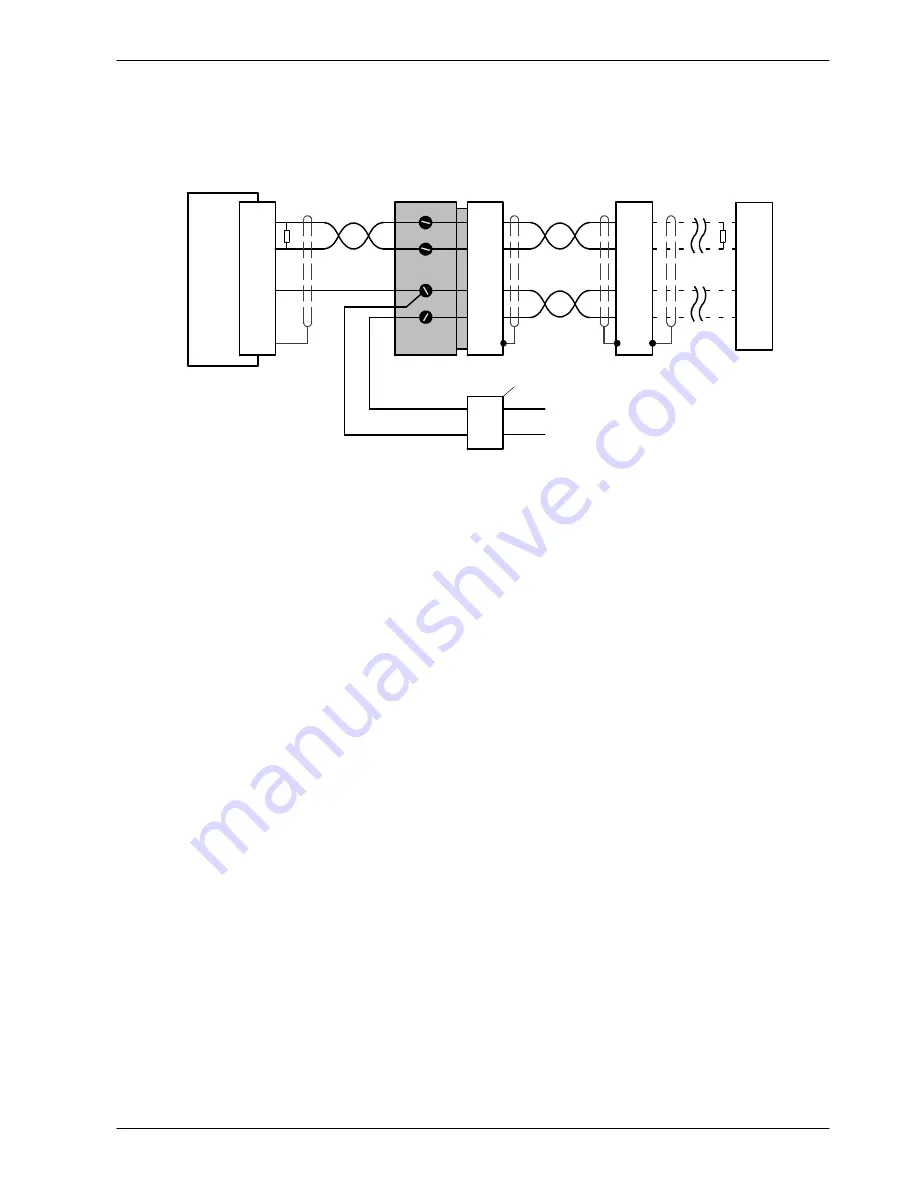
www.baldormotion.com
Input / Output 5-21
MN1942
Figure 43 shows a typical CANopen network with a NextMove
e
100 manager node, one
MicroFlex
e
100 slave node and a Baldor HMI operator panel:
7
2
6
9
NextMove
e
100
D-type
7
2
Baldor HMI
Operator Panel
Twisted pair
Twisted pairs
T
R
T
R
End
node
7
2
6
9
7
2
6
9
MicroFlex
e
100
D-type
6
5
CANopen
D-type
5
5
2
1
‘X1’
24 V
0 V
Phoenix
SUBCON-PLUS F3
Figure 43 - Typical CANopen network connections
Note:
The MicroFlex
e
100 CAN channel is opto-isolated, so a voltage in the range 12-24 V
must be applied between pin 9 and pin 6 of the CAN connector.
The configuration and management of a CANopen network must be carried out by a single node
acting as the network manager (for example NextMove
e
100), or by a third party CANopen
manager device.
Up to 126 CANopen nodes (node IDs 2 to 127) can be added to the network by the manager node
using the Mint
NODESCAN
keyword. If successful, the nodes can then be connected to using the
Mint
CONNECT
keyword. Any network and node related events can then be monitored using the
Mint
BUS1
event.
Note:
All CAN related Mint keywords are referenced to CANopen using the ‘bus’ dot
parameter. For CANopen the ‘bus’ dot parameter must be set to 1.
Please refer to the Mint help file for further details on CANopen, Mint keywords and dot
parameters.
Summary of Contents for MicroFlex e100
Page 1: ......
Page 2: ......
Page 14: ...www baldormotion com 2 4 Introduction MN1942...
Page 80: ...www baldormotion com 5 26 Input Output MN1942...
Page 108: ...www baldormotion com 6 28 Configuration MN1942...
Page 116: ...www baldormotion com 7 8 Troubleshooting MN1942...
Page 124: ...www baldormotion com 8 8 Specifications MN1942...
Page 142: ...www baldormotion com B 6 Control System MN1942...
Page 170: ...Comments MN1942 Thank you for taking the time to help us...
Page 171: ......
Page 172: ......