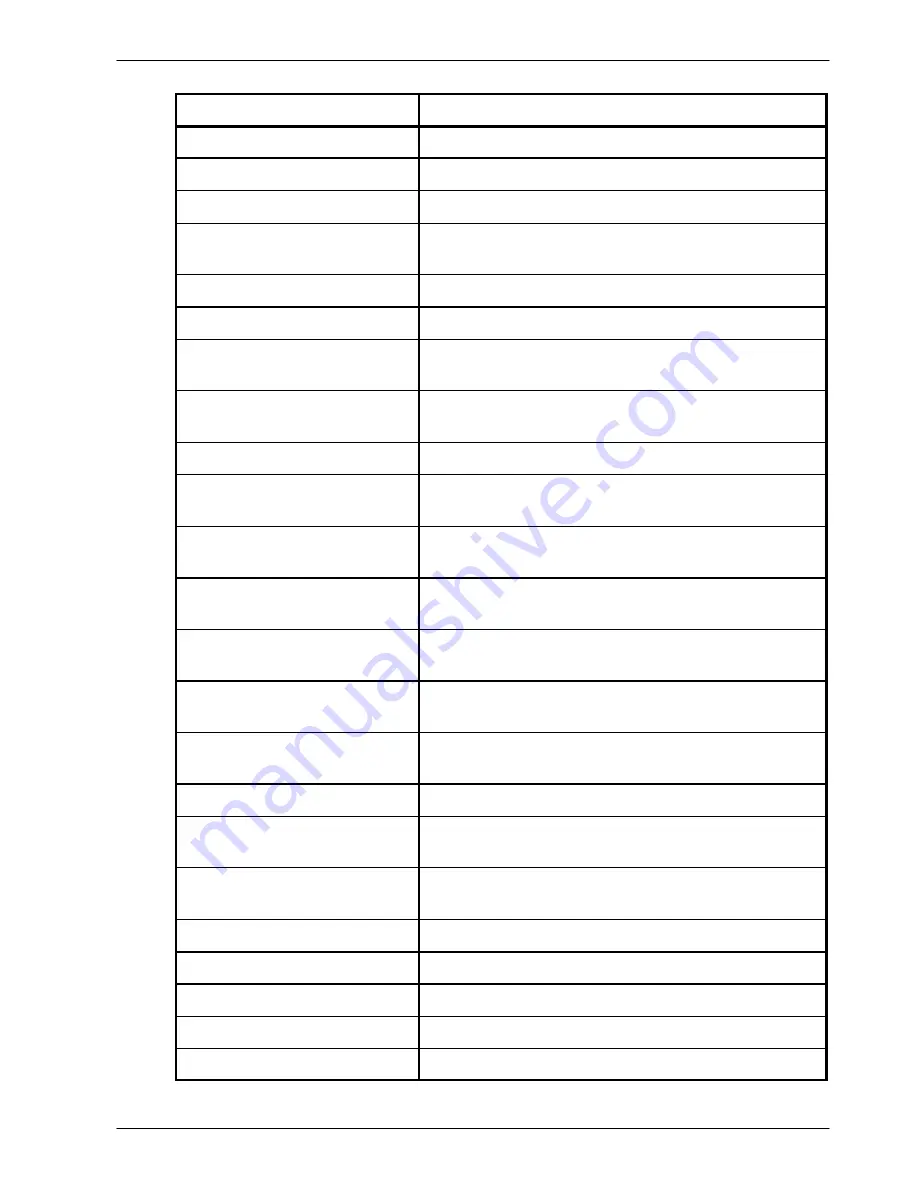
www.baldormotion.com
Mint Keyword Summary C-5
MN1943
Keyword
Description
ENCODERSCALE
To set or read the scale factor for the encoder channel.
ENCODERTYPE
To set or read the feedback type of the motor.
ENCODERVEL
To read the velocity from an encoder channel.
ENCODERWRAP
To set or read the encoder wrap range for the encoder
channel.
ENCODERZLATCH
To get and reset the state of an axis’ encoder Z latch.
ERRCODE
To return the last error code read from the error list.
ERRDATA
To return data associated with the last error read from
the error list.
ERRLINE
To return the line number of the last error read from the
error list.
ERRORCLEAR
To clear all errors in the specified group.
ERRORDECEL
To set the deceleration rate on the axis for powered
stops, in the event of an error or stop input.
ERRORINPUT
To set or return the digital input to be used as the error
input for the specified axis.
ERRORINPUTMODE
To control the default action taken in the event of an
external error input.
ERRORPRESENT
To determine if errors in a particular group are present in
the error list.
ERRORREADCODE
To determine if a particular error is present in the error
list.
ERRORREADNEXT
Returns the next entry in the specified group from the
error list.
ERRORSWITCH
To return the state of the error input.
ERRSTRING
To return the error string for the last error code read from
the error list.
ERRTIME
To return the time stamp for the last error code read
from the error list.
EVENTACTIVE
To indicate whether an event is currently active.
EVENTDISABLE
To selectively enable and disable Mint events.
EVENTPEND
To manually cause an event to occur.
EVENTPENDING
To indicate whether an event is currently pending.
FACTORYDEFAULTS
To reset parameter table entries to their default values.
Summary of Contents for MicroFlex e100
Page 1: ......
Page 2: ......
Page 14: ...www baldormotion com 2 4 Introduction MN1942...
Page 80: ...www baldormotion com 5 26 Input Output MN1942...
Page 108: ...www baldormotion com 6 28 Configuration MN1942...
Page 116: ...www baldormotion com 7 8 Troubleshooting MN1942...
Page 124: ...www baldormotion com 8 8 Specifications MN1942...
Page 142: ...www baldormotion com B 6 Control System MN1942...
Page 170: ...Comments MN1942 Thank you for taking the time to help us...
Page 171: ......
Page 172: ......