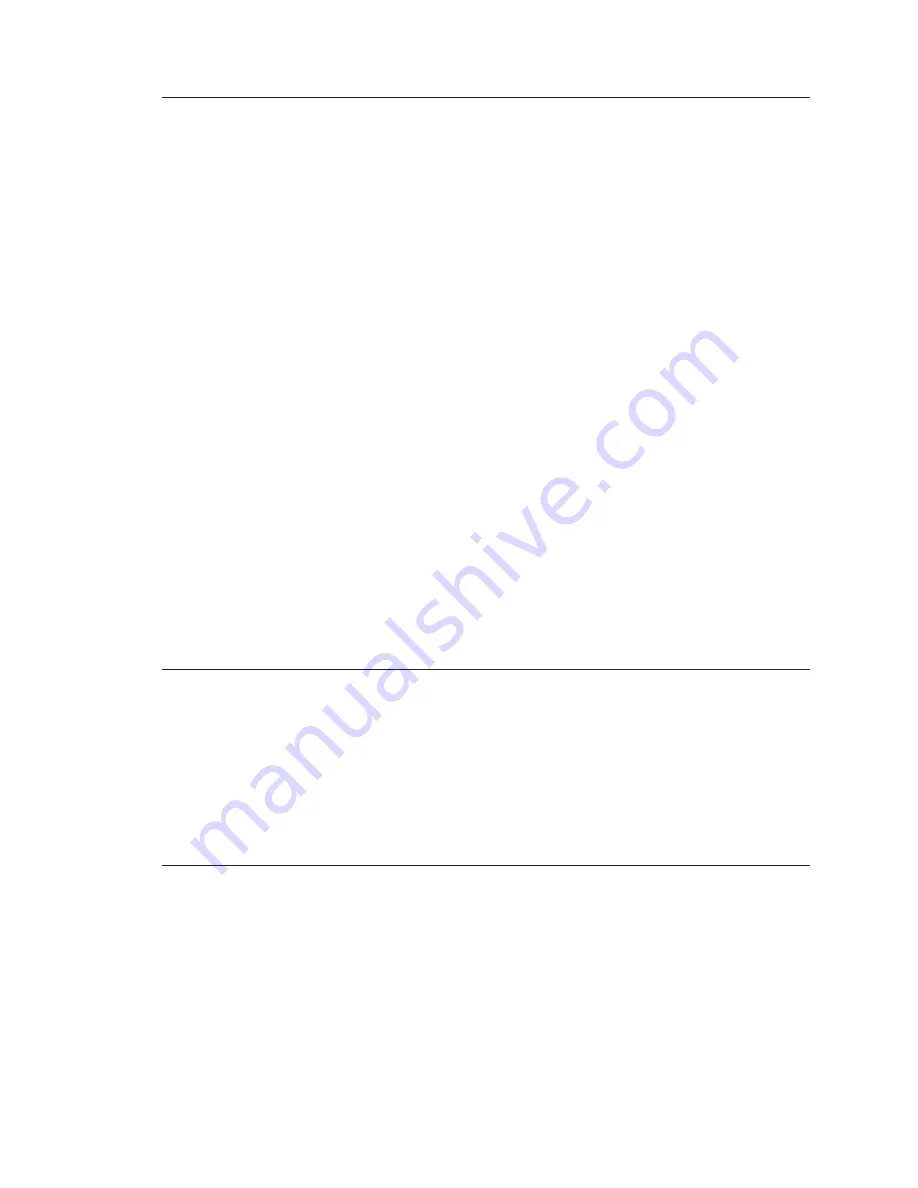
Maintenance & Troubleshooting | 5-29
Condition/Alarm Name
Description & Suggested Corrective Action
Corrective
Action
(continued):
•
Take appropriate safety precautions, open the Electronics Enclosure
door, and:
- Check the fuse(s) for the zone(s) which caused the alarm (i.e.,
Bench Heater
or
Oven Heater
, if used). Refer to the Fuse Legend
at the back of the Electronics Enclosure for the locations of these
fuses.
•
Other checks/corrective action:
- Using an Ohm Meter, measure the
resistance of the associated
RTD (Cell, Bench, or Oven) and test it for an open circuit.
If the
RTD is faulty, contact AMETEK for assistance.
- Check the electrical connections between the heater and the
Relay
board. Check for proper connections and damage to the wiring.
-
Replace
the
Relay
board.
Contact AMETEK for assistance.
-
Replace
the
Customer Connection
board.
Contact AMETEK for
assistance.
For alarms caused by
High
temperatures only:
•
If the Oven Heater temperature-controlled zone has exceeded its
over-temperature limit of 177 °C/350 °F, the analyzer automatically
switches to
Zero Gas Flush
mode.
Take appropriate safety precautions, open the Electronics Enclosure
door, and:
- Manually reset the alarm by pressing the OT (Over-Temperature)
Reset Switch,
S501
, on the
Relay
board (see Figure 5-4) to re-
energize the tripped Oven Heater circuit.
- Check the LEDs for the Oven Heater Over-Temp circuit (
D502
on
the
Relay
board) to check if it is experiencing problems.
- Check the fuse for the Over-Temperature circuit (
F3
, located at
TB1
13
). Refer to the Fuse Legend for the locations of these fuses.
Pressure transducer 1
Pressure transducer 2
These alarm conditions indicate that the concentration of the output
exceeds its full-scale range by more than 10 psia (typical; set point and
pressure unit may vary).
Corrective Action:
•
The parameters have exceeded the normal operating range. From the
User Interface Panel, check that the full-scale range is correct for the
current sample. If
Pressure Transducer
alarms persist during normal
operation, contact the factory. A range change and recalibration may
be required.
Summary of Contents for IPS-4-UV
Page 15: ...Contents xv...
Page 16: ...xvi IPS 4 UV Analyzer GPDiv2 This page intentionally left blank...
Page 24: ...1 8 IPS 4 UV Analyzer GPDiv2 This page intentionally left blank...
Page 66: ...3 36 IPS 4 UV Analyzer GPDiv2 This page intentionally left blank...
Page 144: ...6 6 IPS 4 UV Analyzer GPDiv2 This page intentionally left blank...
Page 180: ...A 2 IPS 4 UV Analyzer GPDiv2 Analyzer Light Path Schematic...
Page 183: ...Appendix Drawings A 5 Detector Interface Board 100 1937...
Page 184: ...A 6 IPS 4 UV Analyzer GPDiv2 Detector Board 100 1955...
Page 185: ...Appendix Drawings A 7 Display Interface Board 100 1978...
Page 186: ...A 8 IPS 4 UV Analyzer GPDiv2 Customer Connection Board 100 1971...
Page 187: ...Appendix Drawings A 9 Relay Board 100 1942...
Page 188: ...A 10 IPS 4 UV Analyzer GPDiv2 Analog Board 100 1922...
Page 189: ...Appendix Drawings A 11 MCU Board 100 1914...
Page 190: ...A 12 IPS 4 UV Analyzer GPDiv2 Xenon Lamp Board 100 2061...
Page 191: ...Appendix Drawings A 13 Electronics Enclosure Wiring Diagram Sheet 1 of 3 WX 102877...
Page 192: ...A 14 IPS 4 UV Analyzer GPDiv2 Electronics Enclosure Wiring Diagram Sheet 2 of 3 WX 102877...
Page 193: ...Appendix Drawings A 15 Electronics Enclosure Wiring Diagram Sheet 3 of 3 WX 102877...
Page 194: ...A 16 IPS 4 UV Analyzer GPDiv2 This page intentionally left blank...
Page 196: ...S 2 IPS 4 UV Analyzer GPDiv2 This page intentionally left blank...