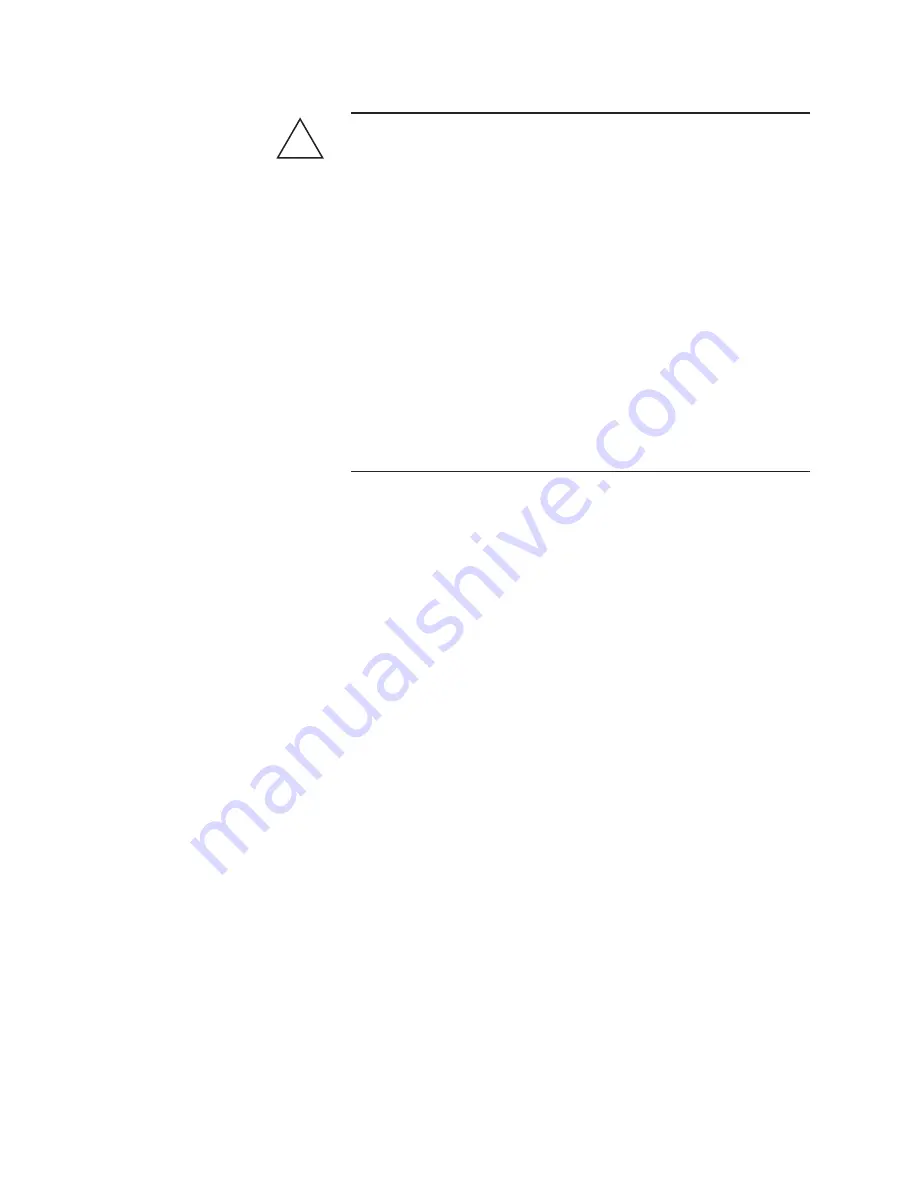
Maintenance & Troubleshooting | 5-5
Before Performing Maintenance
Under normal operating conditions, lethal concentrations of H
2
S
or other toxic gases/liquids from the sample stream may be present
within the analyzer sample system.
Before working on the sample system, manually Zero the analyzer
(from the
Calibration
screen, select
Start zero calibration
and press
ENTER
), isolate it (block it in) from the sample stream, and disconnect
the main AC power. This procedure is necessary prior to changing out
any analyzer components or replacing any replaceable parts (as part
of regular preventive maintenance), or performing leak checks follow-
ing the replacement of instrument air or other adjustments to any of
the connections points in the analyzer sample system.
If this is not
possible, a breathing apparatus must be worn while servicing
the sample system.
The sample system is defined as all components in the analyzer sys-
tem through which sample fluid passes.
Locating a Plug in the Sample System
If analyzer problems occur, they are most likely related to improper
sample system operation, such as plugs or leaks. Plugs in the sample sys-
tem cause problems in analyzer response time, either to changing process
conditions or to Zero fluid. Leaks are potentially dangerous and will even-
tually lead to corrosion problems.
Detecting a Plug in the Sample System
This is best done by observing the analyzer measurement response time
immediately following a Zero function. A typical response is
less than 30
seconds to T90
. Observe your analyzer and learn what a normal response
time is. Use the recorded response time as a reference for detecting the
formation of plugs in the sample system.
If the sample response time is longer than normal, it is most likely due
to plugging somewhere in the sample system. The next step is to locate
and remove the plug. The portion of the sample system with the high-
est risk of plugging is the sample inlet and the portion of the sample inlet
most prone to plugging is the valve on the sample probe or process tap.
One way to confirm that a plug is in the sample inlet is to close the Vent
Line Shut Off valve (in the Oven/Sample System Enclosure) and Zero the
analyzer.
!
WARNING
Summary of Contents for IPS-4-UV
Page 15: ...Contents xv...
Page 16: ...xvi IPS 4 UV Analyzer GPDiv2 This page intentionally left blank...
Page 24: ...1 8 IPS 4 UV Analyzer GPDiv2 This page intentionally left blank...
Page 66: ...3 36 IPS 4 UV Analyzer GPDiv2 This page intentionally left blank...
Page 144: ...6 6 IPS 4 UV Analyzer GPDiv2 This page intentionally left blank...
Page 180: ...A 2 IPS 4 UV Analyzer GPDiv2 Analyzer Light Path Schematic...
Page 183: ...Appendix Drawings A 5 Detector Interface Board 100 1937...
Page 184: ...A 6 IPS 4 UV Analyzer GPDiv2 Detector Board 100 1955...
Page 185: ...Appendix Drawings A 7 Display Interface Board 100 1978...
Page 186: ...A 8 IPS 4 UV Analyzer GPDiv2 Customer Connection Board 100 1971...
Page 187: ...Appendix Drawings A 9 Relay Board 100 1942...
Page 188: ...A 10 IPS 4 UV Analyzer GPDiv2 Analog Board 100 1922...
Page 189: ...Appendix Drawings A 11 MCU Board 100 1914...
Page 190: ...A 12 IPS 4 UV Analyzer GPDiv2 Xenon Lamp Board 100 2061...
Page 191: ...Appendix Drawings A 13 Electronics Enclosure Wiring Diagram Sheet 1 of 3 WX 102877...
Page 192: ...A 14 IPS 4 UV Analyzer GPDiv2 Electronics Enclosure Wiring Diagram Sheet 2 of 3 WX 102877...
Page 193: ...Appendix Drawings A 15 Electronics Enclosure Wiring Diagram Sheet 3 of 3 WX 102877...
Page 194: ...A 16 IPS 4 UV Analyzer GPDiv2 This page intentionally left blank...
Page 196: ...S 2 IPS 4 UV Analyzer GPDiv2 This page intentionally left blank...