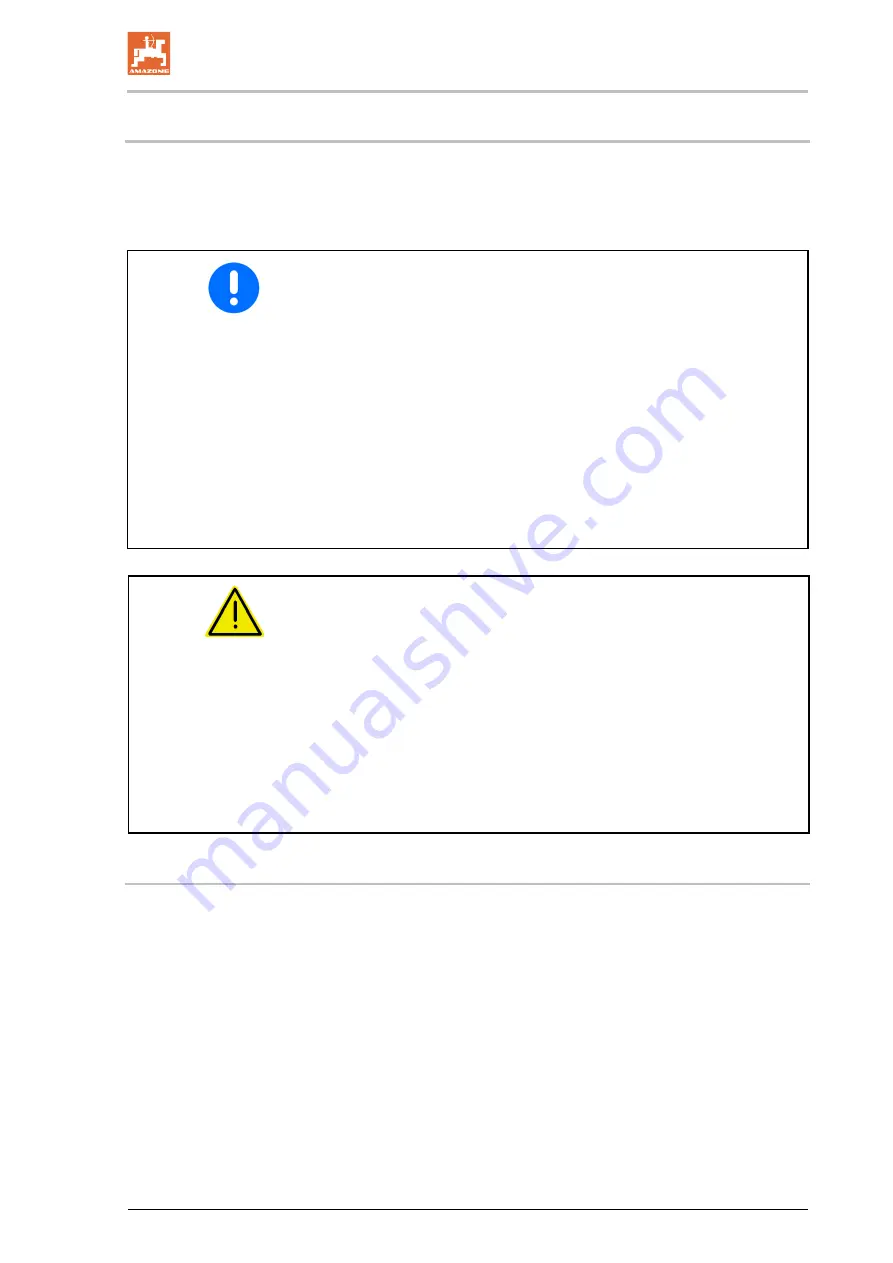
Commissioning
UF02 BAG00225.3 09.22
115
7 Commissioning
This section contains information
on commissioning your machine.
on checking if it is possible to connect the machine to your trac-
tor.
Before operating the machine for the first time the operator must
have read and understood the operating manual.
Comply with the section "Safety information for the user", start-
ing on page 30 when
coupling and uncoupling the machine
transporting the machine
using the machine
Only couple and transport the machine to a tractor which is suit-
able for the task.
The tractor and machine must meet the national road traffic reg-
ulations.
The operator and the user shall be responsible for compliance
with the statutory road traffic regulations.
WARNING
Risk of crushing, shearing, cutting, and being drawn in or
trapped in the vicinity of hydraulically or electrically actuated
components.
Do not block the operator controls on the tractor which are used for
hydraulic and electrical movements of components, e.g. folding, swiv-
elling and pushing movements. The movement must stop automati-
cally when you release the appropriate control. This does not apply to
equipment movements that:
are continuous or
are automatically locked or
require a floating position or pressed position to function
7.1
Antifreeze in the spray liquid tank
Depending on the season and marking on the implement, the imple-
ment is protected with a biodegradable antifreeze against damage
due to freezing temperatures.
The antifreeze can be sprayed out with the spray liquid at first use or
pumped out.
Antifreeze that was pumped out can be reused or disposed of
properly.
Summary of Contents for UF 1002
Page 20: ...General safety instructions 20 UF02 BAG00225 3 09 22 Super S boom...
Page 21: ...General safety instructions UF02 BAG00225 3 09 22 21 Q Plus boom...
Page 217: ...Liquid circuit UF02 BAG00225 3 09 22 217 Part width section control...
Page 218: ...Liquid circuit 218 UF02 BAG00225 3 09 22 Single nozzle control Flushing water pump...
Page 219: ...Liquid circuit UF02 BAG00225 3 09 22 219 Single nozzle control FlowControl...
Page 223: ...Spray table UF02 BAG00225 3 09 22 223...
Page 232: ......