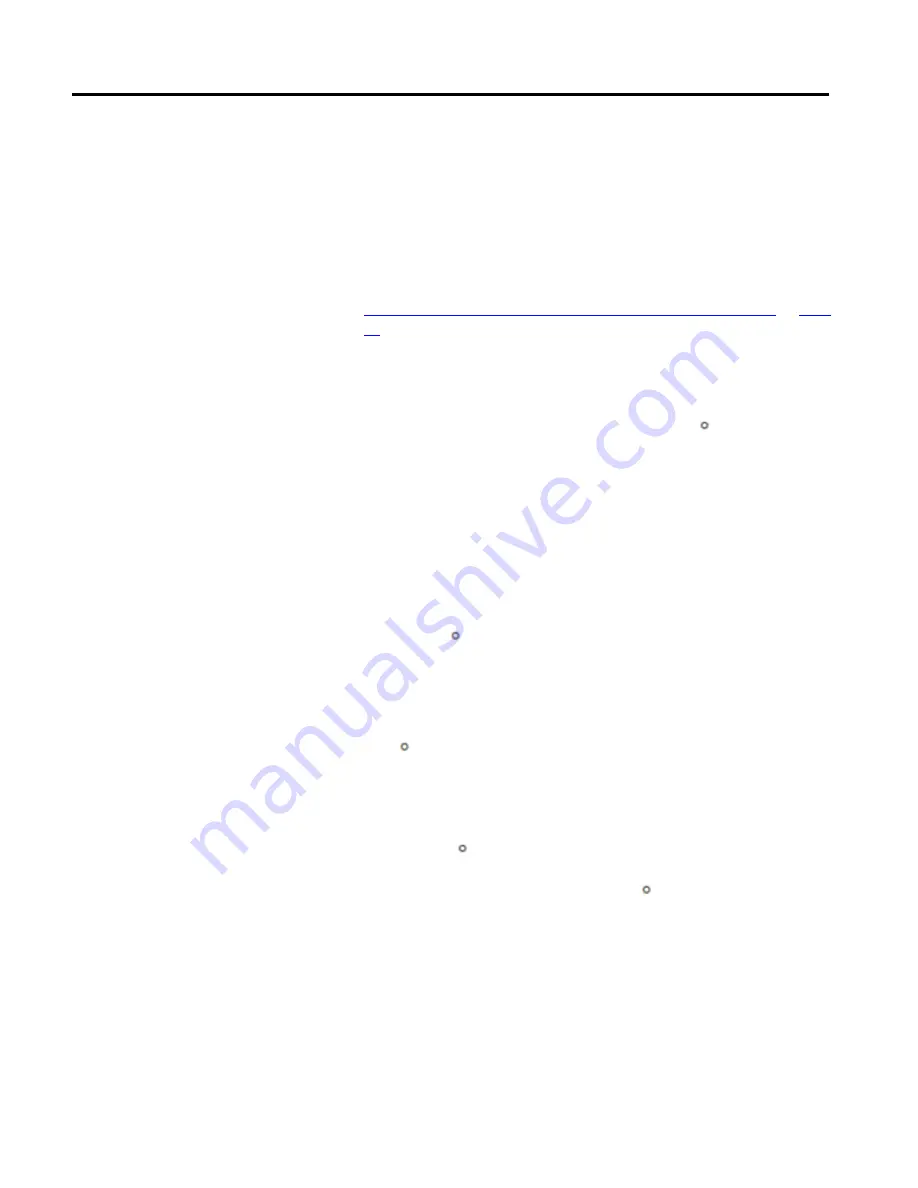
Chapter 3
Geometries with no orientation support
90
Rockwell Automation Publication MOTION-UM002F-EN-P - February 2018
4.
Move each joint to an absolute position of 0.0. Verify that each joint
position reads 0 degrees and the respective L1 is in a horizontal position.
If L1 is not in a horizontal position, see the alternate method for calibrating
a Delta three-dimensional robot.
See also
Alternate method for calibrating a Delta Three-dimensional robot
Rotate each joint to a position so that the respective link is at a horizontal
position. Perform one of the following:
•
Use an MRP instruction to set all the joint angles to 0 at this position.
•
Configure the values for the Zero Angle Offsets on the
Geometry
tab in the
Coordinate System Properties
dialog box equal to the values of the joints
in a horizontal position.
For Delta robot geometries, the internal transformation equations in the Logix
Designer application are written assuming that:
•
Joints are at 0 when link L1 is horizontal.
•
As each top link (L1) moves downward, its corresponding joint axis (J1, J2,
or J3) is rotating in the positive direction.
If you want the joint angular position when L1 is horizontal to be at any other
value than 0 , then configure the zero angle orientation values on the
Geometry
tab on
Coordinate System Properties
dialog box to align the joint angle positions
with the internal equations.
For example, if the Delta robot is mounted so that the joints attached at the top
plate are homed at 30 in the positive direction below horizontal and you want
the Logix Designer application readout values to be zero in this position, then
configure the Zero Angle Orientation values to -30 on the
Geometry
tab on the
Coordinate System Properties
dialog box.
Alternate method for
calibrating a Delta
Three-dimensional robot
Configure Zero Angle
Orientations for Delta
Three-dimensional robot