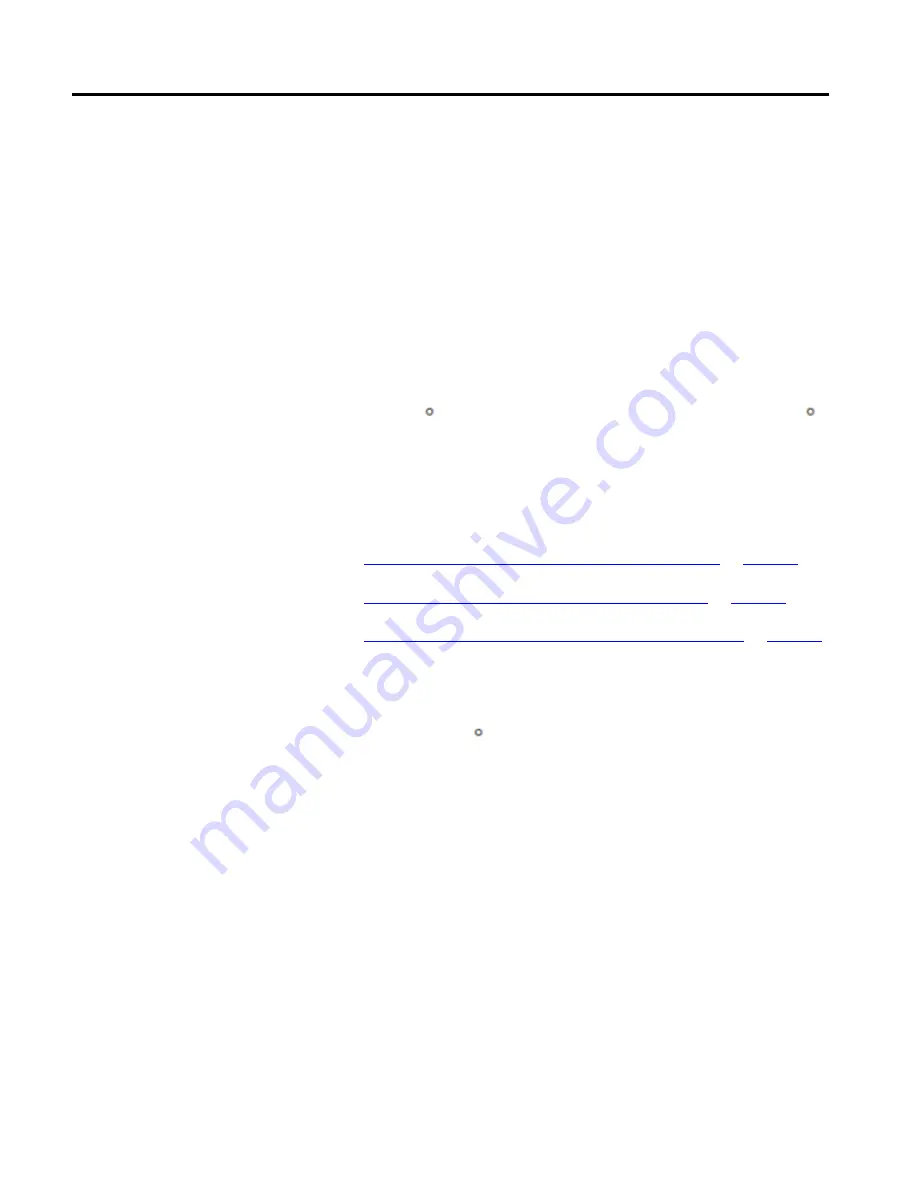
Geometries with no orientation support
Chapter 3
Rockwell Automation Publication MOTION-UM002F-EN-P - February 2018
113
1.
Configure CS1 to contain the virtual X1 and X2 axes.
2.
Configure CS2 to contain the real X1 and X2 axes.
3.
Configure the Orientation vector of the MCT instruction as (0,0, -45), a
negative degree rotation around the X3 axis.
4.
Configure the Translation vector as (0, 0, 0).
5.
Link the CS1 and CS2 by using a MCT instruction.
6.
Home the H-bot and then program all moves in CS1.
The machine moves the tool center point (TCP) to the programmed coordinates
in CS2. The -45 rotation introduced by the Kinematics, counteracts the 45
rotation introduced by the mechanics of the machine and the H-bot moves to the
CS1 configured coordinates. As a result, a programmed move of X1virt=10,
X2virt=5 moves to a real mechanical position of X1=10, X2=5.
See also
Establish the reference frame for a Cartesian H-bot robot
on
Identify the work envelope for a Cartesian H-bot robot
Define configuration parameters for a Cartesian H-bot robot
For a Cartesian H-bot, the Base coordinate system is an orthogonal set of X1, X2
axes postponed anywhere on the Cartesian H-bot. The angular rotation of the
reference frame may not be rotated for this robot since the angular rotation vector
is used to achieve the 45 rotation required for the mechanical operation.
The work envelope for a Cartesian H-bot is a rectangle of length and width equal
to the axis soft travel limits.
Defining the link lengths, base offset, or end-effector offset configuration
parameters is not required for a Cartesian H-bot robot.
Establish the reference frame
for a Cartesian H-bot
Identify the work envelope for
a Cartesian H-bot
Define configuration
parameters for a Cartesian
H-bot robot