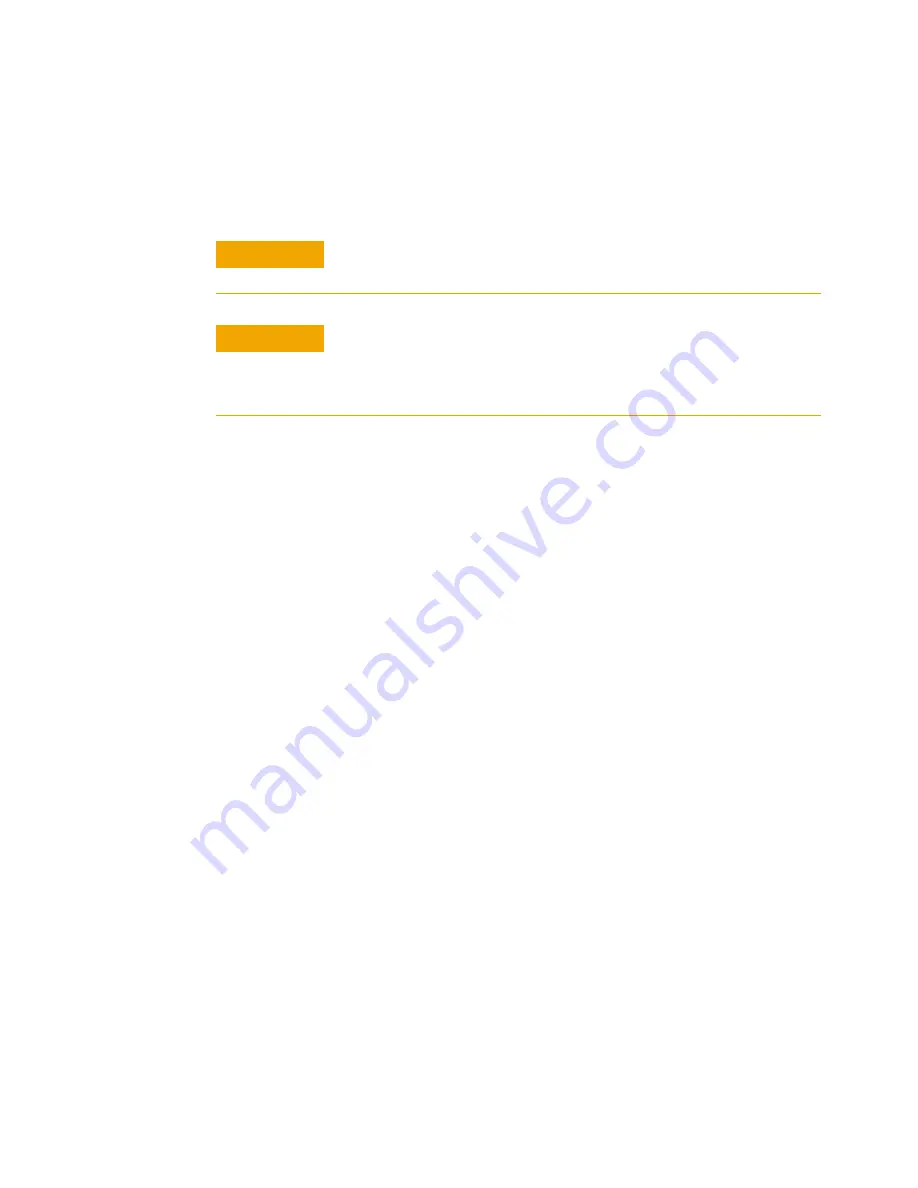
General Maintenance
10
Troubleshooting and Maintenance Guide
161
Take extra precautions, such as a grounded antistatic mat, if
you must work on components or assemblies that have been
removed from the MSD. This includes the analyzer.
More information is available
If you need more information about the functions of electronic
components, refer to
Most of the procedures in this chapter are illustrated with video
clips.
C A U T I O N
In order to be effective, an antistatic wrist strap must fit snugly (not
tight). A loose strap provides little or no protection.
C A U T I O N
Antistatic precautions are not 100% effective. Handle electronic
circuit boards as little as possible and then only by the edges. Never
touch the components, exposed traces, or pins on connectors and
cables.
Summary of Contents for 5975T LTM GC/MSD
Page 1: ...Agilent Technologies Agilent 5975T LTM GC MSD Troubleshooting and Maintenance Guide...
Page 10: ...10 Troubleshooting and Maintenance Guide...
Page 32: ...32 Troubleshooting and Maintenance Guide 2 Concepts and General Tasks...
Page 72: ...72 Troubleshooting and Maintenance Guide 3 Chromatographic Symptoms...
Page 86: ...86 Troubleshooting and Maintenance Guide 5 ALS Symptoms...
Page 98: ...98 Troubleshooting and Maintenance Guide 7 Instrument Power On and Communication Symptoms...
Page 108: ...108 Troubleshooting and Maintenance Guide 9 Troubleshooting Tasks...
Page 166: ...166 Troubleshooting and Maintenance Guide 10 General Maintenance...
Page 214: ...214 Troubleshooting and Maintenance Guide 13 Analyzer...