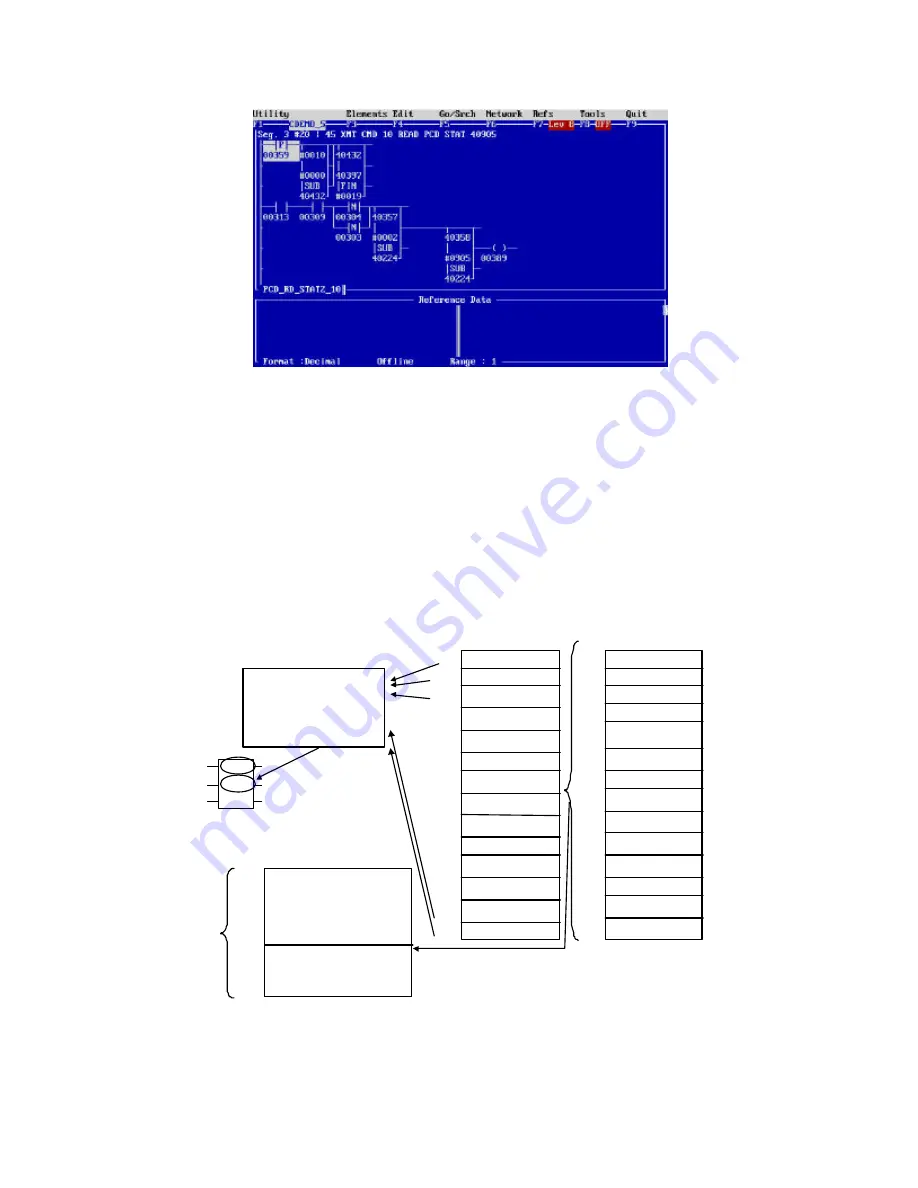
LINE SECTIONALIZING USING A PLC AND ABB PROTECTIVE RELAY
Page 27 of 53
Figure 49. Segment 3 Network 20 – Read PCD Status Information or FIFO Instruction
Load
Segment 3 Networks 21 through 30
As the previous networks 11 through 20 only data access instructions were programmed in the device.
Networks 21 through 30 perform control instructions. As illustrated in the DPU2000R Automation Manual
and the PCD2000 Modbus Protocol documents, the procedure for performing control is to write a group of
registers parameterizing the control (usually writing 5 consecutive registers) and then writing one single
register with the execute command (usually 1) and send it to the relay within 100 seconds of the
parameterization commands. As illustrated in Figures 51 through 60, the procedure to do this is shown in
Figure 50.
6XXX File 1
6XXX File 2
600700
600710
600720
600730
600740
600750
600760
600770
600780
600790
600800
600810
600820
600830
READ DPU STATUS
Parameterize the
XMIT Block
Regs 40308 to
40 315
Data to Parameterize
the Modbus Instructions
at 40355 to 40384 and
also to store write data
parameters for control
611000
611030
611090
611120
611150
611180
611210
611240
611270
611300
611330
611360
611390
611420
Write 1DPU Reg 40360 to PLC41154
Write 5 DPU Regs 40360 to PLC41155
Write5 DPU Regs 40360 to PLC 41155
Write 5 DPU Regs 40360 to PLC 41155
Write 5 DPU Regs 40360 to PLC 1155
Write 5 DPU Reg 40360 to PLC41155
Write 5 PCD Regs 40360 to PLC41155
Write5 PCD Regs 40360 to PLC 41155
Write 5 PCD Regs 40360 to PLC 41155
Write 5 PCD Regs 40360 to PLC 41155
Write 5 PCD Regs 40360 to PLC 41155
Write 1 PCD Regs 40360 to PLC 41154
40300
XMIT
16
#0001
40308 = Coommand Word
40309 =Message Pointer (355)
40310 = Buffer Length (5 Fixed by Modbus)
40311 =Response Timeout ( mS)
40312=Retry Limit
40313 =Start of TransmitDelay
40314 =End of Transmit Delay
40315 =Current Retry Count
CYCLIC
POLL
(40330
counter)
40309 = TRANSER COMMAND TO 40355
40310 = 5 Registers
40355 = Modbus Function Code
40356 = Quantity of Register Read/Written
40357 = DPU or PCD Address
40358 = DPU/PCD Data Address to Read or Write
40359 = 0X or 4X data address in PLC
to placeDPU/PCD data read
or address to obtain data to write to DPU/PCD
40360= Data Area to Store for WRITE instructions
40384=
Data Constant for write 0001 h
PCD WRITE TRIGGER
Data for Write 5 ConstanstsDPU
TRIP
Data for Write 5 Constants
DPU Close
Data for Write 5 Constants
DPU Reset Targets
Data for Write 5 Constants
DPU RESET ALARMS
Data For Write 5 Constants
DPU RESET LATCHED DATA
Data for Write 5 Constants
PCD TRIPS
Data For Write 5 Constants
PCD CLOSE
Data For Write 5 Constants
PCD RESET TARGETS
Data For Write 5 Constants
PCD RESET ALARMS
Data For Write 5 Constants
PCD RESET LATCHED DATA
Data For Write 1 Constant
PCD WRITE TRIGGER
PTR 20
PTR 21
PTR 22
PTR 23
PTR 24
PTR 25
PTR 26
PTR 27
PTR 28
PTR 29
PTR 30
PTR 31
PTR 33
PTR 34
COUNTER
30
Registers
Figure 50. Write Ladder Logic Methodology
Summary of Contents for REL 356
Page 23: ...ABB REL 356 Current Differential Protection 1 10 Product Overview and Specifications ...
Page 83: ...ABB REL 356 Current Differential Protection 3 36 Settings and Application ...
Page 127: ...ABB REL 356 Current Differential Protection 5 28 Testing ...
Page 186: ...LINE SECTIONALIZING USING A PLC AND ABB PROTECTIVE RELAY Page 49 of 53 ...
Page 187: ...LINE SECTIONALIZING USING A PLC AND ABB PROTECTIVE RELAY Page 50 of 53 ...
Page 188: ...LINE SECTIONALIZING USING A PLC AND ABB PROTECTIVE RELAY Page 51 of 53 ...
Page 189: ...LINE SECTIONALIZING USING A PLC AND ABB PROTECTIVE RELAY Page 52 of 53 ...