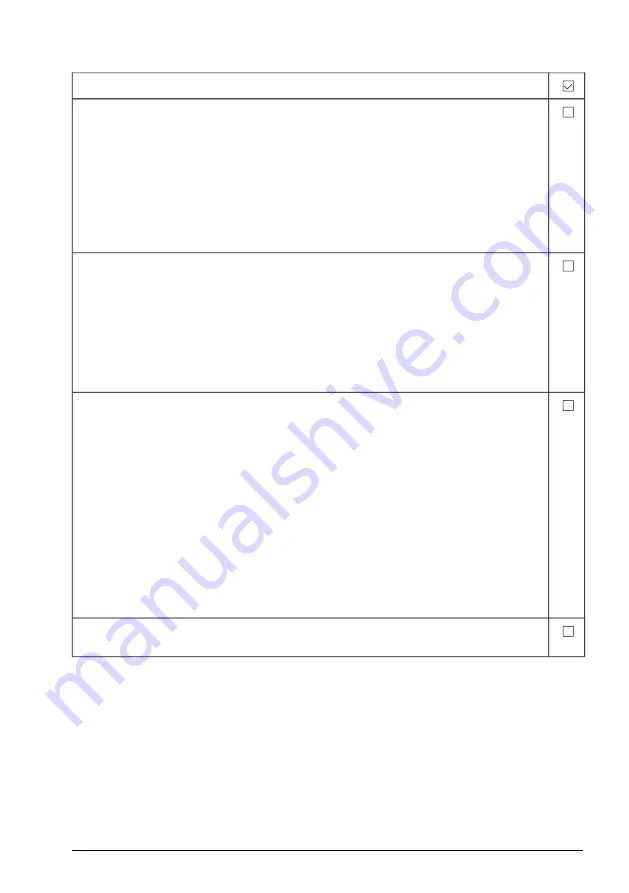
Action
Test the operation of the STO function when the motor is stopped.
• Give a stop command for the drive (if running) and wait until the motor shaft is at a
standstill.
Make sure that the drive operates as follows:
• Open the STO circuit. The drive generates an indication if one is defined for the 'stopped'
state in parameter
31.22
(see the firmware manual).
• Give a start command to verify that the STO function blocks the drive's operation. The
drive generates a warning. The motor should not start.
• Close the STO circuit.
• Reset any active faults. Restart the drive and check that the motor runs normally.
Test the operation of the STO function when the motor is running.
• Start the drive and make sure the motor is running.
• Open the STO circuit. The motor should stop. The drive generates an indication if one
is defined for the 'running' state in parameter
31.22
(see the firmware manual).
• Reset any active faults and try to start the drive.
• Make sure that the motor stays at a standstill and the drive operates as described above
in testing the operation when the motor is stopped.
• Close the STO circuit.
• Reset any active faults. Restart the drive and check that the motor runs normally.
Test the operation of the failure detection of the drive. The motor can be stopped or running.
• Open the 1st channel of the STO circuit. If the motor was running, it should coast to a
stop. The drive generates a
FA81 Safe Torque Off 1 loss
fault indication (see the firm-
ware manual).
• Give a start command to verify that the STO function blocks the drive's operation. The
motor should not start.
• Close the STO circuit.
• Reset any active faults. Restart the drive and check that the motor runs normally.
• Open the 2nd channel of the STO circuit. If the motor was running, it should coast to a
stop. The drive generates a
FA82 Safe Torque Off 2 loss
fault indication (see the firm-
ware manual).
• Give a start command to verify that the STO function blocks the drive's operation. The
motor should not start.
• Close the STO circuit.
• Reset any active faults. Restart the drive and check that the motor runs normally.
Document and sign the validation test report which verifies that the safety function is safe
and accepted for operation.
The Safe torque off function 217
Summary of Contents for ACS880-11
Page 1: ... ABB INDUSTRIAL DRIVES ACS880 11 drives Hardware manual ...
Page 2: ......
Page 4: ......
Page 26: ...26 ...
Page 52: ...52 ...
Page 82: ...82 ...
Page 95: ...R6 R8 IP21 R6 R8 IP55 Electrical installation IEC 95 ...
Page 103: ...R6 1 5 N m 0 5 N m Electrical installation IEC 103 ...
Page 104: ...R8 1 5 N m 0 5 0 6 N m 104 Electrical installation IEC ...
Page 116: ...R6 R8 UL Type 1 R6 R8 UL Type 12 116 Electrical installation North America NEC ...
Page 142: ...142 ...
Page 154: ... Fan arrow must point up 154 Maintenance ...
Page 160: ...160 ...
Page 181: ... Package dimensions R6 R3 R8 Technical data 181 ...
Page 202: ...R3 IP21 UL Type 1 3AXD50000045323 202 Dimension drawings ...
Page 203: ...R3 Option B056 IP55 UL Type 12 3AXD50000045322 Dimension drawings 203 ...
Page 204: ...R6 IP21 UL Type 1 3AXD50000045353 204 Dimension drawings ...
Page 205: ...R6 Option B056 IP55 UL Type 12 3AXD50000045352 Dimension drawings 205 ...
Page 206: ...R8 IP21 UL Type 1 3AXD50000047667 206 Dimension drawings ...
Page 207: ...R8 Option B056 IP55 UL Type 12 3AXD50000047667 Dimension drawings 207 ...
Page 208: ...208 ...
Page 225: ... Declarations of conformity The Safe torque off function 225 ...