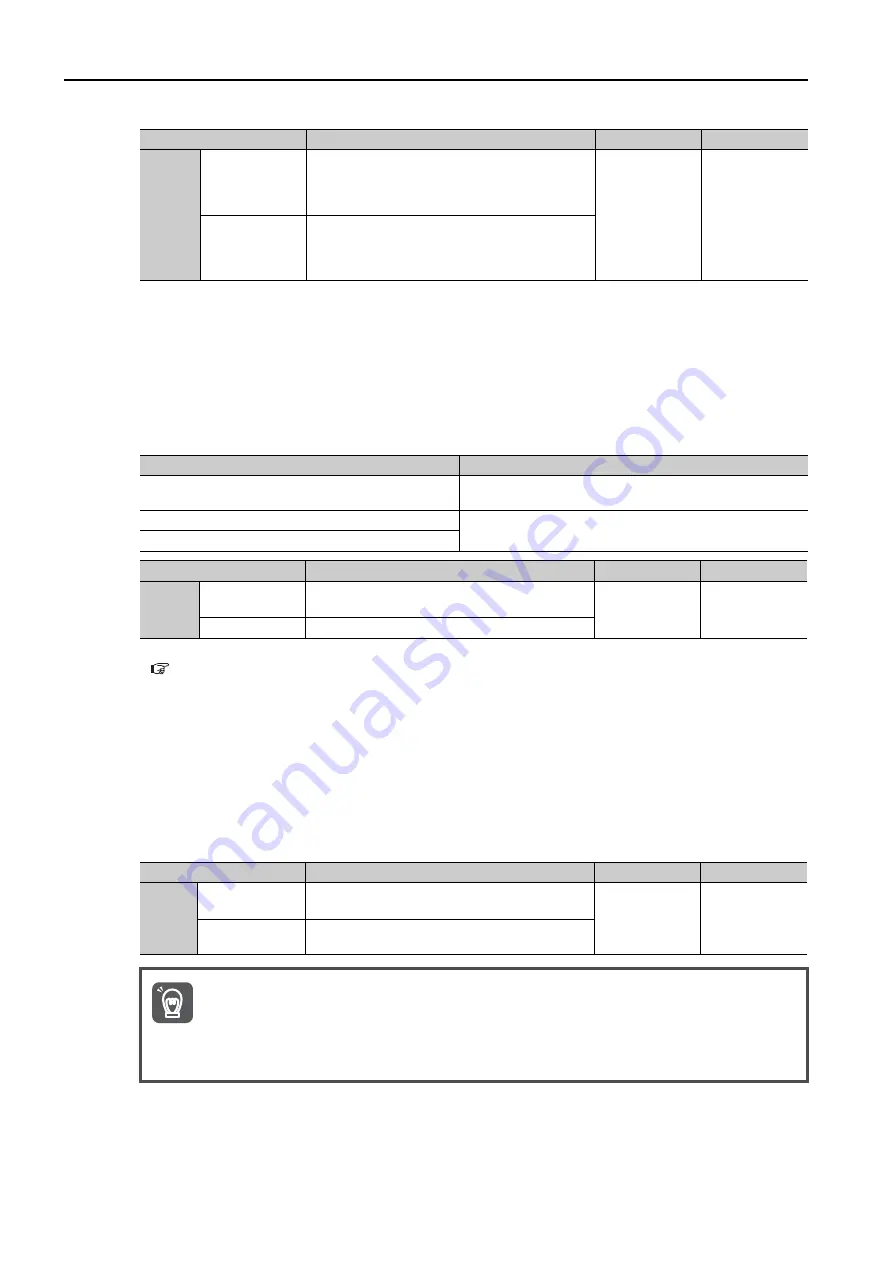
9.6 Autotuning without Host Reference
9.6.6 Automatically Adjusted Function Settings
9-32
Friction Compensation
Friction compensation compensates for changes in the following conditions.
•
Changes in the viscous resistance of the lubricant, such as grease, on the sliding parts of the
machine
•
Changes in the friction resistance resulting from variations in the machine assembly
•
Changes in the friction resistance due to aging
The conditions for applying friction compensation depend on the mode selection.
*
Refer to the following section for details.
Feedforward
If Pn140 is set to n.0
(Do not use model following control and speed/torque feedforward
together (default setting)) and tuning is performed with the mode selection set to 2 or 3, feed-
forward (Pn109), the speed feedforward input (VFF), and the torque feedforward input (TFF) will
be disabled.
To use the speed feedforward input (VFF), the torque feedforward input (TFF), and model fol-
lowing control from the host controller in the system, set Pn140 to n.1
(Use model follow-
ing control and speed/torque feedforward together).
Parameter
Function
When Enabled
Classification
Pn140
(2140h)
n.
0
Do not adjust vibration suppression automati-
cally during execution of autotuning without a
host reference, autotuning with a host refer-
ence, and custom tuning.
Immediately
Tuning
n.
1
(default setting)
Adjust vibration suppression automatically
during execution of autotuning without a host
reference, autotuning with a host reference,
and custom tuning.
Mode Selection Settings
Friction Compensation
1: Standard
Based on the setting of Pn408 = n.X
(Friction Compensation Function Selection)
*
2: For position control
Adjusted with friction compensation.
3: For position control (emphasis on overshooting)
Parameter
Function
When Enabled
Classification
Pn408
(2408h)
n. 0
(default setting)
Disable friction compensation.
Immediately
Setup
n. 1
Enable friction compensation.
Parameter
Function
When Enabled
Classification
Pn140
(2140h)
n.0
(default setting)
Do not use model following control and
speed/torque feedforward together.
Immediately
Tuning
n.1
Use model following control and speed/torque
feedforward together.
When model following control is used with the feedforward function, it is used to make optimum
feedforward settings in the SERVOPACK. Therefore, model following control is not normally used
together with either the speed feedforward input (VFF) or torque feedforward input (TFF) from the
host controller. However, model following control can be used with the speed feedforward input
(VFF) or torque feedforward input (TFF) if required. An unsuitable feedforward input may result in
overshooting.
Important