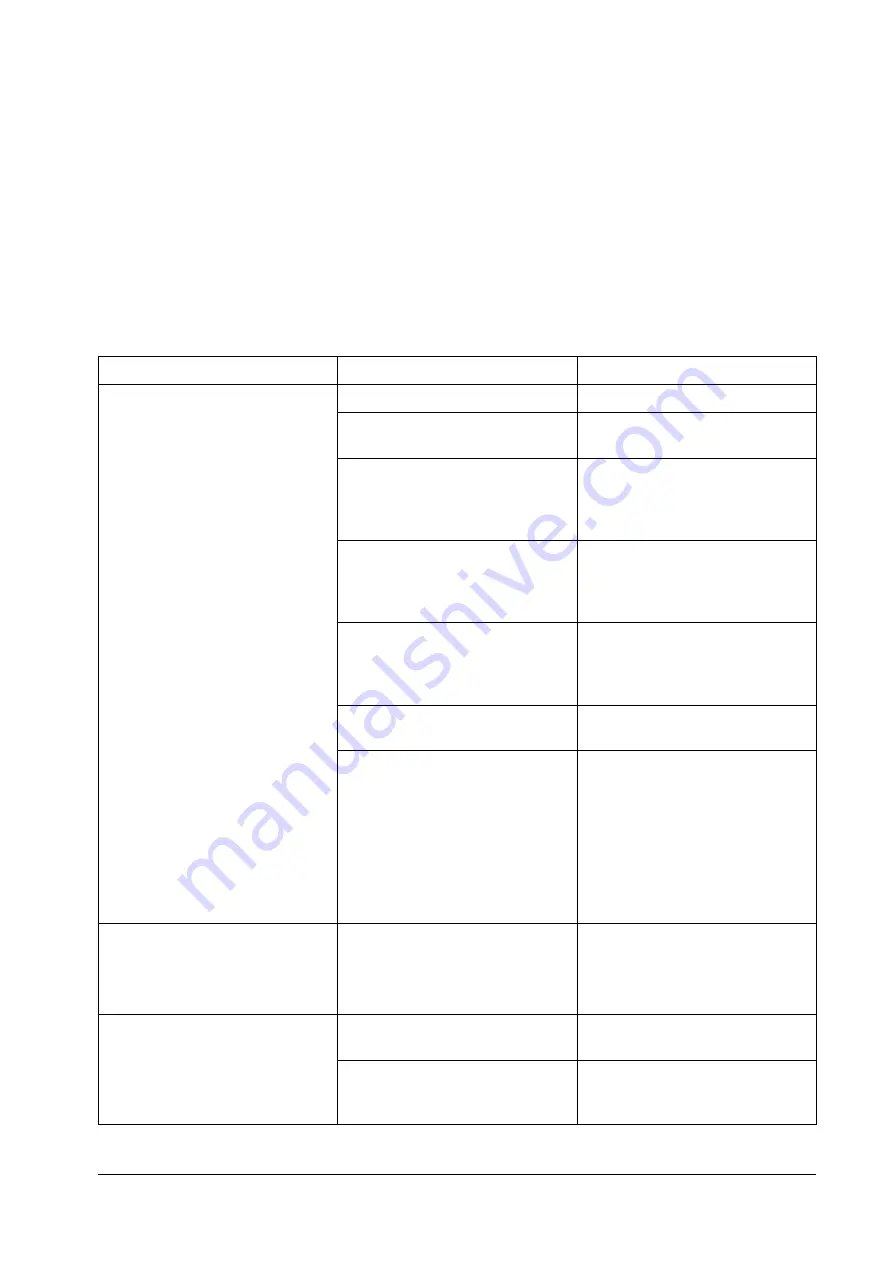
73
XYZ Machine Tools Ltd
TRAK
2
OP
Installation, Maintenance, Service & Part List Manual
218 - ATC ERROR - The ATC timed-out moving to the back location
.
Check that that air
pressure is available and the ATC limit switches are functioning properly.
- The ATC started to
move but didn't make it back in 2 seconds. Use Service Coe 521 to time the ATC. Also make sure the ATC
doesn't bounce off the back limit switch when actuated. The light should stay on and not blink when the
ATC gets to the back location.
219 - SPINDLE ERROR - The spindle was commanded to turn on but the tool clamp is not in the
clamped position. Check the tool clamp limit switches.
- Check that the tool clamp limit switch is
functioning correctly. Check the LED on the back of the control. Use Service Code 521 to confirm the proper
inputs.
5.8.9
Diagnostics Table
The following is a list of symptoms for the ATC and possible causes and remedies.
Symptom
Possible Cause
Remedy
ATC will not move to the front or
back positions
The door is open
Close the door.
Compressed air is not being
supplied to the machine.
Supply 90 psi air to the machine
Low air pressure, dirty air filter
Find the cause of the low air
pressure. Pressure should be 90
psi at the machines regulator,
clean or replace filter.
The solenoid is not receiving an
electrical signal.
Check the LED light on the
computer module to see if the
output has been triggered to
move ATC move out or in.
The tube supplying air to
advance the sliding mechanism
toward the spindle became
pinched or obstructed.
Replace and re-route pinched
tubing.
A mechanical obstruction is
preventing movement.
Remove the obstruction
The ATC door lift assist cylinder
is jammed, or its flow controls
are closed too much and do not
allow sufficient amount of air
flow to lift the door up and assist
the ATC cylinder. This causes too
much resistance for the ATC
cylinder and will prevent the ATC
cylinder from moving forward.
Adjust the ATC door assist lift
cylinder flow controls as specified
in section 5.9.
The tool holder “pops” when
being removed from the spindle
Tool holder or the spindle bore
taper is contaminated with dry
coolant causing it to be tacky
Clean all mating surfaces
Do not leave tool in the spindle
for long periods of time or
overnight.
Tool holder falls from the spindle
during a tool change
An incorrect pull stud is being
used.
Use the proper pull stud.
The pull fingers inside the spindle
are damaged, jammed open or
missing
Visually inspect the pull fingers.
Содержание TRAK 2OP M11 Mill
Страница 9: ...5 XYZ Machine Tools Ltd TRAK 2OP Installation Maintenance Service Part List Manual...
Страница 10: ...6 XYZ Machine Tools Ltd TRAK 2OP Installation Maintenance Service Part List Manual...
Страница 11: ...7 XYZ Machine Tools Ltd TRAK 2OP Installation Maintenance Service Part List Manual...
Страница 12: ...8 XYZ Machine Tools Ltd TRAK 2OP Installation Maintenance Service Part List Manual...
Страница 13: ...9 XYZ Machine Tools Ltd TRAK 2OP Installation Maintenance Service Part List Manual...
Страница 130: ...1 14 15 1 8 15 12 15 14...