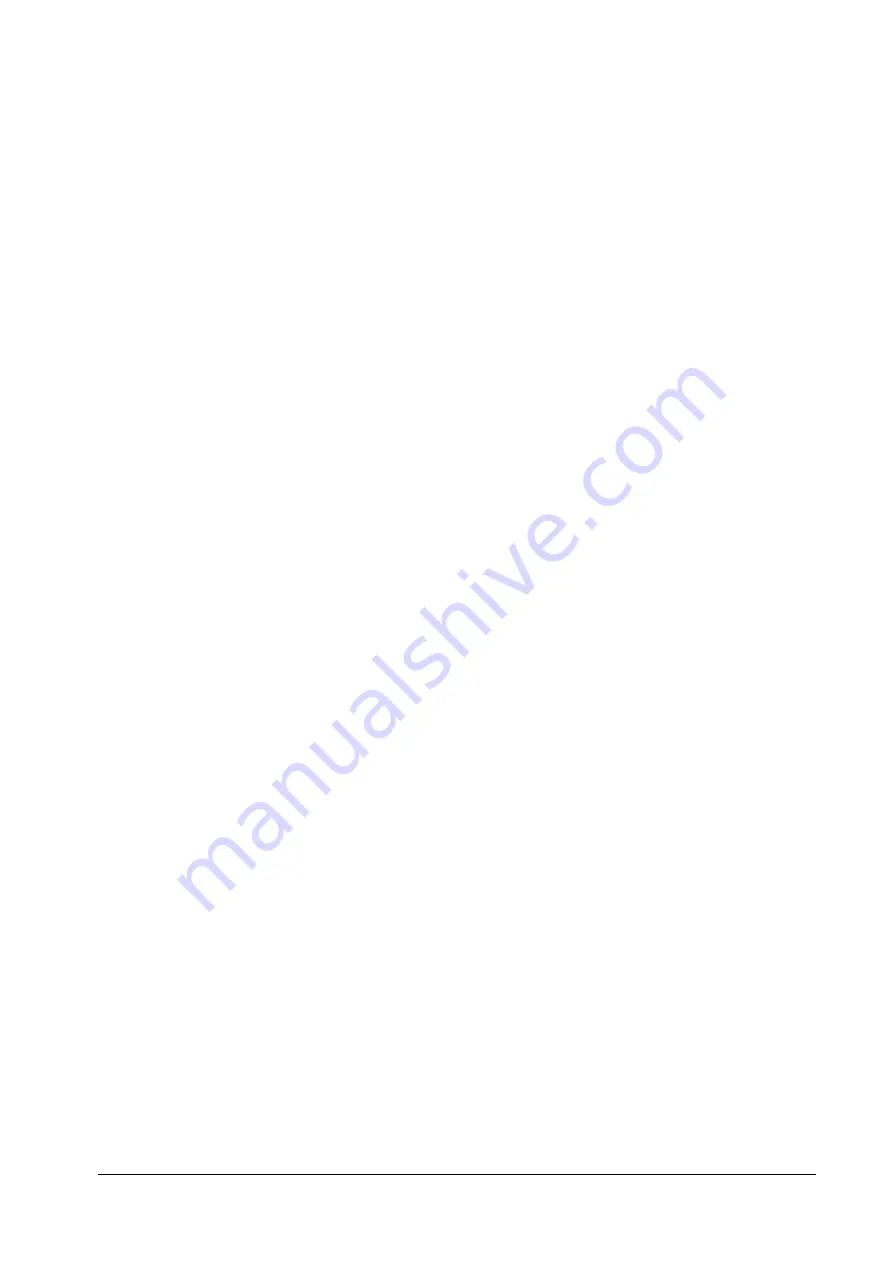
71
XYZ Machine Tools Ltd
TRAK
2
OP
Installation, Maintenance, Service & Part List Manual
During this procedure you will hear the hissing sound of the air blast through the spindle. This sound is a
valuable aid to correct tool height setting. As you near the proper tool change height, you will hear the
sound of the air slowly being blocked off, simply creep down at .002” jog feed rate until the sound of the air
hissing just disappears, then back it off one click and a slight sound of air will once again be heard. That is
the proper tool change height.
It should be noted, that the tool clamping mechanism will give the 30 taper tool holder a slight bump of
~0.020” during the “Unclamp” cycle, to help dislodge the tool holder from the spindle. Likewise, it will give
the tool holder a slight tug at the “Clamp” cycle. This action is both normal and proper.
Any improper setting of the tool change height will result in unnecessary stresses on the gripper assemblies
and the tool magazine.
5.8.4
Tool Clamping Mechanism
There are two forces that are used in the tool clamping mechanism. The first being the force applied by a
stack of Belleville spring washers that are set to apply ~500kg of pull force on the pull stud; clamping the
tool holder into the spindle. The second, is the force of the air/oil cylinder that compresses the Belleville
washers and releases the tool holder from the spindle. See section 6.15 for how to bleed this hydraulic
system if air gets into it.
The spindle pull force is set at the factory and should not be modified for any reason. Modifying this setting
will change the effectiveness of the tool clamping mechanism, and/or shorten its life expectancy.
5.8.5
Tool Carrier Front and Back Cylinder Switches
An air cylinder is used to move the ATC forwards and backwards. There are two sensors mounted on the
cylinder, one near each end. Each sensor has an LED light which illuminates to indicate when the air
cylinder has reached the fully retracted or extended position. When the ATC is back, the rear LED light
should be on. When the ATC moves all the way forward, the front LED comes on for a brief second and
then turns off, as soon as the ATC is pushed back by the worktable to the proper Y location.
Sensor inputs on the computer module are “ATC FRONT” and ATC BACK”.
5.8.6
Clamp and Unclamp Switches
There 2 switches to monitor the status of the tool clamping mechanism “TOOL CLAMP” and TOOL
UNCLAMP”.
“Unclamp” is a limit switch that turns ON when the tool clamp mechanism is in the unclamped state. If this
limit switch is not set or functioning improperly, there is the potential that the drawbar gripper or the
mechanism may become damaged. This switch is triggered only when the machine or the operator is
loading a tool in and out of the spindle. Pressing the green push button on the head puts the machine in
the unclamped state.
Tool “Clamp” is a limit switch that turns ON when the tool clamp mechanism is in the clamped state.
5.8.7
ATC Flow Control Valves
The speed at which the ATC moves front or back is controlled by 2 flow control valves, identified on
drawings 27563-2 and 27540-1 found in this manual. See section 5.9 for more information on these flow
control valves and guidelines on how to adjust them.
One flow control valve controls the speed at which the ATC travels out toward the operator and other how
fast it travels back to its retracted position. In both cases, a clockwise adjustment reduces the speed of the
ATC sliding assembly and an adjustment in the anti-clockwise direction; increases the speed
5.8.8
Error Messages Relating to the ATC
The following is the list of ATC related error messages:
Error 105 - Check the Spindle Drive Module and related electronics. Repair as needed.
The
spindle drive may have faulted. This would happen due to an orientation issue or when the spindle is
decelerating prior to a tool change.
Содержание TRAK 2OP M11 Mill
Страница 9: ...5 XYZ Machine Tools Ltd TRAK 2OP Installation Maintenance Service Part List Manual...
Страница 10: ...6 XYZ Machine Tools Ltd TRAK 2OP Installation Maintenance Service Part List Manual...
Страница 11: ...7 XYZ Machine Tools Ltd TRAK 2OP Installation Maintenance Service Part List Manual...
Страница 12: ...8 XYZ Machine Tools Ltd TRAK 2OP Installation Maintenance Service Part List Manual...
Страница 13: ...9 XYZ Machine Tools Ltd TRAK 2OP Installation Maintenance Service Part List Manual...
Страница 130: ...1 14 15 1 8 15 12 15 14...