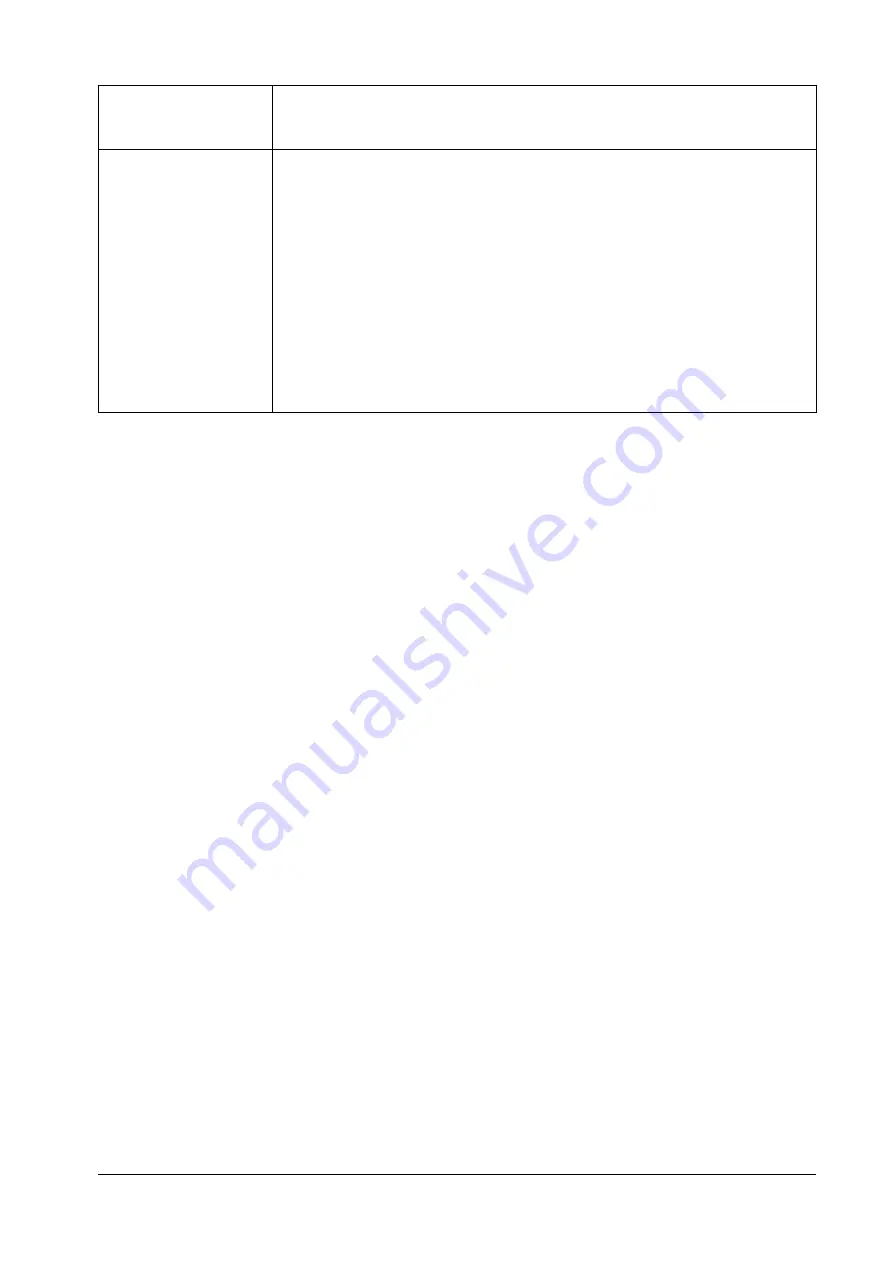
65
XYZ Machine Tools Ltd
TRAK
2
OP
Installation, Maintenance, Service & Part List Manual
Spindle faults out when
decelerating from high
speed.
2.
Verify that the spindle braking resistor is connected properly to the
Inverter.
3.
Verify that the braking resistance is equal to 200 ohms at the Inverter.
Spindle will not turn
when a command is
given.
1.
Verify that the Inverter has power.
2.
Verify that the Forward command is given to the Inverter, by measuring 0
volts DC across the FWD terminal and the DCM terminal on the Inverter
when the FWD command is given and 24 VDC when it is not.
3.
Verify that an RPM command greater than 100 rpm is entered on the
spindle speed command.
4.
Verify that the voltage across terminal AVI and ACM is greater than 0
VDC.
5.
Verify the door closed signal is present on MI5 (0V between DCM and
MI5).
6.
Verify that all parameters on the Inverter are set correctly.
7.
Verify that the E-stop command to Inverter has not been activated. By
measuring 0V from MI1 to DCM. When the E-stop message is present it
will measure 24V (button is pressed).
5.6.2
Spindle Inverter (AC Drive)
The spindle AC Drive is a 2.2kW, 3phase 440 VAC input drive. The AC drive is able to drive the spindle
motor up to 6000 RPM (200 HZ drive frequency). The AC drive contains an encoder input PCB in order to
perform the spindle orientation. The encoder input is also forwarded to the computer module. Without the
encoder input to the drive the AC drive will fault out. When the E-stop is pressed, the AC drive will
automatically decelerate to a stop.
A braking resistor, fitted to the top of the servo cabinet, is connected to the AC drive to reduce spindle
braking times. The resistor is 200 ohms, 500 watts. If the spindle is not braking properly, check the
resistance with an ohmmeter.
There are 5 digital inputs to the AC drive (all 24VDC) and 2 output signals to the computer module. Inputs
and outputs are referred to terminal DCM.
Inputs
1.
FWD (FWD terminal) input:
Commands the AC drive to rotate the spindle in the forward
direction; CW when viewing the motor from the top. The command is activated when the voltage
between the DCM and the FWD terminals is 0 volts and deactivated when it is 24 volts DC.
2.
REV (REV terminal) input:
Commands the AC drive to rotate the spindle in the reverse
direction; CCW when viewing the motor from the top. The command is activated when the voltage
between the DCM and the REV terminals is 0 volts and deactivated when it is 24 volts DC. Please note
that the user can only run the spindle in the forward direction by pressing the ON button on the
overlay. Reverse is used when the ProtoTrak is controlling the spindle during tapping.
3.
Orientate (MI3 terminal) input:
Commands the AC drive to go a specific angle, specified by
parameter 10-19. Note in order for the AC drive to accept an orientation command a FWD and
Orientation command must be given at the same time. The command is activated when the voltage
between the DCM and the MI3 terminals is 0 volts and deactivated when it is 24VDC.
4.
Reset (MI2 terminal) input:
Resets the AC Drive after a fault condition has occurred. The
command is activated when the voltage between the DCM and the RESET terminals is 0 volts and
deactivated when it is 24VDC.
5.
E-stop (MI1 terminal) input:
Informs the drive that an E-stop condition has been activated and
to disable the spindle drive immediately. The E-stop command takes precedence over any other
command. The command is activated when the voltage between the DCM and the MI1 terminals is 24
volts and deactivated when it is 0 volts DC. When the E stop button is pressed and the message is on
the screen you should see 24 volts.
6.
Door Interlock (MI5 terminal):
Inhibits the drive when the door is open via door relay, K2
(24VDC measured between MI5 and DCM). If the door switch is working, but K2 fails open, then the
Содержание TRAK 2OP M11 Mill
Страница 9: ...5 XYZ Machine Tools Ltd TRAK 2OP Installation Maintenance Service Part List Manual...
Страница 10: ...6 XYZ Machine Tools Ltd TRAK 2OP Installation Maintenance Service Part List Manual...
Страница 11: ...7 XYZ Machine Tools Ltd TRAK 2OP Installation Maintenance Service Part List Manual...
Страница 12: ...8 XYZ Machine Tools Ltd TRAK 2OP Installation Maintenance Service Part List Manual...
Страница 13: ...9 XYZ Machine Tools Ltd TRAK 2OP Installation Maintenance Service Part List Manual...
Страница 130: ...1 14 15 1 8 15 12 15 14...