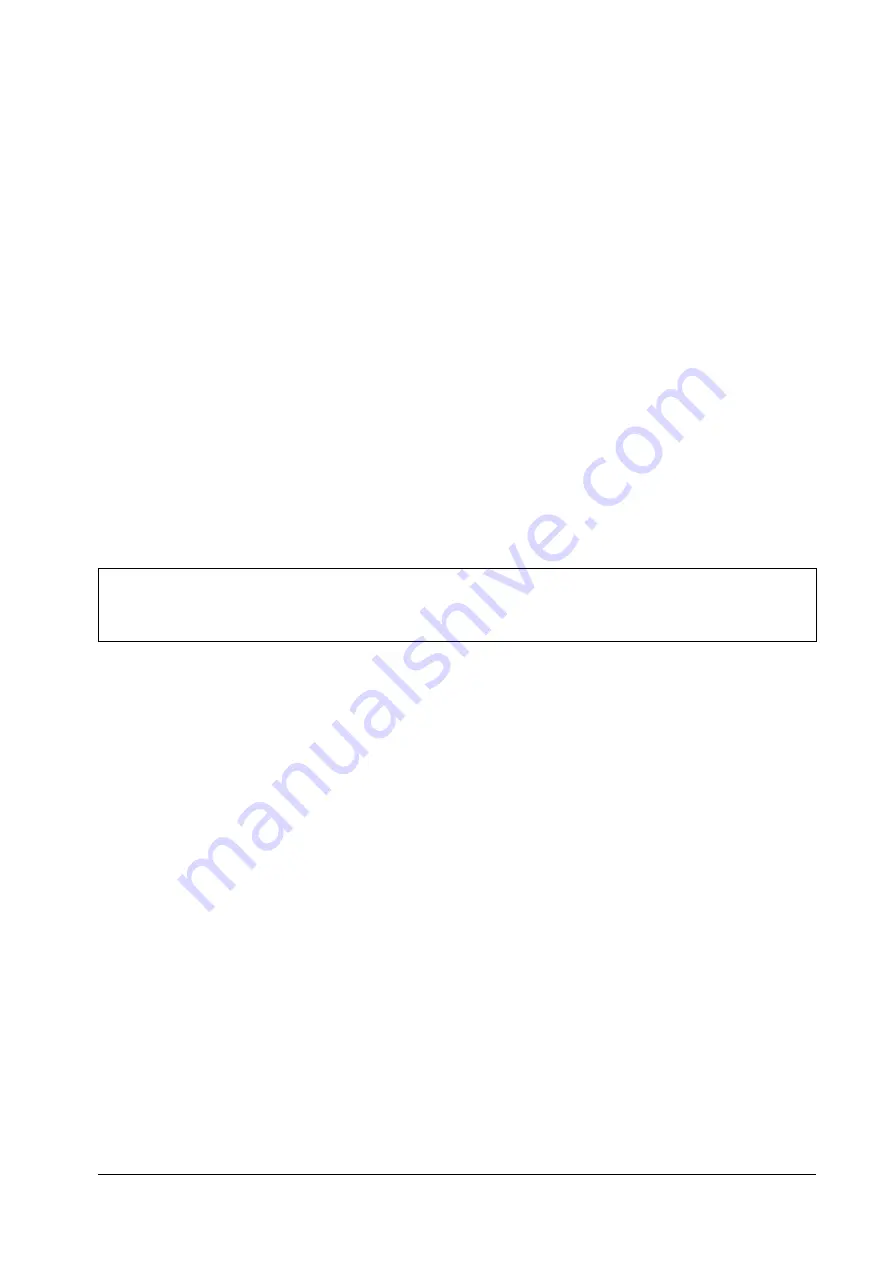
105
XYZ Machine Tools Ltd
TRAK
2
OP
Installation, Maintenance, Service & Part List Manual
13.
Torque the five SHCS that secure the ballnut to the yoke to 10Nm (7ft-lbs).
14.
Install the lower bearing locknut and tighten the three locking set screws.
15.
Check Z-Axis torque.: Move the head down and place a support under head. Use the Z axis brake
test in Service Code 521 to release the brake. DANGER – HEAD WILL FALL IF NOT SUPPORTED.
Check torque in upward direction and record. Values should be 3.5Nm (31in-lbs) or less. Ideally
you want to check the torque in 3 places along the length to make sure the ballscrew is aligned.
16.
Install the Z-axis ballscrew cover:
a.
Place the cover against the column and secure with the two SHCS at the centre of the
frame.
b.
Secure the underside of the frame to the lower bearing housing with two BHCS
c.
Secure the top segment of the telescoping cover to the sheet metal bracket at the back of
the bridge.
17.
Make sure the motor index angle is set correctly. Check in service code 505. Adjust motor as
required.
18.
Enter service code 520 to set the tool change height:
a.
Place a tool holder in any pocket. Jog the X and Y axes to the relevant coordinates that are
displayed in the table.
b.
Press the orient spindle tab.
c.
Press the tool unclamp tab.
d.
Using the EHW, highlight the Z Tool Change dialogue box.
e.
Jog the Z-axis towards the tool holder, change to .002” federate as you get close to the
tool holder. As the spindle goes over the tool holder, listen for the air to stop escaping from
around the tool holder, then back up one click. Enter the Z tool change offset that is
displayed in the lower right hand gray box.
6.8
Spindle Motor Replacement
Warning!
The spindle motor weighs approximately 30kgs; use appropriate lifting equipment attached to the two
eye bolts to move the motor!
Please refer to assembly drawing 27500-1 found at the back of this manual.
1.
Remove the right and left side enclosure panels. Remove the following panels from the spindle
head (
E-stop the machine first. if still powered up during this process
):
a.
unclamp button panel,
b.
vented top cover,
c.
front cover
d.
side covers.
2.
Jog the Z-axis downward to the end of travel.
3.
Shut down the 2 Op and
turn off the power
.
4.
Remove the junction box covers from the motor and disconnect the incoming power, spindle
fan and encoder cables.
5.
Remove the clamp/unclamp bracket assembly.
6.
Loosen the 2 clamp screws on the driven side of the coupler.
7.
Remove the four hex head bolts that secure the motor the head.
8.
Hoist the motor upward until the motor is clear of the machine.
9.
Alternatively, using an extended hex socket, manually drive the X-axis to the right hand side of
the bridge, allowing the motor to be lowered to the table.
10.
Place a couple blocks of wood or other suitable support onto the table and lower the motor
down.
11.
Remove the hoisting cable
12.
Manually drive the Y-axis toward the front of machine to ease lifting of the motor from the
machine.
13.
Install the new motor in reverse order.
14.
Tighten the two clamp screws on the motor coupler.
15.
Enter service code 510 to set spindle orientation and follow the on-screen instructions.
Содержание TRAK 2OP M11 Mill
Страница 9: ...5 XYZ Machine Tools Ltd TRAK 2OP Installation Maintenance Service Part List Manual...
Страница 10: ...6 XYZ Machine Tools Ltd TRAK 2OP Installation Maintenance Service Part List Manual...
Страница 11: ...7 XYZ Machine Tools Ltd TRAK 2OP Installation Maintenance Service Part List Manual...
Страница 12: ...8 XYZ Machine Tools Ltd TRAK 2OP Installation Maintenance Service Part List Manual...
Страница 13: ...9 XYZ Machine Tools Ltd TRAK 2OP Installation Maintenance Service Part List Manual...
Страница 130: ...1 14 15 1 8 15 12 15 14...