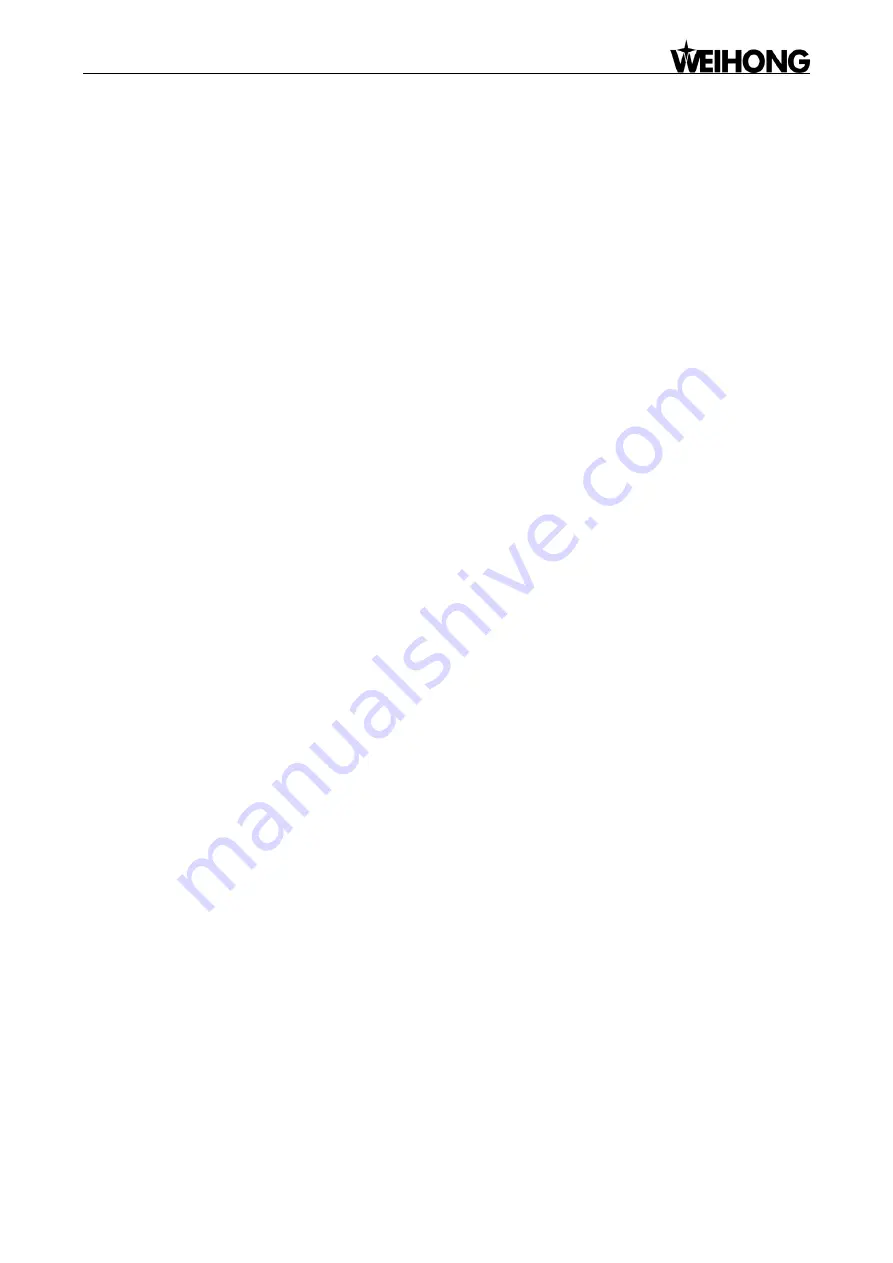
Specialized Concentrated Focused
Maintenance
「
93
」
4.3.4 What should you do if machine tool returns to machine
origin abnormally?
Limit alarm or servo driver alarm occurs during backing to machine origin.
1) Check if the software can receive the origin signal of this axis. The method is: trigger the origin
switch, and then see if the color of the dot before the “× machine origin” changes from red to green
in [Diagnosis] function section. If there is no color change, it indicates the
software can‟t receive the
origin signal, needing to check if there is an error in the origin switch or in the wiring of origin switch.
To see if the system failure occurs, make the origin signal on the terminal board and COM port into
conduction directly with a conducting wire
, and then check whether the color of the dot before “×
machine origin” changes in [Diagnosis] function section.
2) Check whether the position of origin switch is appropriate to avoid the following three situations: the
distance between origin switch and limit switch is too small; the origin switch is installed behind the
limit switch; or the position of origin switch is out of the mechanical stroke of machine tool.
When backing to machine origin, the machine tool motions towards a certain direction at a relatively
low speed (ninth of the coarse positioning speed) until limit is triggered.
See if the polarity of “× machine origin” input port is correct in [Diagnosis] function section. When this
origin switch is triggered, i.e. there is signal input, the color of the dot should be green. Otherwise, it is
red.
A certain axis moves a very long distance or keeps moving at a rather low speed towards the
reverse direction after coarse positioning during backing to machine origin.
The cause of th
e above phenomenon is that the system can‟t detect the encoder origin signal of this
axis.
1) See if the servo cable of this axis is well contacted at the joints with system host machine and servo
driver.
2)
Set the value of driver parameter “pre-scaler (frequency divider) of encoder” as 1/2 or 1/4 of the
original one if YASKAWA or TECO, etc. driver is used.
3) Check if there is an error in the driver, servo cable, motor cable or the control system (e.g. exchange
servo cable and servo driver with those of other axes able to return to machine origin normally).
4.3.5 What should you do if the machine tool motions upward
after arriving at the position of tool presetter during
presetting?
View and tell whether the polarity of “tool presetting signal” is right in [Diagnosis] screen. The color of the
dot before the “tool presetting” signal is red when the system does not receive tool presetting signal.