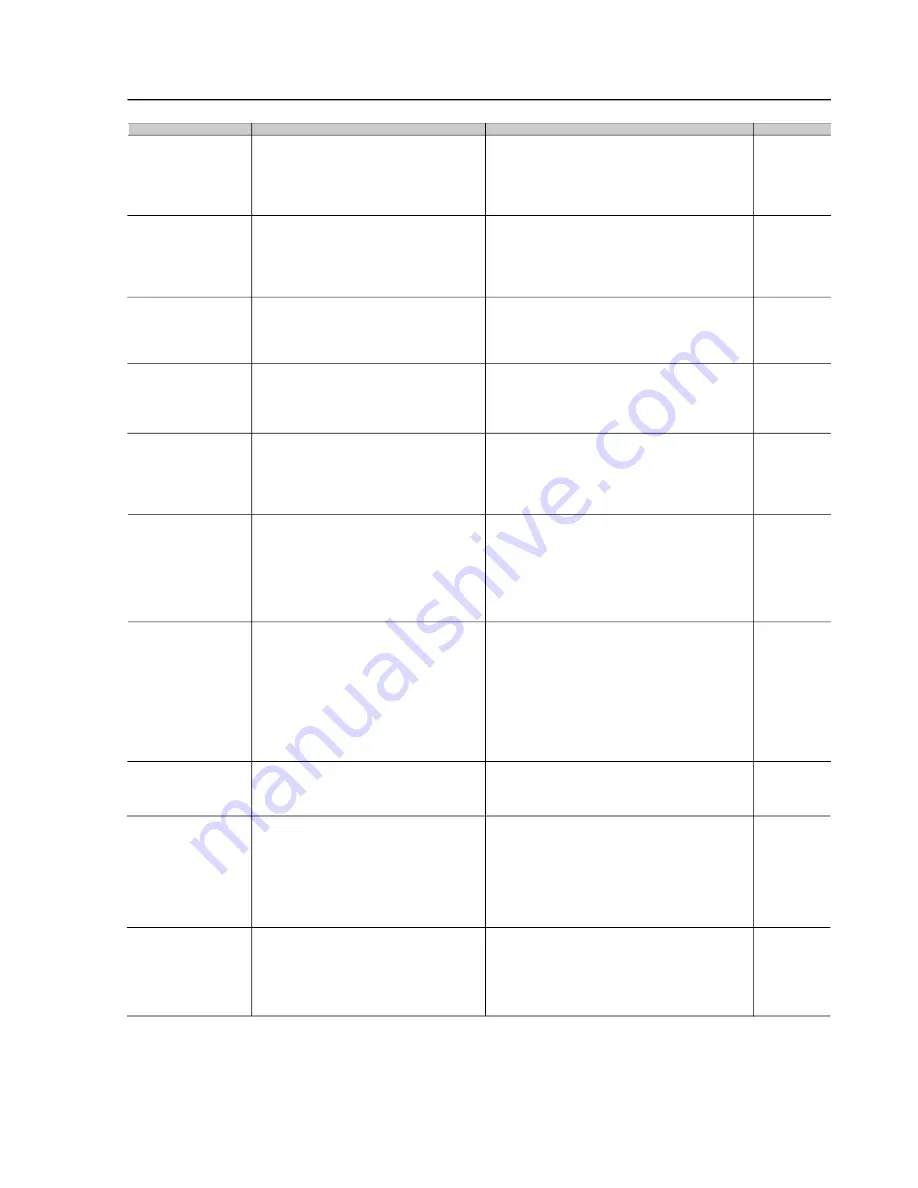
CHAPTER 8 - DIAGNOSTICS AND TROUBLESHOOTING
141
Table 8.1 (Cont.) -
Detailed Fault Description
FAULT
E65
Motor Undercurrent at
full voltage operation
E66
Motor Overcurrent at
full voltage operation
E67
Wrong phase
sequence at start
begin
E70
Undervoltage at the
Electronics supply
E71
Internal By-pass relay
contact is open
E72
Overcurrent before
By-pass closing
E74
Current unbalance
E75
Line frequency out of
range
E76
Undercurrent before
By-pass closing
E77
By-pass relay contact
is closed
DESCRIPTION OF THEACTUATION
When the current is lower than the
programmed during the programmed time.
Motor rated current is used as reference.
When the current is higher than the
programmed during the programmed time.
The rated motor current is used as
reference.
When the signal interruption sequence of
the synchronism do not follows the
R
/1L1,
S
/3L2,
T
/5L3 sequence.
When the supply of the control board power
supply is lower than 93,5Vac.
When any problem with the contacts of the
By-pass relay, internal or external, has been
detected at full voltage after start.
When at the end of the acceleration ramp
the current is not lower than 2x the rated
current of the Soft-Starter (P295x2) before
closing of the internal By-pass relay.
When the current of one of the phases is
lower or higher during the programmed time.
The other motor phases are used as
reference.
When the frequency is lower or higher than
the limits from 42,5 to 69Hz during more than
0.5s.
When at the end of the acceleration ramp
the current is lower than 0,1x the rated
current of the Soft-Starter (P295x0,1)
before closing of the internal By-pass relay.
When the contact of the By-pass relay, internal
or external, will not opened.
POSSIBLE CAUSES
The percent value programmed as maximum
acceptable undercurrent limit (P610) is lower than
required for the motor and its application.
In applications with hydraulic pumps which ay be
operated without load.
The percent value programmed as maximum
acceptable overcurrent limit (P612) is lower than
required for the motor and its application.
Motor with instantaneous overload.
Stalled motor or locked rotor.
Parameter P620 has been programmed without
need. Wrong phase sequence.
This can be changed in another point of the power
supply line.
Phase loss in the control board supply.
Bad contact in the control board supply.
Fuse in control board supply is open,
glass fuse 5x20mm 2A with delayed action.
Bad contact of the internal or extenal By-pass relay
supply.
Bad contact of the internal or extenal By-pass relay
due to any overload. an overload
P140=1 without external By-pass relay connected.
Rated Soft-Starter current has been wrong
programmed at P295.
The time programmed at P102 is shorter than
required for the motor start by voltage ramp.
Motor rated current is higher than allowed for the
Soft-Starter.
Stalled motor or locked rotor.
Value programmed at P614 and P615 is out of
range and not allowed for this application.
Voltage drop in one or more phases of the power
supply.
Phase loss in the power supply.
Input transformers have been undersized.
Input fuses are open.
Bad contact of the power supply connections or
connections to the motor.
When the Soft-S motor are being supplied
by a generator that is unable to drive the motor at
rated load or is unable to start the motor.
Power supply fault or thyristor fault before Bypass
closing.
The rated Soft-Starter current has been wrong
programmed at P295.
Rated motor current is lower than the minima
current (P295x0.3).
For tests you can set P616=0.
Bad contact of the internal or external By-pass relay
due to any overload. an overload.
Short Circuit in the contact of the internal or external
By-pass relay due to any overload. an overload.
Short Circuit in parallel with the contact of By-pass:
thyristor in short circuit, external short circuit.
RESET
Power-on
Manual Reset
Auto-reset
DIx
Power-on
Manual
ResetAuto-
reset
DIx
Power-on
Manual Reset
DIx
Power-on
Manual Reset
DIx
Power-on
Manual Reset
DIx
Power-on
Manual Reset
DIx
Power-on
Manual Reset
Auto-reset
DIx
Power-on
Manual Reset
DIx
Power-on
Manual Reset
DIx
Power-on
Manual Reset
DIx
Phone: 800.894.0412 - Fax: 888.723.4773 - Web: www.clrwtr.com - Email: [email protected]