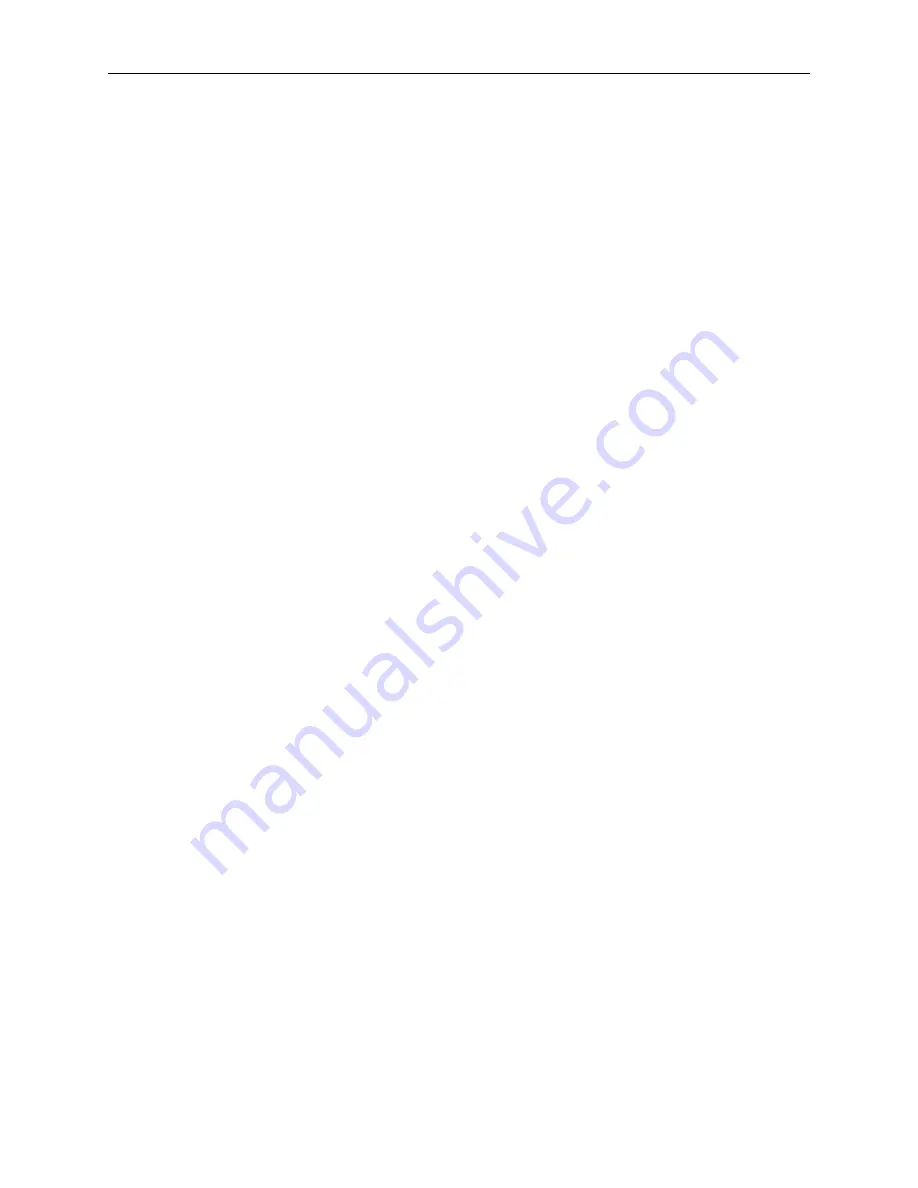
Volume 3, 9/10/04
Appendix A - Page 207
can expect a response time of less than 0.18 seconds; the closed end thermocouple will require a
10 second reaction time in an air stream. In liquids, their response time is less than 4 seconds.
Keep in mind, the trade-off for faster response times is less longevity. The 0.125” open tip probes
will require more frequent replacement if used for exhaust gas temperature measurement.
A 0.25" diameter thermocouple tube is available in a 5" length with an open thermocouple end.
Utilizing 20 gauge wire (0.0285" diameter), it is ideally suited for measuring temperatures of air or
exhaust gases. Its response time to a step change in temperature is approximately 0.3 seconds.
This response time is a function of the thermocouple and not a limitation of software.
A second 0.25" diameter thermocouple tube also has a 5" length and uses a closed end. Also
fitted with 20 gauge wire (0.0285" diameter), the closed end model is specifically designed for
measuring fluid temperatures. The response time for temperature changes in fluid is
approximately 10 seconds. (While this closed end version could be used to measure air
temperatures, the air response time is much greater).
Proper placement of the thermocouples is critical to proper exhaust gas measurement. The
thermocouple must be placed in the high velocity flow area of the exhaust pipe to obtain uniform
readings. As a rule, a protrusion of at least 0.31" (8mm) into the gas stream is a minimum
placement figure. Most of our users report very good results at 0.37" (9mm) protrusion. It is also
important to index the open end of the tip so gases flow evenly across both types of wire and
through the opening.
Thermocouple readings are affected by the radiation of heat from the surrounding pipe. Cast iron
exhaust headers, for example, run hotter on the interior surface and radiate heat back to the
thermocouple. As a result, the thermocouple can read up to 150°F (80°C) hotter than with a thin-
walled steel header pipe. Conversely, pipes which are cooled with an air blower will register a
lower temperature reading than uncooled pipes, even though the gas temperature is actually the
same. You will also notice that stainless pipes have a different heat reflection than mild steel.
Because the exhaust gases are only flowing over the thermocouples for about 40% of each engine
cycle, the temperature readings average 150 to 200°F, (80 to 110°C), less than the true average
exhaust gas temperature.
Two final factors which induce fluctuations in thermocouple readings are contamination and
vibration.
Proper maintenance procedures for these thermocouples should include cleaning the plug
contacts periodically. At any time during a test that you encounter erratic thermocouple readings,
your first troubleshooting procedure should include unplugging and plugging the thermocouples to
regain contact which may have been sacrificed by vibration. You can normally spot a loose contact
by lower than normal temperature readings. On the other side of the spectrum, an erratically high
temperature reading is often the result of ignition noise.
If you require specialty thermocouples for other categories of temperature measurements, there
are many thermocouple manufacturers. The only requirement for inclusion into the SuperFlow
dynamometer system is that the thermocouples be type K (other types can be used if the system is
configured for those types with the proper electronic module).
We recommend using ungrounded types, as they induce less radio frequency interference (RFI)
noise into the data acquisition and control system. A grounded thermocouple will respond faster,
but will also introduce ignition noise into the system. Any thermocouple you install should have a
shielded wire cable if it is to be applied to a spark ignition engine. You may also use an Ohm meter
to check if the thermocouple is shorted to ground or open.
Содержание AutoDyn
Страница 4: ...AutoDyn Operators Manual Section 1 Page 4 AutoDyn Cover fm...
Страница 5: ...1 General Information...
Страница 10: ...S Y S T E M O V E R V I E W Section 2 Page 1 2 System Overview...
Страница 24: ...P A C K A G I N G A N D H A N D L I N G Section 3 page 1 Packaging and Handling 3...
Страница 29: ...T E S T A R E A R E Q U I R E M E N T S Section 4 page 1 4 Test Area Requirements...
Страница 40: ...I N S T A L L A T I O N Section 5 Page 1 5 Installation...
Страница 55: ...6 System Operation...
Страница 60: ......
Страница 78: ...H A N D H E L D C O N T R O L L E R Section 7 Page 1 7 Handheld Controller...
Страница 104: ...8 Theory Of Testing...
Страница 114: ...Theory Of Testing Volume 2 9 10 04 Section 8 Page 13 Figure 8 1 Frontal Area Coefficient of Drag US...
Страница 115: ...AutoDyn Operators Manual Section 8 Page 14 Theory Of Testing fm Figure 8 2 Frontal Area Coefficient of Drag Metric...
Страница 123: ...9 Description of the Configuration File...
Страница 172: ...20 Service and Calibration...
Страница 178: ...S E R V I C E A N D C A L I B R A T I O N Section 20 page 7 20 2 Maintenance record...
Страница 193: ...A General Testing Information Appendix...
Страница 205: ...B Fundamental Concepts to Obtaining Superior Repeatability Appendix...