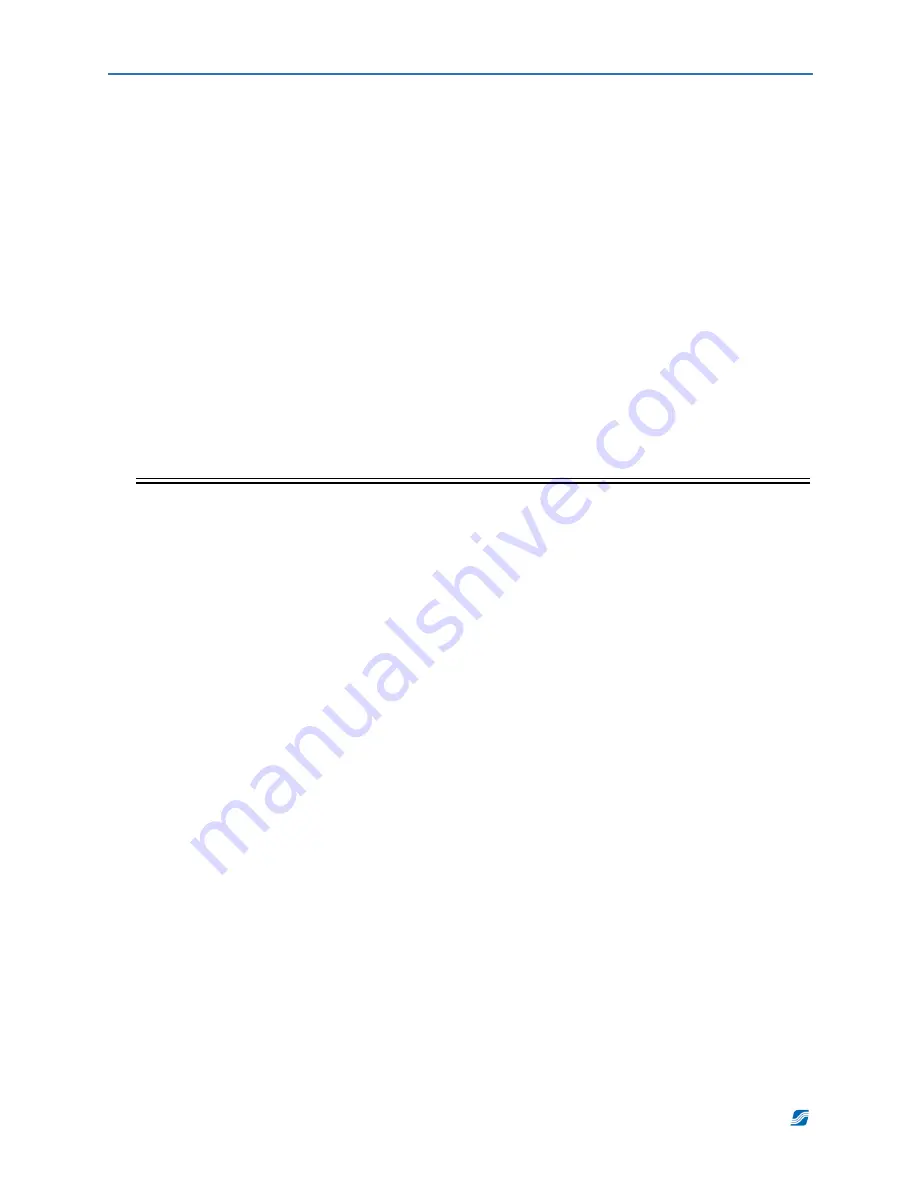
Adjusting Control Mode Parameters
SuperFlow Technologies Group 11-15
11.5.11 Delay
Allowed Values:
Any integer value
Suggested Value Range:
Usually set to zero
What it Does
This term applies a delay to the controller output signal. It provides a method in which a
delay can be introduced between the control system and the actual output of the control valve.
In essence, this parameter indicates the number of passes (cycles) that will occur through the
control system before the controller output signal will be updated.
Suggested Adjustment Technique
Leave the delay at zero for most applications. If you want to delay controller response to
smooth through sudden changes in the device under control, then increase the delay value
until the control system responds smoothly.
11.6 Adjusting Control Mode Parameters
It is useful to set up two speed set points or two torque set points that the operator may manually
toggle between to observe closed-loop system step response for the purpose of tuning the control
parameters. Determine these set points to prevent the engine from reaching excessive speed and
to ensure the engine throttle remains above idle.
It is helpful to create a strip chart display object on a WinDyn screen to allow real-time
observation of the control system while performing adjustments. WinDyn uses the channels
named SETPT1 and SETPT2 as its control channels. By displaying either of these channels and the
desired control channel on a strip chart at the same time, you can observe control system response
in real time.
It is best to tune by individually adjusting the control parameters in each of the control loop
modes. If you encounter a problem while running dual-mode, closed-loop control, the easiest
approach is to go back and individually tune each of the two single-mode control loops that
would otherwise be operating simultaneously.
For best results, in engine dynamometer applications, SuperFlow recommends using the load
controller to control the engine rpm. The engine controller (throttle) can be used in throttle
position (manual mode) or to control the engine torque (close-loop mode). In chassis
dynamometer applications, SuperFlow recommends using the absorber unit to control the vehicle
speed.
Содержание AutoDyn
Страница 4: ...AutoDyn Operators Manual Section 1 Page 4 AutoDyn Cover fm...
Страница 5: ...1 General Information...
Страница 10: ...S Y S T E M O V E R V I E W Section 2 Page 1 2 System Overview...
Страница 24: ...P A C K A G I N G A N D H A N D L I N G Section 3 page 1 Packaging and Handling 3...
Страница 29: ...T E S T A R E A R E Q U I R E M E N T S Section 4 page 1 4 Test Area Requirements...
Страница 40: ...I N S T A L L A T I O N Section 5 Page 1 5 Installation...
Страница 55: ...6 System Operation...
Страница 60: ......
Страница 78: ...H A N D H E L D C O N T R O L L E R Section 7 Page 1 7 Handheld Controller...
Страница 104: ...8 Theory Of Testing...
Страница 114: ...Theory Of Testing Volume 2 9 10 04 Section 8 Page 13 Figure 8 1 Frontal Area Coefficient of Drag US...
Страница 115: ...AutoDyn Operators Manual Section 8 Page 14 Theory Of Testing fm Figure 8 2 Frontal Area Coefficient of Drag Metric...
Страница 123: ...9 Description of the Configuration File...
Страница 172: ...20 Service and Calibration...
Страница 178: ...S E R V I C E A N D C A L I B R A T I O N Section 20 page 7 20 2 Maintenance record...
Страница 193: ...A General Testing Information Appendix...
Страница 205: ...B Fundamental Concepts to Obtaining Superior Repeatability Appendix...