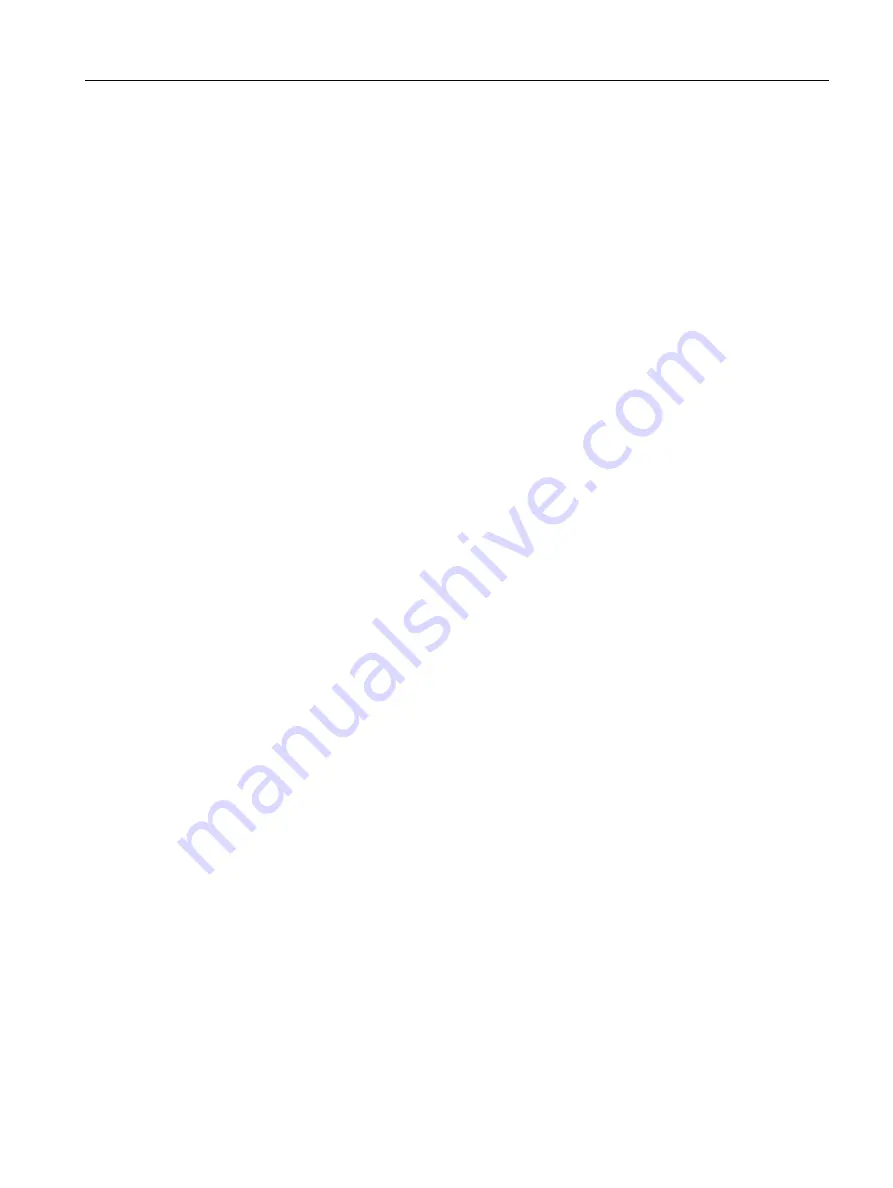
K1: Mode group, channel, program operation, reset response
9.4 Channel
Basic Functions
Function Manual, 09/2011, 6FC5397-0BP40-2BA0
493
Channel configuration
Channels can be filled with their own channel name via the following machine data:
MD20000 $MC_CHAN_NAME (channel name)
The various axes are then assigned to the available channels via machine data. There can be only one
setpointissuing channel at a time for an axis/spindle. The axis/spindle actual value can be read by several
channels at the same time. The axis/spindle must be registered with the relevant channel.
Further, the following channelspecific settings can also be made using machine data:
• Position of deletions or the basic program settings of G groups via the machine data:
MD20150 $MC_GCODE_RESET_VALUES (RESET position of G groups)
• Auxiliary function groups regarding the combination and the output time.
• Transformation conditions between machine axes and geometry axes
• Other settings for the execution of a part program
Change in the channel assignment
An online change in the channel configuration cannot be programmed in a part program or PLC user program.
Changes in the configuration must be made via the machine data. The changes become effective only after a
new POWER ON.
Container axes and link axes
An axis container combines a group of axes in a container. These axes are referred to as container axes. This
involves assigning a pointer to a container slot (ring buffer location within the relevant container) to a channel
axis. One of the axes in the container is located temporarily in this slot.
Each machine axis in the axis container must be assigned at all times to exactly one channel axis.
Link axes can be assigned permanently to one channel or dynamically (by means of an axis container switch) to
several channels of the local NCU or the other NCU. A link axis is a nonlocal axis from the perspective of one of
the channels belonging to the NCU to which the axis is not physically connected.
The assignment between the link axes and a channel is implemented as follows:
• For permanent assignment using machine data:
Allow the direct logic machine axis image to show link axes.
• For dynamic assignment:
Allow the axis container slot machine data to show link axes.
For more information on link axes and container axes, refer to
References:
/FB2/ Function Manual, Extended Functions; Several Operator Panel Fronts and NCUs, Distributed Systems
(B3)
Interface signals
The signals of the 1st channel are located in the NC/PLC interface in DB21, the signals from channel 2 are
located in DB22. The channel or channels can be monitored and controlled from the PLC or NCK.
Содержание SINUMERIK 828D Turning
Страница 34: ...Basic Functions 34 Function Manual 09 2011 6FC5397 0BP40 2BA0 ...
Страница 146: ...A3 Axis Monitoring Protection Zones 2 6 Data lists Basic Functions 146 Function Manual 09 2011 6FC5397 0BP40 2BA0 ...
Страница 328: ...F1 Travel to fixed stop 6 5 Data lists Basic Functions 328 Function Manual 09 2011 6FC5397 0BP40 2BA0 ...
Страница 816: ...K2 Axis Types Coordinate Systems Frames 10 9 Data lists Basic Functions 816 Function Manual 09 2011 6FC5397 0BP40 2BA0 ...
Страница 1198: ...P4 PLC for SINUMERIK 828D 14 6 Function interface Basic Functions 1198 Function Manual 09 2011 6FC5397 0BP40 2BA0 ...
Страница 1752: ...Appendix 20 2 Overview Basic Functions 1752 Function Manual 09 2011 6FC5397 0BP40 2BA0 ...
Страница 1774: ...Glossary Basic Functions 1774 Function Manual 09 2011 6FC5397 0BP40 2BA0 ...