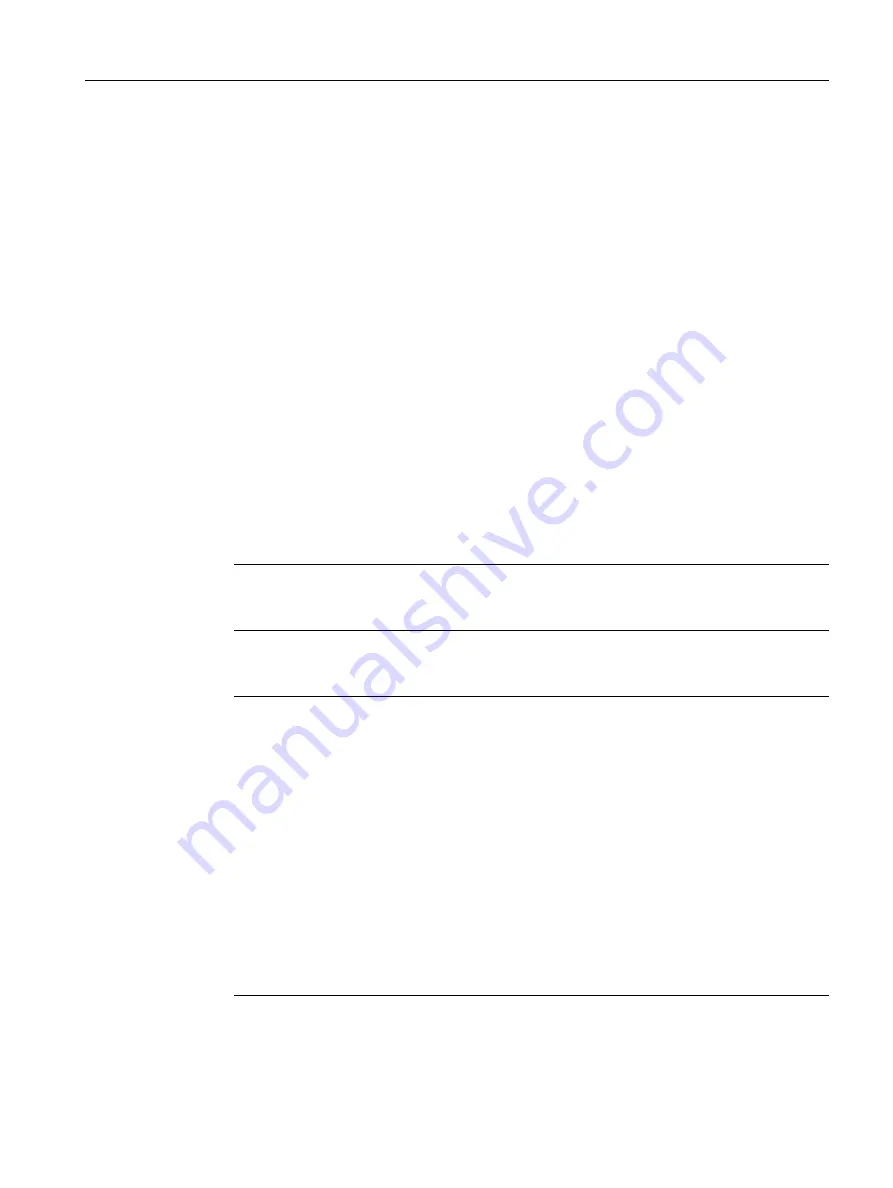
R1: Reference point approach
15.9 Referencing with absolute value encoders
Basic Functions
Function Manual, 09/2011, 6FC5397-0BP40-2BA0
1237
15.9.2
Calibration by entering a reference point offset
Function
During adjustment by entering the reference point offset, the difference between the position displayed on the
operator interface and the true actual position in the machine is determined and made known to the NC as
reference point offset.
Procedure
1. Determining the position of the machine axis with reference to the machine zero point via e.g.:
- position measurement (e.g. laser interferometer)
- Moving the machine axis to a known position (e.g., fixed stop)
2. Reading the displayed actual position of the machine axis on the operator interface.
3. Calculating the reference point offset (difference between the actual positions determined under point 1 and
2) and entering in machine data:
MD34090 $MA_REFP_MOVE_DIST_CORR (reference point offset)
4. Marking the absolute value encoder as adjusted:
MD34210 $MA_ENC_REFP_STATE = 2
5. Initiate POWER ON reset.
6. Controlling the position of the machine axis displayed on the operator interface.
Note
The encoder adjustment does not become active until the next time the encoder is
activated (e.g., when the controller is powered up).
Note
Backlash compensation
If backlash compensation is parameterized for a measuring system with absolute value
encoder, the following must be observed:
No backlash is permitted during machine axis travel to the adjusted machine position.
Activate reference point offset permanently
The entered reference point offset (MD34090) will be permanently active only after initial
POWER ON - Reset. If the machine axis is moved after the absolute encoder adjustment
without an interim POWER ON - Reset, the reference point offset entered in the machine
data can be overwritten, for example, as part of internal overrun offset.
Checking the actual position
Following adjustment of the absolute encoder, we recommend that you verify the actual
position of the machine axis the next time you power up the controller (POWER ON).
Содержание SINUMERIK 828D Turning
Страница 34: ...Basic Functions 34 Function Manual 09 2011 6FC5397 0BP40 2BA0 ...
Страница 146: ...A3 Axis Monitoring Protection Zones 2 6 Data lists Basic Functions 146 Function Manual 09 2011 6FC5397 0BP40 2BA0 ...
Страница 328: ...F1 Travel to fixed stop 6 5 Data lists Basic Functions 328 Function Manual 09 2011 6FC5397 0BP40 2BA0 ...
Страница 816: ...K2 Axis Types Coordinate Systems Frames 10 9 Data lists Basic Functions 816 Function Manual 09 2011 6FC5397 0BP40 2BA0 ...
Страница 1198: ...P4 PLC for SINUMERIK 828D 14 6 Function interface Basic Functions 1198 Function Manual 09 2011 6FC5397 0BP40 2BA0 ...
Страница 1752: ...Appendix 20 2 Overview Basic Functions 1752 Function Manual 09 2011 6FC5397 0BP40 2BA0 ...
Страница 1774: ...Glossary Basic Functions 1774 Function Manual 09 2011 6FC5397 0BP40 2BA0 ...