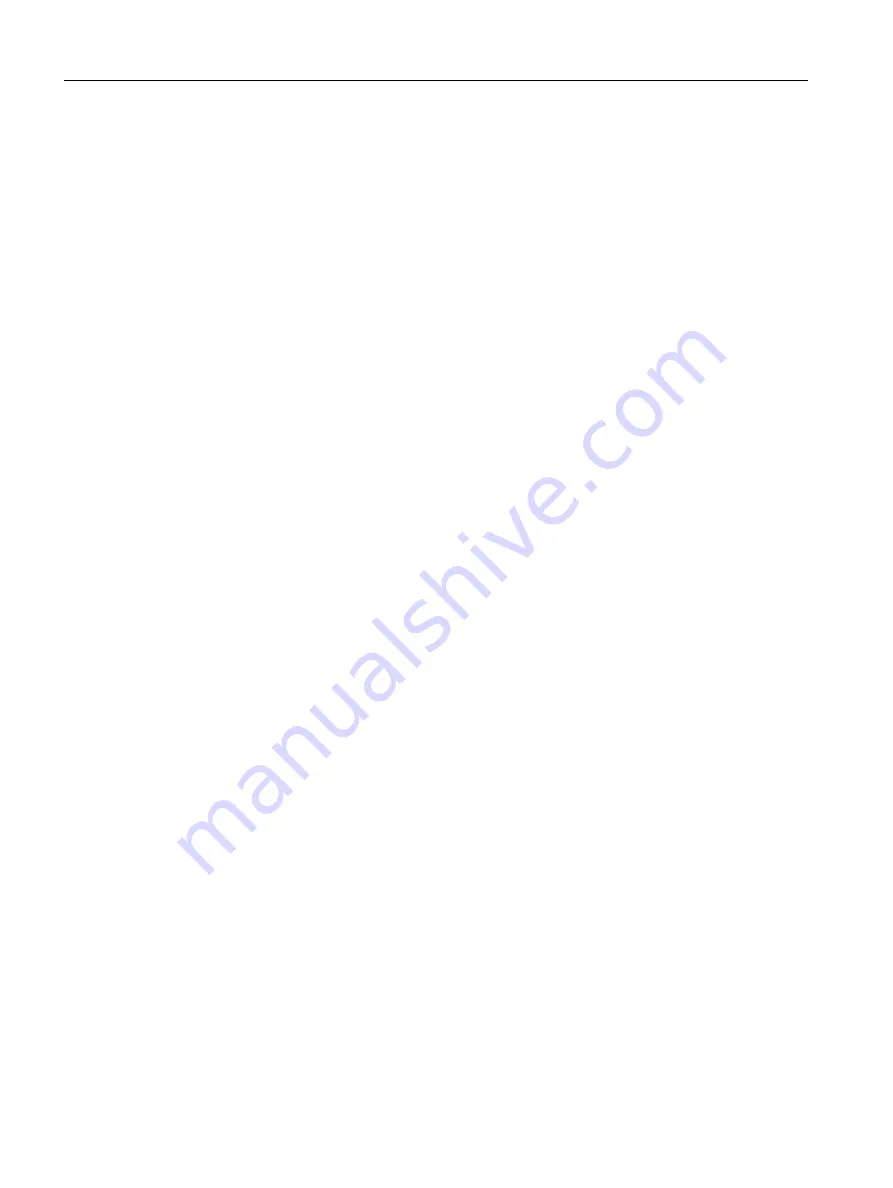
W1: Tool offset
18.6 Toolholder with orientation capability
Basic Functions
1520
Function Manual, 09/2011, 6FC5397-0BP40-2BA0
18.6.6
Programming
Selecting the toolholder
A toolholder is selected with the number m of the toolholder with:
TCARR = m
Access to toolholder data blocks
The following access is possible from the part program:
The current value of the parameter n for the tool holder m is written with the new "value" with::
$TC_CARRn[m] = value
The parameters of a tool holder m can, as far as the toolholder data set is already defined, read with:
value = $TC_CARRn[m]
(Value must be a
REAL
variable)
The toolholder data set number must lie in the range, which is defined by the machine data:
MD18088 $MN_MM_NUM_TOOL_CARRIER (Total number of toolholder data sets that can be defined)
This number of toolholder data sets, divided by the number of active channels, can be defined for a channel.
Exception:
If settings, which deviate from the standard, are selected via the machine data:
MD28085 $MC_MM_LINK_TOA_UNIT (Assignment of TO unit to a channel).
Canceling all toolholder data blocks
All values of all toolholder data sets can be deleted from within the part program using one command.
$TC_CARR1[0] = 0
Values not set by the user are preset to 0.
Activation
A toolholder becomes active when both a toolholder and a tool have been activated. The selection of the
toolholder alone has no effect. The effect of selecting a toolholder depends on the G code
TCOABS
/
TCOFR
(modal G-code group for toolholders).
Changing the G code in the
TCOABS
/
TCOFR
group causes recalculation of the tool length components when the
toolholder is active. With
TCOABS
, the values stored in the toolholder data for both angles of rotation α1 and α2
are used to determine the tool orientation.
With
TCOFR
, the two angles are determined from the current frame. The values stored in the toolholder data are
not changed, however. These are also used to resolve the ambiguity that can result when the angle of rotation is
calculated from one frame. Here, the angle that deviates least from the programmed angle is selected from the
various possible angles.
Содержание SINUMERIK 828D Turning
Страница 34: ...Basic Functions 34 Function Manual 09 2011 6FC5397 0BP40 2BA0 ...
Страница 146: ...A3 Axis Monitoring Protection Zones 2 6 Data lists Basic Functions 146 Function Manual 09 2011 6FC5397 0BP40 2BA0 ...
Страница 328: ...F1 Travel to fixed stop 6 5 Data lists Basic Functions 328 Function Manual 09 2011 6FC5397 0BP40 2BA0 ...
Страница 816: ...K2 Axis Types Coordinate Systems Frames 10 9 Data lists Basic Functions 816 Function Manual 09 2011 6FC5397 0BP40 2BA0 ...
Страница 1198: ...P4 PLC for SINUMERIK 828D 14 6 Function interface Basic Functions 1198 Function Manual 09 2011 6FC5397 0BP40 2BA0 ...
Страница 1752: ...Appendix 20 2 Overview Basic Functions 1752 Function Manual 09 2011 6FC5397 0BP40 2BA0 ...
Страница 1774: ...Glossary Basic Functions 1774 Function Manual 09 2011 6FC5397 0BP40 2BA0 ...