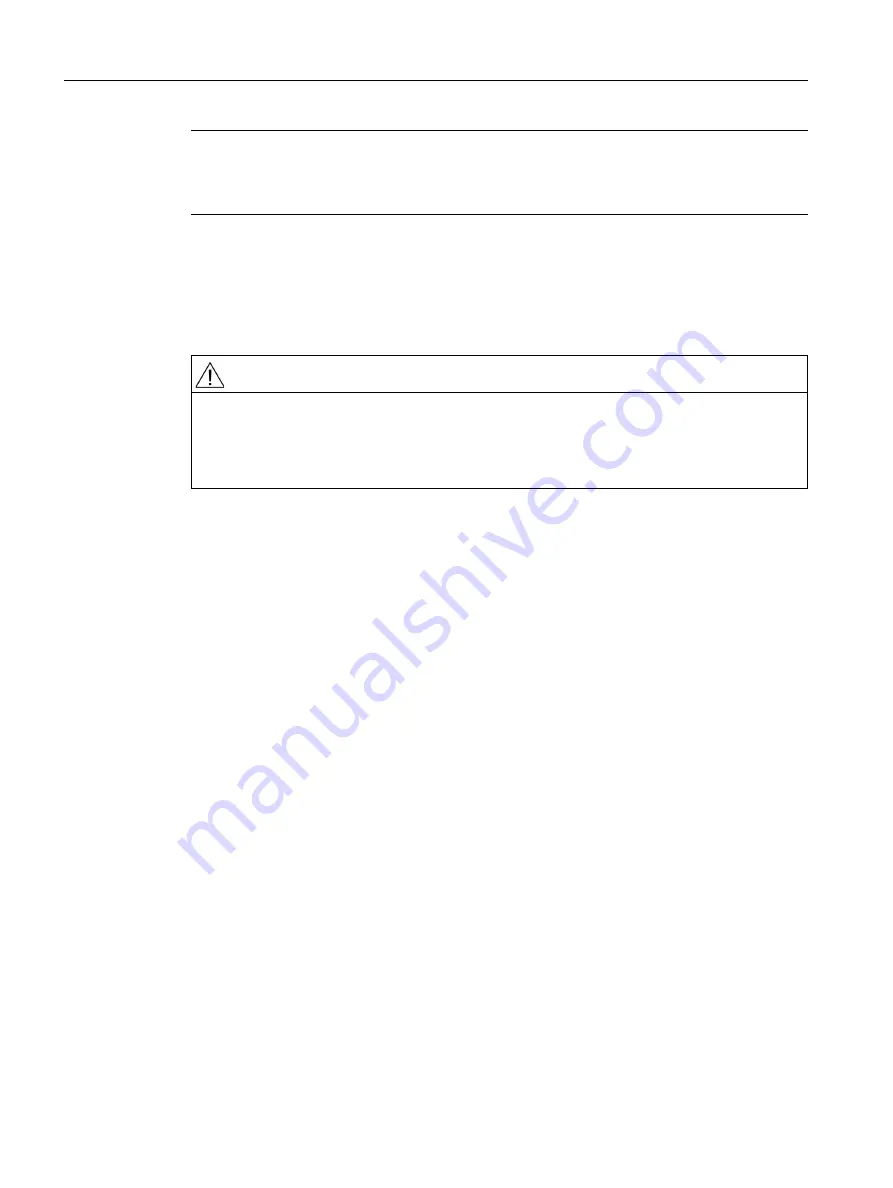
S1: Spindles
16.8 Spindle monitoring
Basic Functions
1348
Function Manual, 09/2011, 6FC5397-0BP40-2BA0
Diagnostics
Speed limiting using SD43235 is active, if the system variable $AC_SMAXVELO_INFO[<n>] has the value "21".
16.8.7
Maximum encoder limit frequency
Maximum encoder frequency exceeded.
If the spindle speed reaches a speed (large S value programmed), which exceeds the maximum encoder limit
frequency (the maximum mechanical speed limit of the encoder must not be exceeded), the synchronization is
lost. The spindle continues to rotate, but with reduced functionality.
With the following functions, the spindle speed is reduced until the active measurement system is operating
below the encoder limit frequency again:
• Thread cutting (
G33, G34, G35
)
• Tapping without compensating chuck (
G331, G332
)
• Revolutional feedrate (
G95
)
• Constant cutting rate (
G96, G961, G97, G971
)
•
SPCON
(position-controlled spindle operation)
When the encoder limit frequency is exceeded
NC/PLC IS:
DB31, ... DBX60.4 (Homed/Synchronized 1)
or
DB31, ... DBX60.5 (Homed/Synchronized 2)
are reset for the measurement system in question and NC/PLC IS:
DB31, ... DBX60.2 (encoder limit frequency 1 exceeded)
or
DB31, ... DBX60.3 (encoder limit frequency 2 exceeded)
are set.
If the spindle is in axis mode, the maximum encoder limit frequency must not be exceeded.
The maximum velocity (MD32000 $MA_MAX_AX_VELO) must lie below the maximum encoder limit frequency;
otherwise, alarm 21610 is output and the axis is brought to a standstill.
Note
The machine operator preferably changes the setting data via the user interface. However,
taking into account the fact that it becomes immediately effective in the part program, it can
be read and/or written.
CAUTION
The maximum encoder frequency limit of the actual spindle position encoder is monitored by
the control (the limit can be exceeded). It is the responsibility of the machine tool
manufacturer to ensure that the configuration of the spindle motor, gearbox, measuring
gearbox, encoder and machine data prevents the maximum speed of the actual spindle
position encoder being exceeded.
Содержание SINUMERIK 828D Turning
Страница 34: ...Basic Functions 34 Function Manual 09 2011 6FC5397 0BP40 2BA0 ...
Страница 146: ...A3 Axis Monitoring Protection Zones 2 6 Data lists Basic Functions 146 Function Manual 09 2011 6FC5397 0BP40 2BA0 ...
Страница 328: ...F1 Travel to fixed stop 6 5 Data lists Basic Functions 328 Function Manual 09 2011 6FC5397 0BP40 2BA0 ...
Страница 816: ...K2 Axis Types Coordinate Systems Frames 10 9 Data lists Basic Functions 816 Function Manual 09 2011 6FC5397 0BP40 2BA0 ...
Страница 1198: ...P4 PLC for SINUMERIK 828D 14 6 Function interface Basic Functions 1198 Function Manual 09 2011 6FC5397 0BP40 2BA0 ...
Страница 1752: ...Appendix 20 2 Overview Basic Functions 1752 Function Manual 09 2011 6FC5397 0BP40 2BA0 ...
Страница 1774: ...Glossary Basic Functions 1774 Function Manual 09 2011 6FC5397 0BP40 2BA0 ...