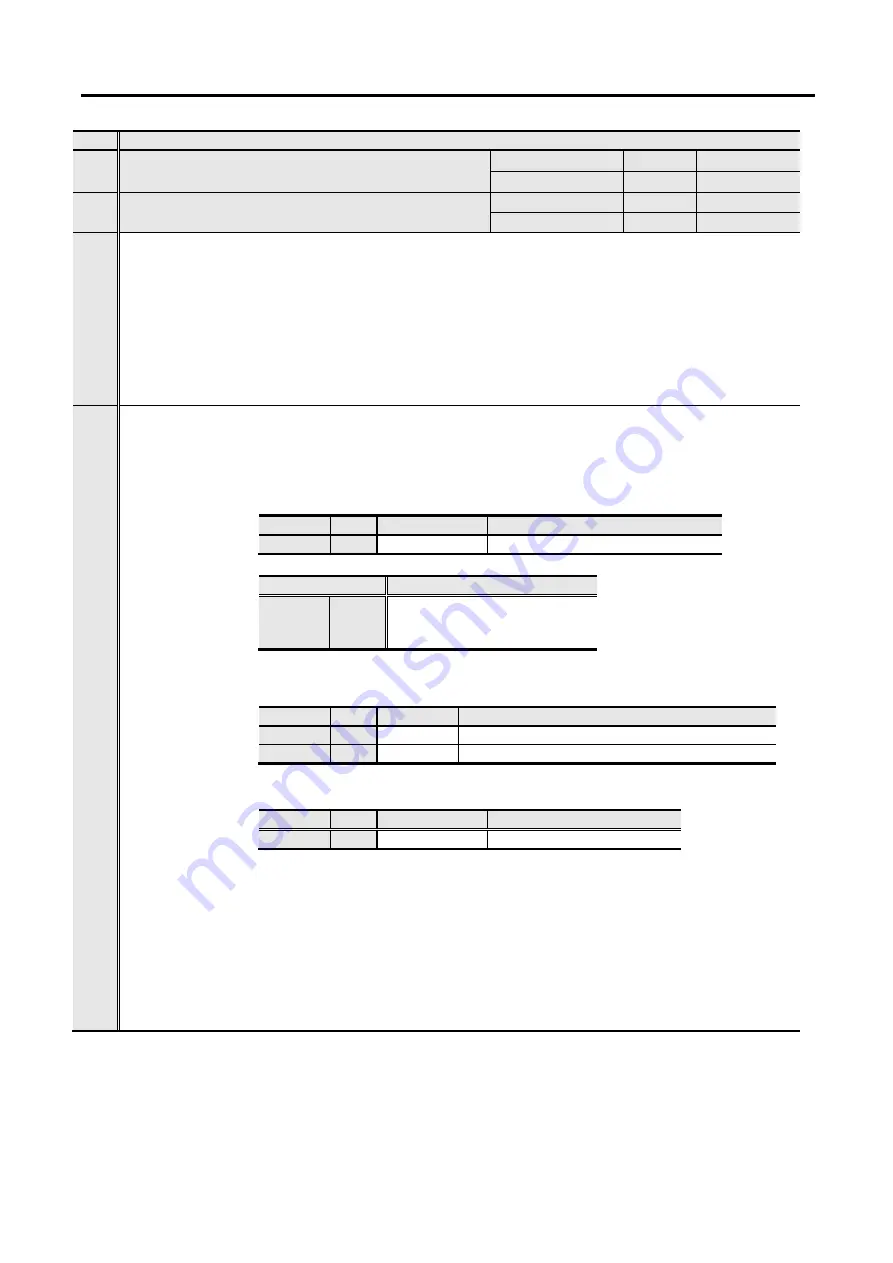
5. Operation
5-93
-
Group8
-
ID
Contents
37
Forward Direction Internal Torque Limit Value
[TCLM-F]
Setting range
Unit
Default
10.0 to 500.0
%
100.0
38
Reverse Direction Internal Torque Limit Value
[TCLM-R]
Setting range
Unit
Default
10.0 to 500.0
%
100.0
■
Limits the Torque output at this setting value when Preset torque limit value is valid.
Limits the torque by the ratio for the torque rating (100.0%= torque rating)
When the Torque Limit Function (TL) is valid, the torque output is limited by the Preset
torque limit setting value appropriate to the polarity of the Torque command.
When the following conditions are set, the torque output is limited by a rate of "Peak
armature current at stall (IP) / Rated armature current (IR)".
- In case of exceeding Peak torque at stall (Tp) of combination motor.
- In case of setting of exceeding a rate of "Peak armature current at stall (IP) / Rated
armature current (IR)".
■
About Torque limit function
There are two input systems of restricting Torque function:
Preset torque limit and External torque limit.
To use preset torque limit
Restricts the maximum output torque by using preset torque limit.
Sets torque limit value.
Sets torque limit function ON
Selects to set the Torque function being valid.
While the Torque limit function is valid, restricts torque.
✔
When setting, be cautious about acceleration/deceleration time. If the setting value is
too small, enough Acceleration/Deceleration torque can not get, and normal operation
can not get.
✔
Set at: Preset torque limit value > Acceleration/Deceleration torque.
✔
Preset torque limit can set individually to Forward and Reverse direction.
Group
ID
Symbol
Contents
8
36
TLSEL
Torque Limit Input Selection
Selection
Contents
00
TCLM
Use preset torque limit value
Forward side/TCLM-F
Reverse side/TCLM-R
Group
ID
Symbol
Contents
8
37
TCLM-F
Forward Direction Internal Torque Limit Value
8
38
TCLM-R
Reverse Direction Internal Torque Limit Value
Group
ID
Symbol
Contents
9
32
TL
Torque Limit Function
Содержание Sanmotion R 3E S
Страница 1: ...M0010630G For Rotary Motor Instruction Manual Analog Pulse Input Type ...
Страница 2: ......
Страница 76: ...No Text on This Page ...
Страница 88: ...No Text on This Page ...
Страница 266: ...No Text on This Page ...
Страница 332: ...No Text on This Page ...
Страница 408: ...No Text on This Page ...
Страница 444: ...No Text on This Page ...
Страница 482: ...12 Appendix 12 36 12 5 5 RS3A07A L 12 5 6 RS3A10A A 160 95 235 225 205 6 5 100 50 15 200 220 16 5 70 19 5 20 2 ...
Страница 511: ...12 7 Optional parts dimensions 12 65 12 Appendix REGIST 1000W Wiring diagram ...
Страница 512: ...No Text on This Page ...