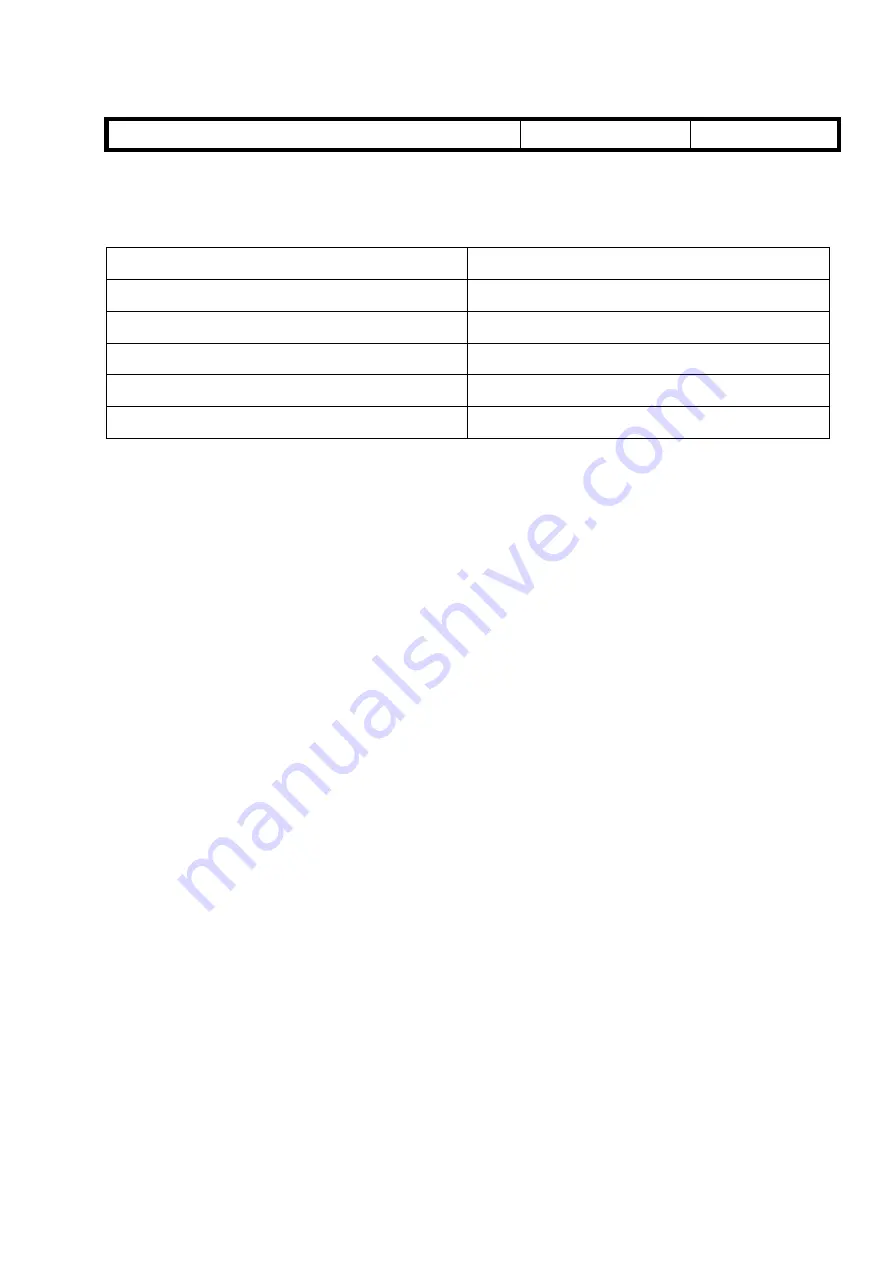
T
echnical
B
ulletin
PAGE: 22/51
Reissued: 1-Mar-19
Model:
Leo-C2/P2
Date:
27-Dec-18
No.:
RD0A5038b
4. If toner scattering still occurs replace the developer unit and developer.
The new development unit part number is D0A52301.
CUT IN SERIAL NUMBER
C858F500017
PRO C7200S
C878F610066
Pro C7200SX
Y988F510184
Pro C7200X
Y998F520014
Pro C7210X
3168F620001
ProC7200SL
5008F510084
Pro C7200
Содержание Leo-C2/P2
Страница 23: ...Technical Bulletin PAGE 3 3 Model Leo C2 P2 Date 6 Mar 18 No RD0A5003 Replace this description with the below...
Страница 213: ...Technical Bulletin PAGE 3 4 Reissued 18 Oct 18 Model Leo C2 P2 Date 14 Sep 18 No RD0A5034a...
Страница 219: ...Technical Bulletin PAGE 5 10 Reissued 26 Oct 18 Model Leo C2 P2 Date 18 Oct 18 No RD0A5035a Flow Chart...
Страница 227: ...Technical Bulletin PAGE 3 3 Model Leo C2 P2 Date 25 Oct 18 No RD0A5036 7 Rebuilt the part back to original...
Страница 238: ...Technical Bulletin PAGE 3 51 Reissued 1 Mar 19 Model Leo C2 P2 Date 27 Dec 18 No RD0A5038b Image Quality...
Страница 241: ...Technical Bulletin PAGE 6 51 Reissued 1 Mar 19 Model Leo C2 P2 Date 27 Dec 18 No RD0A5038b...
Страница 247: ...Technical Bulletin PAGE 12 51 Reissued 1 Mar 19 Model Leo C2 P2 Date 27 Dec 18 No RD0A5038b Flow Chart...
Страница 263: ...Technical Bulletin PAGE 28 51 Reissued 1 Mar 19 Model Leo C2 P2 Date 27 Dec 18 No RD0A5038b JAM...
Страница 268: ...Technical Bulletin PAGE 33 51 Reissued 1 Mar 19 Model Leo C2 P2 Date 27 Dec 18 No RD0A5038b SC...
Страница 278: ...Technical Bulletin PAGE 43 51 Reissued 1 Mar 19 Model Leo C2 P2 Date 27 Dec 18 No RD0A5038b Fiery...
Страница 282: ...Technical Bulletin PAGE 47 51 Reissued 1 Mar 19 Model Leo C2 P2 Date 27 Dec 18 No RD0A5038b Notices...