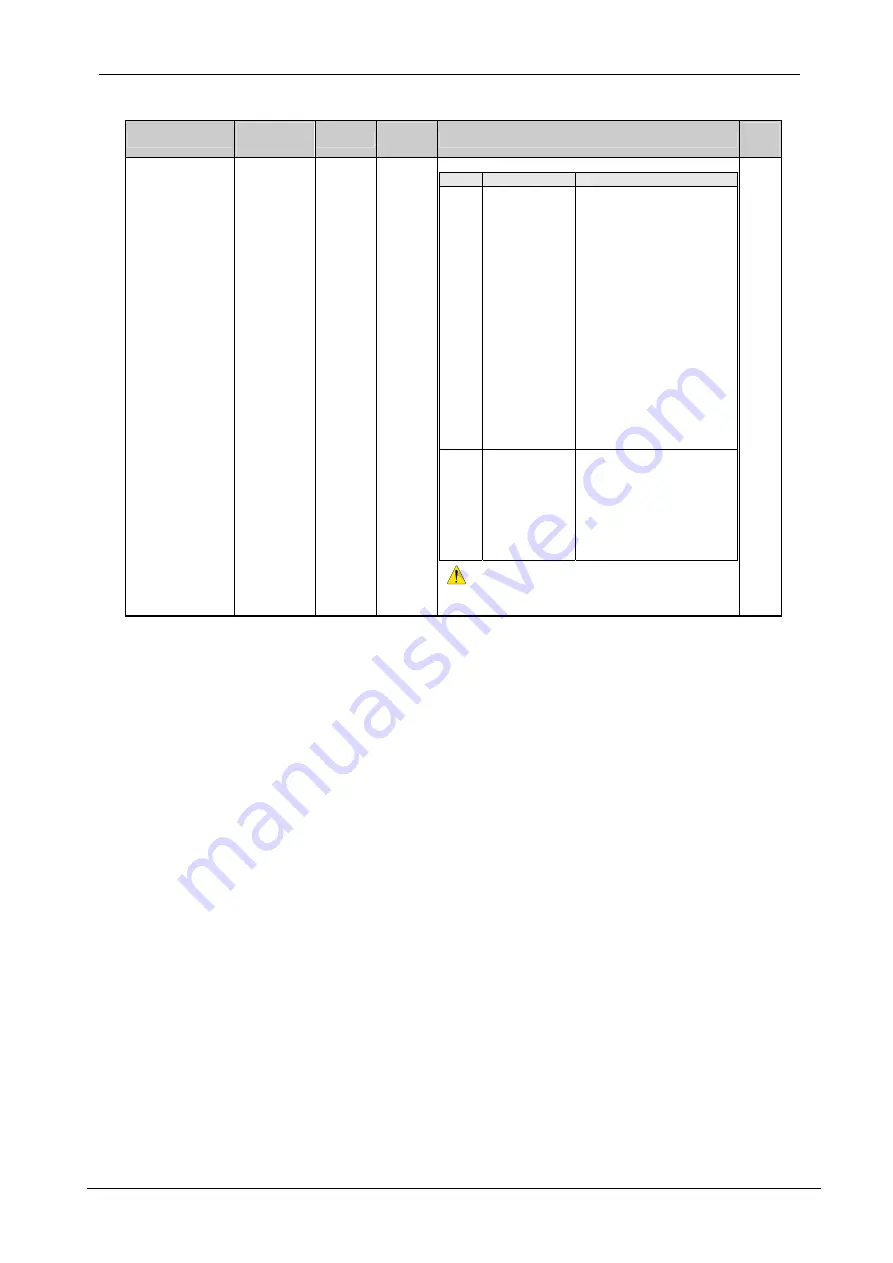
SDRIVE 700
POWER ELECTRONICS
50
DESCRIPTION OF PROGRAMMING PARAMETERS
Parameter
Name /
Description
Range
Default
value
Function
Set on
RUN
4 DIGIT I MODE=1
G4.1.4
/
Selection of
Digital Inputs
configuration
0 – 5
1
Note:
Coming from the previous page.
OPT
DESCRIPTION
FUNCTION
4
MOTORIZED
POT
It assigns the up and down
reference function for two of the
digital inputs.
DI5 = Up (NO contact)
DI6 = Down (NC contact)
Reference limits will be the
speed limits set in 'G10 LIMITS'.
Programming a change ramp is
possible at:
G5.7 PMT ACL1=3%/s
G5.8 PMT DCL1=3%/s
G5.9 PMT ACL2=1%/s
G5.10 PMT DCL2=1%/s
G5.11 PMOT BRK=OFF
Note:
In this mode, the reference
set by potentiometer will be
memorized even if the motor is
stopped and also in the case of a
power loss.
5 ERASAB
POT
It operates in the same way as
option 4, but when the motor is
stopped or a power loss occurs,
the reference will not be
memorized. In this case the
minimum reference value set in
G10.1 or G10.3 will be the
default speed.
Caution:
Digital input configuration changes their settings
automatically. Make sure there is not a hazard due to accidental
motor starting that can cause property damage or personal injury.
NO
Pumps program activation, in G1.7 PROG = PUMP, requires the following considerations:
There are some configuration options available when the pump program is active, which can be set in the
same way that the options available in the standard program.
Nevertheless, when the pump program is active, the drive will assume that only the configurable options
from 50 to 69 (for G4.1.5 to G4.1.10) can be set, without taking into consideration the setting on parameter
‘G4.1.4 DIGIT I MODE’, which means a block setting.
All that means that the user will configure the pump program freely, according to his requirements,
selecting the correct functionality and protections. For a correct programming of the digital inputs when the
pump program is active, there is additional information in G25 Pump Control.
Note
: Selection of the pump program will set all the Digital Inputs to mode ‘00 – un used’. If re-
programming is needed, it will be necessary to configure their functionality in a separate way again. So it
guarantees a safety installation operation, avoiding that hardware external to the equipment can cause any
kind of damage.
Note:
The digital outputs will also be affected due to pump control activation.
To select one auxiliary pump it is necessary to act in the following way:
o
Set any free digital input to options ‘52 FIX PUMP1 FLT’, ‘53 FIX PUMP2 FLT’, ‘54 FIX
PUMP3 FLT’, ‘55 FIX PUMP4 FLT’ or ‘56 FIX PUMP5 FLT’
o
To enable the control of the pump in the corresponding screen G25.9.1, G25.9.2,
G25.9.3, G25.9.4 and G25.9.5 respectively.
To remove this pump configuration and release the relay for another use, the user should:
o
Disable the control of the pump in the corresponding screen G25.9.1, G25.9.2, G25.9.3,
G25.9.4 or G25.9.5 respectively.