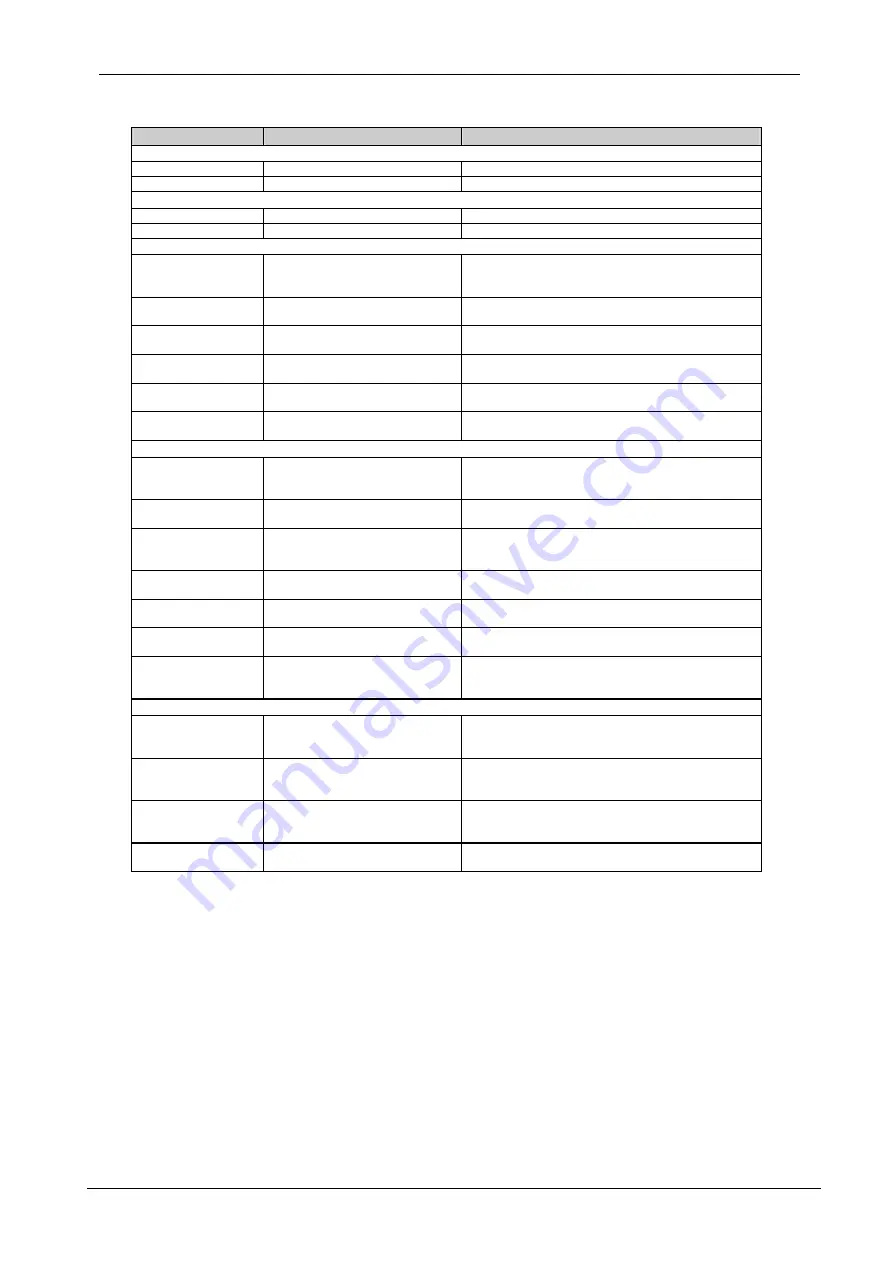
SDRIVE 700
POWER ELECTRONICS
110
COMMONLY USED CONFIGURATIONS
Parameter
Name / Description
Value
G25: Pump Control - S25.1: Setpoints.
1 CONTROL MODE=1
G25.1.1
/ Control mode
1
Î
Pumps. The drive will start in pump control mode.
5 SETPT1=x.xBar
G25.1.5
/ Setpoint 1 for the PID
x.xBar
Î
Local setpoint 1. (Set according to the installation).
G25: Pump Control - S25.2: PID Setting.
1 PID SETP=LOCAL
G25.2.1
/ PID reference source
LOCAL
Î
Speed reference introduced by keypad.
2 PID FBK=AI2
G25.2.2
/ PID feedback source
AI2
Î
Feedback signal connected to Analogue Input 2.
G25: Pump Control – S25.3: Start Conditions.
1 Lp Pon=0.0%
G25.3.1
/ Wake up level of the drive
x.x%
Î
When demand decreases, the drive can go in sleep mode.
(It allows setting the wake up level for the drive. This value is set as
percentage of PID setpoint).
2 FP SpON=90.0%
G25.3.2
/ Start speed for the fixed pumps
90.0%
Î
It sets the drive speed above which fixed pumps will
start. (Set according to the installation).
3 FP ErON=10.0%
G25.3.3
/ Minimum PID error to start fixed
pumps
10.0%
Î
This parameter allows user to consider the PID error (%)
at the moment of starting fixed pumps.
4 FP T1 ON=10.0s
G25.3.4
/ Delay time to start fixed pump 1 10.0s
Î
It sets the delay time to start the fixed pump associated to
the relay 1.
5 FP T2 ON=10.0s
G25.3.5
/ Delay time to start fixed pump 2 10.0s
Î
It sets the delay time to start the fixed pump associated to
the relay 2.
6 FP T3 ON=10.0s
G25.3.6
/ Delay time to start fixed pump 3 10.0s
Î
It sets the delay time to start the fixed pump associated to
the relay 3.
G25: Pump Control – S25.4: Stop Conditions.
1 LP T SLP=20s
G25.4.1
/ Delay time before activating sleep
mode
20s
Î
This delay time will be applied to any conditions that
activate the sleep mode. These conditions are: sleep speed, No
Flow input, Flow measurement and sleep current.
2 40.0%
G25.4.2
/ Sleep speed for local setpoint 1
+40.0%
Î
The drive will sleep below the value set here whenever
local setpoint 1 is selected.
13 FP erOFF=+0.0%
G25.4.13
/ Maximum PID error to stop fixed
pumps
0.0%
Î
This parameter allows user to consider the PID error (%)
at the moment of stopping fixed pumps. (Set according to the
requirements).
14 FP T1 OF=10s
G25.4.14
/ Delay time to stop fixed pump 1 10s
Î
It sets the delay time to stop the fixed pump associated to
the relay 1.
15 FP T2 OF=10s
G25.4.15
/ Delay time to stop fixed pump 2 10s
Î
It sets the delay time to stop the fixed pump associated to
the relay 2.
16 FP T3 OF=10s
G25.4.16
/ Delay time to stop fixed pump 3 10s
Î
It sets the delay time to stop the fixed pump associated to
the relay 3.
19 70.0%
G25.4.19
/ Stop speed 1 for one fixed pump
+70.0%
Î
It sets the speed below which the drive must remain to
stop one fixed pump whenever the operating setpoint is local
setpoint 1 adjusted in G25.1.5.
G25: Pump Control – S25.9: Fixed Pumps Control.
1 ENABLE PUMP1=Y
G25.9.1
/ To enable fixed pump associated
to relay 1
Y=YES
Î
If setting is set to NO relay 1 will be free for user
configuration. If set to YES relay 1 will be pre-defined as fixed
speed pump 1.
2 ENABLE PUMP2=Y
G25.9.2
/ To enable fixed pump associated
to relay 2
Y=YES
Î
If setting is set to NO relay 2 will be free for user
configuration. If set to YES relay 2 will be pre-defined as fixed
speed pump 2.
3 ENABLE PUMP3=Y
G25.9.3
/ To enable fixed pump associated
to relay 3
Y=YES
Î
If setting is set to NO relay 3 will be free for user
configuration. If set to YES relay 3 will be pre-defined as fixed
speed pump 3.
4 FP ALTER MOD=1
G25.9.4
/ To enable fixed pump alternation
mode
1
Î
Cycle (The pump that starts will be the next pump in
sequence to the last pump stopped).
12.5.2.
Connections Drawing
There are several configuration options available when pump program is activated. These options
can be configured like in standard program.
Nevertheless, unlike standard program, when pump program is activated, the drive will only allow
setting the options of each digital input (from G4.1.5 to G4.1.10) and will not consider the setting
realized in parameter ‘G4.1.4 DIGIT I MODE’, where digital inputs are set in groups.
This means that user will configure the pump program as he wants, by selecting the functionality
and protections that he needs. For a correct configuration of the inputs when pump program is
active, see chapter G25 Pump Control to get additional information.