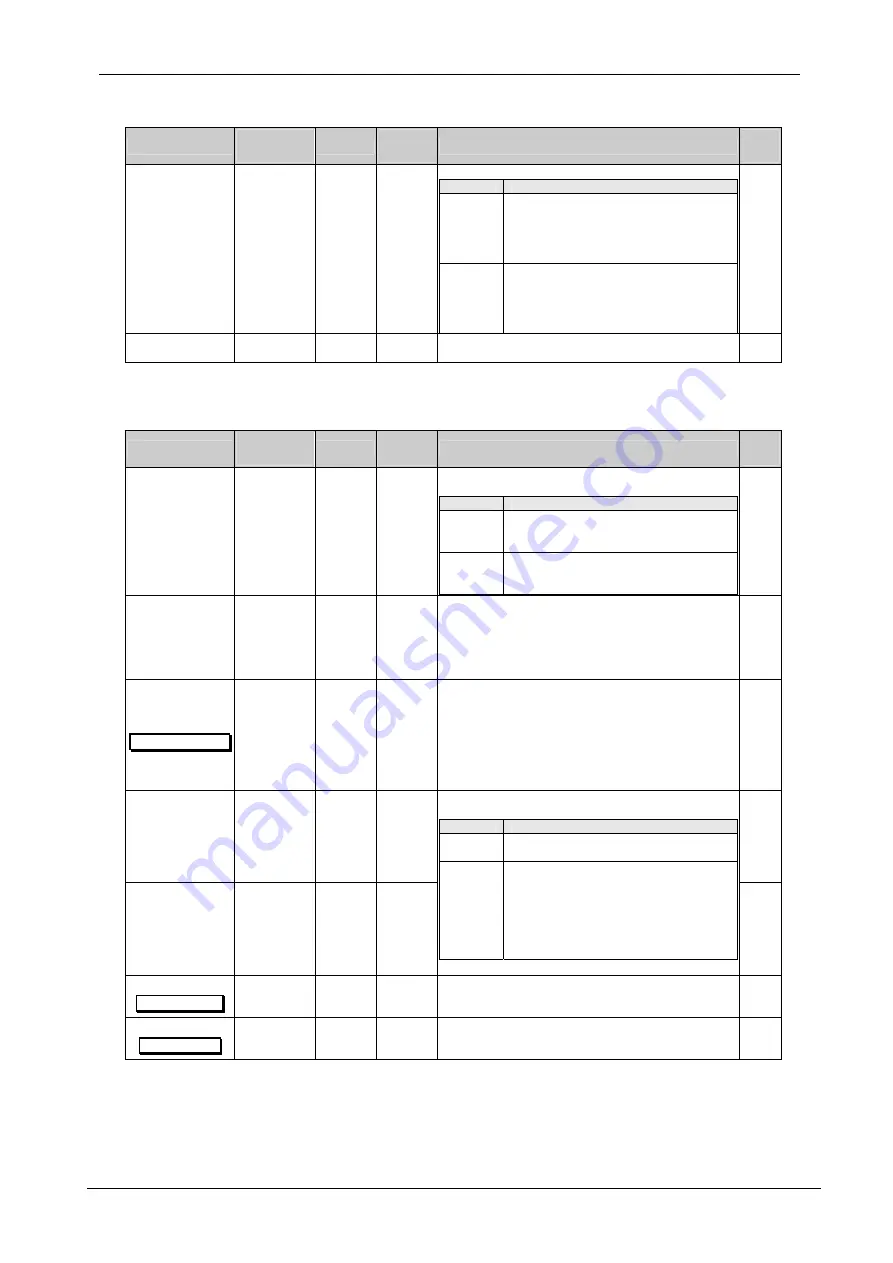
SDRIVE 700
POWER ELECTRONICS
58
DESCRIPTION OF PROGRAMMING PARAMETERS
Parameter
Name /
Description
Range
Default
value
Function
Set on
RUN
7 INVERT PID=N
G6.7
/ PID output
inversion
N
Y
N
It allows inverting the PID output of the drive.
OPTION
FUNCTION
N=NO
PID regulator responds in normal mode, that
means, when the feedback value is above the
reference signal value, speed will be decreased.
If the feedback value is below the reference
signal value, speed will be increased.
Y=YES
PID regulator responds in inverse mode. So,
when the feedback value is above the reference
signal value, speed will be increased. If the
feedback value is below the reference signal
value, speed will be decreased.
NO
8 ERR PID = +0.0%
G6.8
/ PID
control error
- -
It shows the difference between the reference 'G6.1 SEL REF' and
the feedback signal of the process 'G6.3 SEL FBK'.
-
10.7.
Group 7 – G7: Start / Stop Mode Configuration
Parameter
Name /
Description
Range
Default
value
Function
Set on
RUN
1 STOP 1 = RAMP
G7.1
/ Stop
mode 1
RAMP
SPIN
RAMP
It selects the main stop mode of the drive. This value should be
configured appropriately for each application.
OPT
FUNCTION
RAMP
The drive will stop applying a frequency ramp to
stop the motor. The rate of stop is determined in
screen 'G5.2 Decel 1'
SPIN
The drive will turn off the output to the motor. The
motor sill coast to stop. Stopping time is
determined by system inertia.
YES
2 STOP 2 = SPIN
G7.2
/ Stop
mode 2
RAMP
SPIN
SPIN
User can select an alternative stop mode of the drive if required.
This value should be set for each application. For options
information see parameter ‘G7.1 STOP 1=RAMP’.
Note:
Stop mode 1 or 2 can be selected by digital inputs, by
comparator output functions, or by setting a changing speed for stop
mode in 'G7.3 BRK STP 2'.
YES
3 BRK STP 2 = OFF
STP2 UNDER SPEED
G7.3
/ Changing
speed for stop
mode
OFF=0 to
250%
OFF
When this parameter is set to a value other than zero a second
stopping profile can be activated based on motor speed. When the
drive receives a stop mode 1 command, it will stop from steady
status to the speed set here. At that moment, the drive will apply
stop mode 2 to complete the stop.
Note:
Stop mode 1 or 2 can be selected by digital inputs, by
comparator output functions, or by setting a changing speed for stop
mode in 'G7.3 BRK STP 2'.
YES
4 START = RAMP
G7.4
/ Start
mode
RAMP
SPIN
RAMP YES
5 START 2=RAMP
G7.5
/ Start
mode 2
RAMP
SPIN
RAMP
It selects the start mode of the drive. This value should be
configured appropriately for each application.
OPT
FUNCTION
RAMP
Drive will start applying a frequency ramp to the
motor.
SPIN
In this mode, the motor shaft speed is
automatically searched for and the frequency
output of the drive is set to match the actual
motor speed. From this point the motor is then
accelerated normally up to the reference speed.
This allows starting loads that are already rotating
when the drive receives a start command.
YES
6 STAR DLY = OFF
DELAY TO START
G7.6
/ Start
delay time
OFF=0 to
6500s
OFF
Allows setting of a delay time from the moment the drive receives
the start command to the beginning of providing an output frequency
to the motor.
YES
7 STOP DLY = OFF
DELAY TO STOP
G7.7
/ Stop delay
time
OFF=0 to
6500s
OFF
Allows setting of a delay time applied from the moment the drive
receives the stop command until the drive stops providing an output
frequency to the motor.
YES