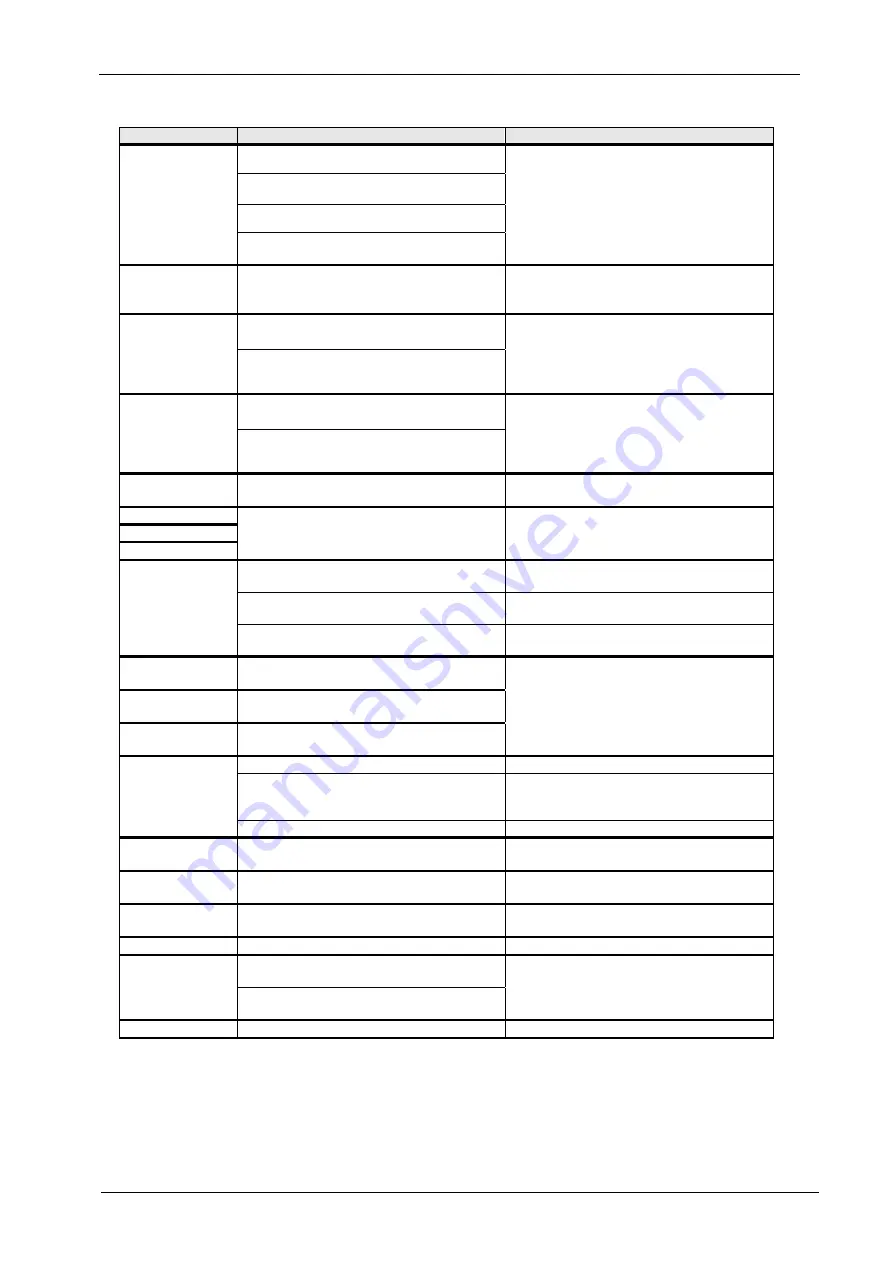
POWER ELECTRONICS
SDRIVE 700
FAULT MESSAGES. DESCRIPTIONS AND ACTIONS
101
DISPLAY
POSSIBLE CAUSE
ACTIONS
High current used by the motor due to heavy load.
The load exceeds the capacity of motor cooling
under normal operating conditions.
Incorrect setting of the thermal model parameters.
F25 MTR O/L
Phase loss of the motor or a fault in motor
windings.
Check the motor load.
Check the setting of parameters ‘G2.1 MTR CUR’
and ‘G2.7 MTR COOL’ relating to the motor
thermal model. Increasing the parameter ‘G2.7
MTR COOL’, can be undertaken when there is a
motor PTC fitted and it is connected to the SD700.
F27 DL SMTH
Potential damage to the soft charge resistors of the
SD700.
Try to reset the fault. Disconnect and re-connect
again the input power. If the fault persists contact
Power Electronics for technical service.
Input power fault.
F28 MICRO FLT
Parameters setting is not recognised.
Disconnect and re-connect SD700 input power of
the drive. If the same fault appears, initialize all of
the parameters (parameter ‘G1.5 INITIALISE’) and
connect the input power again. If the fault persists,
request technical assistance.
Input power fault.
F29 DSP FLT
Parameters setting is incoherent.
Disconnect and connect again SD700 input power.
If the same fault appears, initialize all of the
parameters (parameter ‘G1.5 INITIALISE’) and
connect the input power again. If the fault persists,
request technical assistance.
F30 WATCHDOG
Input power fault.
Reset the fault; If the fault persists, request
technical assistance.
F31 SCR L1
F32 SCR L2
F33 SCR L3
A conduction fault has been produced in the
corresponding thyristor. The thyristor is OFF when
it should be on.
Try to reset the fault. Disconnect and re-connect
again the input power. If the fault persists request
technical assistance.
Blocked or poor ventilation.
Check if there is an object blocking ventilation.
Improve the cooling.
Heat sink and cooling fan fault on the SD700.
Check if the heat sink and the cooling fan are
operating correctly.
F34 IGBT TEMP
Ambient temperature is higher than 50°C.
Check the cooling and thermal conditions. Request
technical assistance.
F35 PHSE L1 LOSS
Input phase L1 is not connected correctly or there
is no voltage on it.
F36 PHSE L2 LOSS
Input phase L2 is not connected correctly or there
is no voltage in it.
F37 PHSE L3 LOSS
Input phase L3 is not connected correctly or there
is no voltage in it.
Verify the wiring of the input power supply of the
drive. Check input voltage and input fuses.
External trip device has operated.
Check the external trip switch (if exists).
Motor is overheated (motor load exceeds the
cooling capacity at operating speed).
Check motor temperature.
To reset the fault the motor must be return to
normal temperature.
F40 EXT / PTC
Fault in sensor connection.
Check sensor wiring.
F41 COMMS TRIP
Trip generated by a computer through serial
communication.
Disconnect the SD700 from the communication
network and verify if the fault is generated again.
F42 AIN1 LOSS
Analogue input cable has been come loose or
disconnected (terminals 10 and 11).
Verify the wiring and the device which provides the
analogue signal.
F43 AIN2 LOSS
Analogue input cable has been come loose or
disconnected (T12 and T13).
Verify the wiring and the device which provides the
analogue signal.
F44 CAL FLT
SD700 fault.
Verify drive select. Request technical assistance.
Deceleration ramps (parameters ‘G5.2 DECEL1’
and ‘G5.4 DECEL2’) are too slow.
F45 STOP T/O
SD700 is voltage limiting voltage due to
regeneration from the motor.
Verify that the time set in parameter ‘G11.2 STOP
TO’ to stop the system after setting deceleration
ramps and checking the system performance.
F46 EEPROM FLT
Integrated circuit fault.
Request technical assistance.