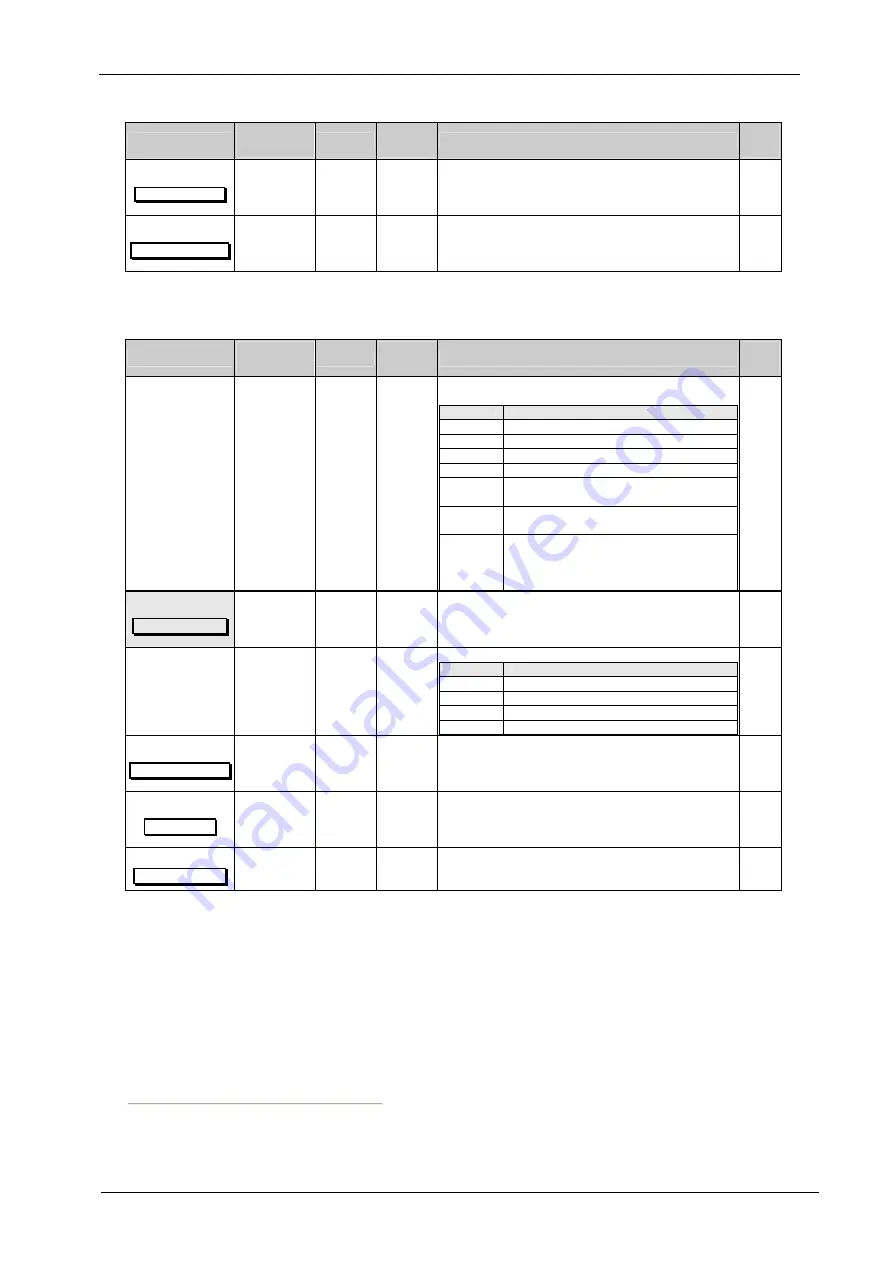
POWER ELECTRONICS
SDRIVE 700
DESCRIPTION OF PROGRAMMING PARAMETERS
57
Parameter
Name /
Description
Range
Default
value
Function
Set on
RUN
11 MPOT BRK = OFF
MOTO POT BRKPOIN
G5.11
/ Speed
for ramp change
with motorized
pot.
OFF=0 to
250%
OFF
This parameter sets the break frequency for the alternative
acceleration and deceleration reference ramp when using motorized
potentiometer. This parameter is the speed at which the change in
motorized potentiometer reference ramp profile takes place.
YES
12 SP FLT=0.250s
SMOOT SPD FILTER
G5.12
/ Time
constant to filter
the speed
0.000 –
60.0s
0.250s
S-Curve can be introduced if smoother performance during
acceleration and deceleration is required. S-Curve introduces a filter
for speed reference changes during ‘Start/Stop’ and acceleration
and deceleration. It is especially useful in cranes and elevators.
YES
10.6.
Parameter
Name /
Description
Range
Default
value
Function
Set on
RUN
1 SEL REF=MREF
G6.1
/ Source
selection for
introducing
reference signal
NONE
AI1
AI2
RESERV
MREF
LOCAL
locPID
MREF
It allows user to select the reference source for the set point of the
PID regulator.
OPTION
FUNCTION
NONE Source
disabled.
AI1
PID set point introduced by Analogue Input 1.
AI2
PID set point introduced by Analogue Input 2.
RESERV
Reserved for future use.
MREF
PID set point introduced by Digital Inputs
configured as Multi-references.
LOCAL
PID set point introduced by keypad. Value can be
adjusted in screen 'G3.3 LOCAL SPD'.
locPID
PID set point introduced by keypad. Value is set
in 'G6.2 PID LOC'. It allows user to have two
speed references because 'G3.3 LOCAL SPD' is
not modified.
NO
2 PID LOC=+100%
5
PID LOCAL SETPOI
G6.2
/ PID local
reference
+0.0% to
+400%
+100%
When ‘locPID’ is set as set point source, the reference introduced
by keypad will be memorized in this parameter. The value of the
parameter 'G3.3 LOCAL SPD' is not modified and it is available if
we want to use alternative speed reference.
YES
3 SEL FBK=AI2
G6.3
/ Selection
of feedback
signal source
NONE
AI1
AI2
RESERV
AI2
To select the source of the feedback signal for the PID control loop.
OPTION
FUNCTION
NONE
The PID function is not active
AI1
Feedback signal through the Analogue Input 1
AI2
Feedback signal through the Analogue Input 2
RESERV Reserve
NO
4 GAIN Kp=8.0
PID PROPORTIONAL
G6.4
/
Proportional gain
of PID control
0.1 to 20
8.0
It allows setting the proportional gain value of the PID regulator. If
you need a higher control response, increase this value.
Note:
If this value is increased too much, a higher instability in the
system can be introduced.
YES
5 INTEGRAL = 0.0s
PID INTEGRAL
G6.5
/ Integration
time of PID
control
0.0 – 1000s,
Max
0.0s
It allows setting the integration time of the PID regulator. If you need
a higher accuracy you should increase this value.
Note:
If this value is increased too much, the system can become
slower.
YES
6 DIFFEREN = 0.0s
PID DIFFERENTIAL
G6.6
/ Derivation
time of PID
control
0.0 – 250s
0.0s
It allows setting the derivate time of the PID regulator. If you need a
higher response, you can increase this value.
Note:
If this value is increased too much, accuracy can decrease.
YES
Note:
PID functions will be set here if this function is enabled in the parameters 'G3.1 REF1 SPD=LOCAL' or 'G3.2 2
REF2 SPD=LOCAL'.
5
It will be available if 'G6.1 SEL REF = locPID'.