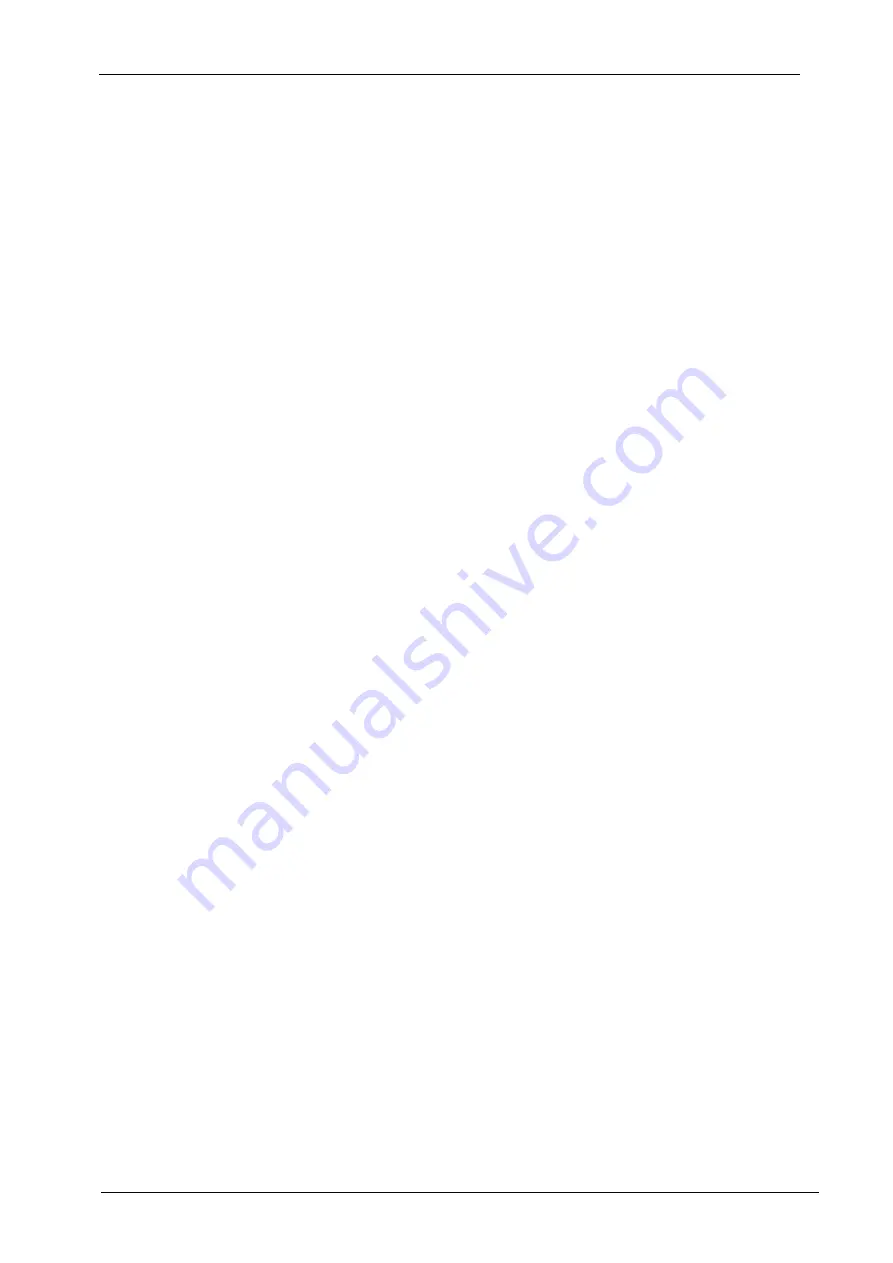
POWER ELECTRONICS
SDRIVE 700
DESCRIPTION OF PROGRAMMING PARAMETERS
81
o
Cavitation:
Configurable at Pause mode or at Fault mode. If it is set as Pause, the
displayed message will be ‘CAVITATION PAUSE’ but if this is set to Fault, the message
will be ‘F68 CAVIT/UNDERL’
Note: The pauses are not faults, consequently the do not generate a fault code and they
will not be stored in the fault history.
Faults of Pumps Program:
That means the drive or installation faults that have been
configured from the pump program. In case of any of these conditions occur, the motor
controlled by the drive will stop, followed by the fixed pumps and the display will show the
corresponding fault message. These fault will be treated in the same way than the general
faults, some of them are:
o
High Pressure Fault:
It can be provoked through a digital input which has been
configured in this mode or by comparison of the received data of an analogue input. This
information will be compared with the setting realized in parameters G25.6.11 to
G25.6.13. The display will show ‘F66 HI PRESSURE’.
o
Low Pressure Fault:
Pipe broken possibility. The display will show ‘F65 LOW
PRESSURE’.
o
No Water Fault:
This is especially useful in the use of level proves at wells. The display
will show ‘F67 LOW WATER’.
o
Short Starting Cycle Fault:
Produced when the drive tries to start before the
established time between a start and a stop has expired. For additional information, see
G25.6.20. In this case, the display will show ‘F71 CYCLING’.
o
Irrigation Equipment Fault:
Produced by a digital input configured for this objective.
The display will show ‘F70 IRRIGATOR F’.
o
No Flow Fault:
Produced by a digital input configured in this option. The display will
show ‘F69 FLOW SWITCH’.
o
Cavitation:
Produced by operation on underload conditions. The display will show ‘F68
CAVIT/UNDERL’.
o
Pressure Switch:
(Only with Priming pump). The Pressure switch is open out of the
allowed time, indicating a sudden pressure loss. The display will show ‘F72 IN PRES
SW’.
10.20.4.
Inputs Configuration.
For inputs configuration, it is necessary to consider some rules which will help in order to get a
correct system configuration.
Digital input for flow acquisition by pulse counter.
All digital input can be configured in this option ‘51 FLOW PULSE’. The parameters for
setting the flowmeter are located in the subgroup G4.4 Pulses Input.
The read flow can be used to limit the flow of the application, see group G25.10 Flow
Limitation Algorithm. An analogue output can be configured to show this information (by
setting the option ’20 CURRENT FLOW’), in this way this information can be used for the
PLC or even can be connected to the drive as a feedback signal in PID mode without
needing the use of external converter of pulses signal into 4-20mA signal.
Inputs programming.
Pumps program activation, in G1.7 PROG = PUMP, requires the following considerations:
There are some configuration options available when the pump program is active, which can
be set in the same way that the options available in the standard program.
Nevertheless, when the pump program is active, the drive will assume that only the
configurable options from 50 to 69 (for G4.1.5 to G4.1.10) can be set, without taking into
consideration the setting on parameter ‘G4.1.4 DIGIT I MODE’, which means a block setting.
All that means that the user will configure the pump program freely, according to his
requirements, selecting the correct functionality and protections.
The options for inputs configuration, standard program options as well as pump program
options have been detailed in the corresponding group G4.1 Digital Inputs.