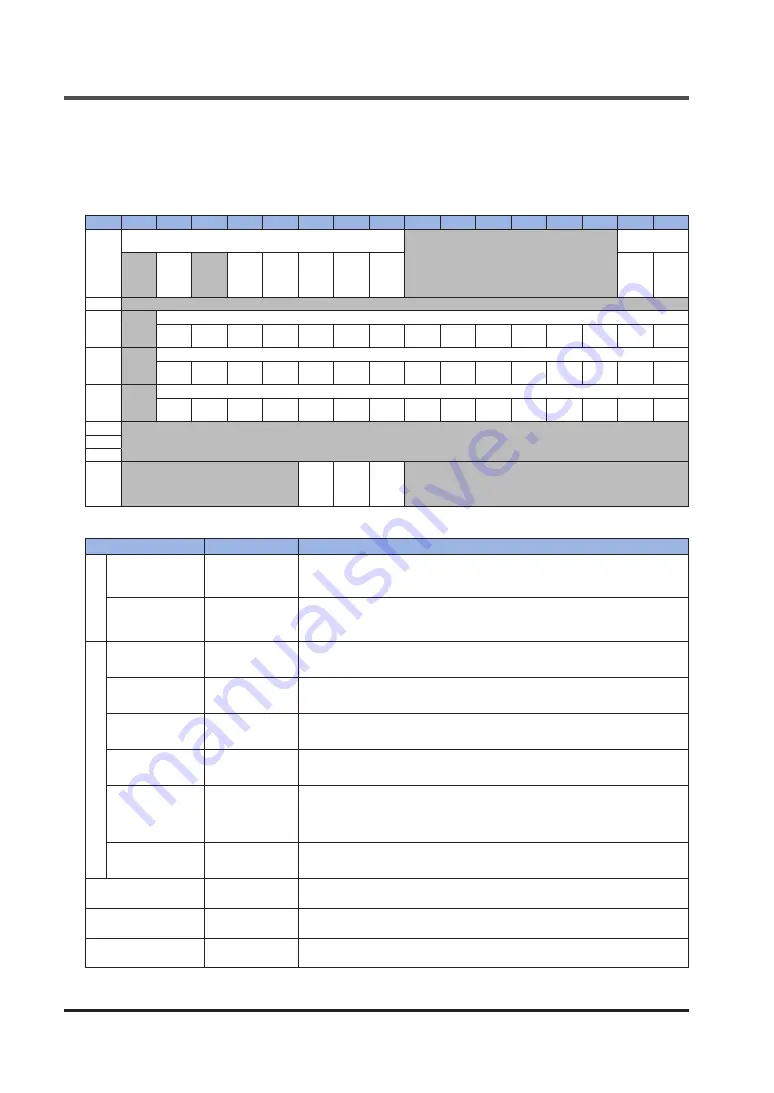
CC-LINK Network Communication
WUME-SCHG1C-4
4-18
■
Remote output RY (Mode 2 Master station → Communication unit)
This is a write-only register for output from the master station to the communication unit in units
of bits.
<Remote output RY>
RY
F
E
D
C
B
A
9
8
7
6
5
4
3
2
1
0
+00
Sensor response data switching request
Not used
Command
request
Not used Error
code Not used Command
Sensor
head
value
Calcu-
lated
value
Normal
mea-
sured
value
Judg-
ment
value
Write
flag
Send
request
+10
Not used
+20 Not used
External input 1 (IN1)
Slave
unit 14
Slave
unit 13
Slave
unit 12
Slave
unit 11
Slave
unit 10
Slave
unit 9
Slave
unit 8
Slave
unit 7
Slave
unit 6
Slave
unit 5
Slave
unit 4
Slave
unit 3
Slave
unit 2
Slave
unit 1
Master
unit
+30 Not used
External input 2 (IN2)
Slave
unit 14
Slave
unit 13
Slave
unit 12
Slave
unit 11
Slave
unit 10
Slave
unit 9
Slave
unit 8
Slave
unit 7
Slave
unit 6
Slave
unit 5
Slave
unit 4
Slave
unit 3
Slave
unit 2
Slave
unit 1
Master
unit
+40 Not used
External input 3 (IN3)
Slave
unit 14
Slave
unit 13
Slave
unit 12
Slave
unit 11
Slave
unit 10
Slave
unit 9
Slave
unit 8
Slave
unit 7
Slave
unit 6
Slave
unit 5
Slave
unit 4
Slave
unit 3
Slave
unit 2
Slave
unit 1
Master
unit
+50
Not used
~
+160
+170
Not used
Error clear
request
Setting
initial-
ization
request
Initializa-
tion done
Not used
<Setting details>
Name
Device No.
Description
Command request
Send request
RY[00]
Send command to controller request bit.
When this bit is set, a command is sent.
To send a subsequent command, clear the bit and then set again.
Write flag
RY[01]
To execute a read command, clear this bit.
To execute a write command, set this bit.
RY[00]: Set before a send request.
Sensor response data switching request (*1)(*2)
Judgment value
(*3)
RY[08]
Change to judgment value mode.
When the bit is set, the mode changes to judgment value mode.
Normal mea-
sured value (*3) RY[09]
Change to normal measured value mode.
When the bit is set, the mode changes to normal measured value mode.
Calculated value
(*3)
RY[0A]
Change to calculated value mode.
When the bit is set, the mode changes to calculated value mode.
Sensor head
value (*3)
RY[0B]
Change to sensor head value mode.
When the bit is set, the mode changes to sensor head value mode.
Command
RY[0C]
Change to command mode.
When this bit is set, changing to command mode and sending com-
mands is allowed.
Set before a command request (RY[00]: send request).
Error code
RY[0E]
Change to error mode.
When this bit is set, the mode changes to error mode.
External input 1
(IN1) (*4)
RY[20] to [2E]
Controls external input 1 on the controller.
When this bit is set, external input 1 turns ON.
External input 2
(IN2) (*4)
RY[30] to [3E]
Controls external input 2 on the controller.
When this bit is set, external input 2 turns ON.
External input 3
(IN3) (*4)
RY[40] to [4E]
Controls external input 3 on the controller.
When this bit is set, external input 3 turns ON.
Содержание SC-HG1-C
Страница 2: ...WUME SCHG1C 4 2 MEMO ...
Страница 8: ...WUME SCHG1C 4 8 MEMO ...
Страница 16: ...WUME SCHG1C 4 1 8 MEMO ...
Страница 17: ...2 1 2 System Configuration 2 1 Communication unit system 2 2 2 2 Unit types 2 4 ...
Страница 22: ...WUME SCHG1C 4 2 6 MEMO ...
Страница 106: ...WUME SCHG1C 4 4 72 MEMO ...
Страница 107: ...5 1 5 Specifications 5 1 Specifications 5 2 5 2 Dimensions 5 3 ...
Страница 110: ...WUME SCHG1C 4 5 4 MEMO ...
Страница 111: ...6 1 6 Warranty 6 1 When you purchase and use the product 6 2 ...
Страница 114: ...WUME SCHG1C 4 6 4 MEMO ...
Страница 115: ...7 1 7 Maintenance 7 1 Maintenance and Inspection 7 2 7 1 1 Maintenance cautions 7 2 7 1 2 Main inspection items 7 2 ...
Страница 124: ...WUME SCHG1C 4 8 8 MEMO ...
Страница 125: ...Revision History 1st edition 1 27 2017 2nd edition 9 8 2017 3rd edition 9 30 2019 4th edition 12 1 2019 ...
Страница 126: ... MEMO ...
Страница 127: ... MEMO ...