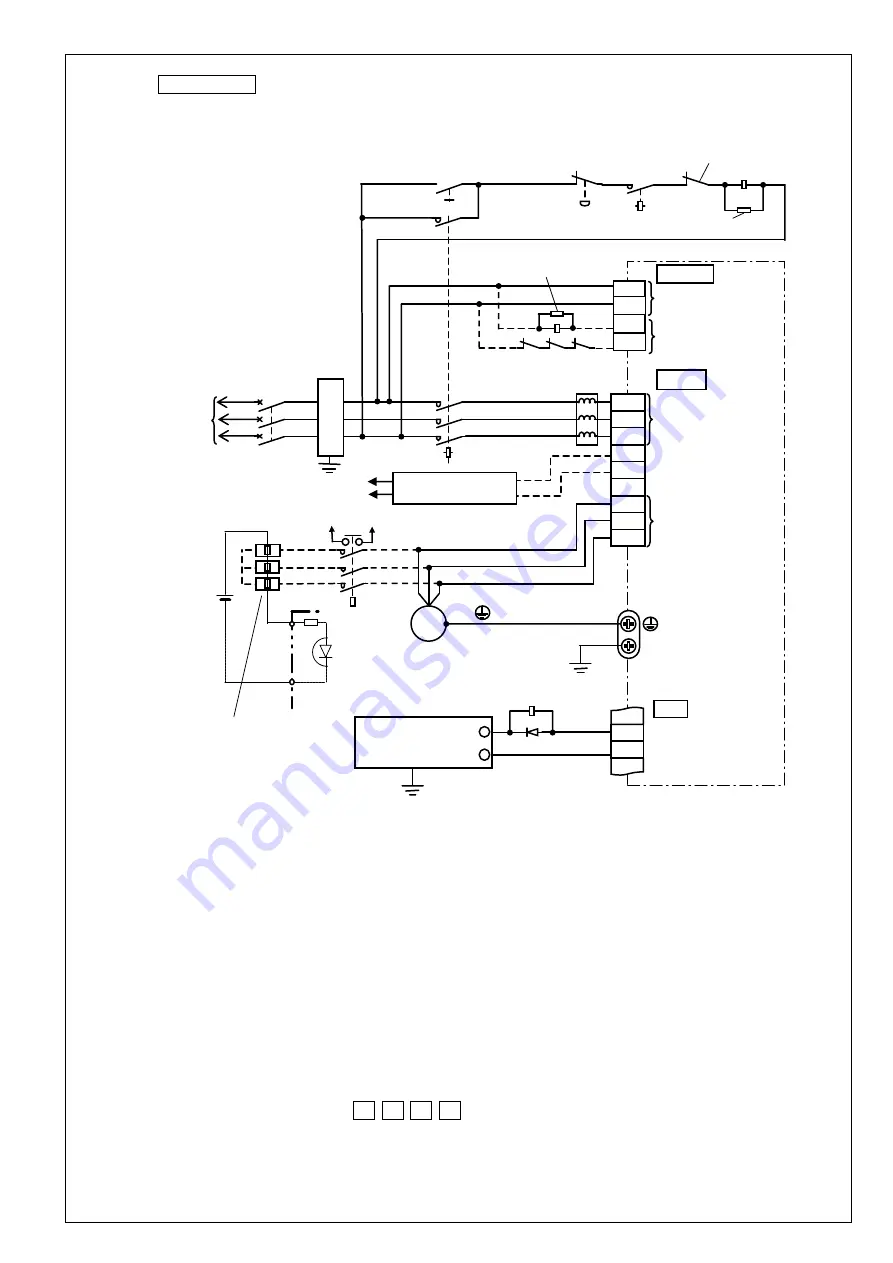
No. SX-DSV03224-56-
R6.0
Motion Control Business Unit, Panasonic Corporation
Size H 200 V
L1
L2
L3
L
ON
MC1
OFF
ALM
L1C
L2C
P
MC1
U
V
W
ALM+
ALM-
ALM
+
-
Terminal
X4
N
B
MCCB
(
Note 3
)
DC24V
(
Note 5
)
MC2
DB1
DB2
MC2
(
Note 2
)
Terminal
(
Note 6
)
Coil surge absorber
Main power
supply
Control power
supply
Power supply
(3-phase)
Built- in Thermostat of an external regenerative resistor
( The wire color of optional accessories is light yellow)
N
oi
se
f
ilt
er
Coil surge absorber
Motor output
External dynamic brake
resistor control
Dynamic brake resistor
built-in thermal protector
(
Note 4
)
Isolated power supply
DC12
~
24 V
(
±
5 %)
Controller side I/O
external
regenerative resistor
Thermostat
( See above)
M
A(U)
B(V)
C(W)
D(
)
(
Note 1
)
When using the amplifier with VCM,
connect the U and W terminals
Note 1) The PIN No. of the motor side connector is stated.
22 kW specification only the notation in parentheses () is the connection destination.
Note 2) Make the electromagnetic contactor (MC2) the same as the electromagnetic contactor (MC1) of the main circuit.
Note 3) To prevent servo-on when the main contact is welded, provide auxiliary contacts to configure protection
by external sequence.
Note 4) Please use three 1.2 Ω 400 W dynamic brake resistors.
Please attach dynamic brake resistance to incombustible material such as metal.
Note 5) Install the thermal protector on the dynamic brake resistor and monitor with the upper side I / O and
configure the protection so that the servo will not be turned on in the sequence during thermal protector operation.
Note 6) If the thermal protector can not be monitored by the upper I / O, input the thermal protector output
Between L2C and DB2 so that the dynamic brake does not operate when temperature protection works.
* For details, refer to 7-1 Power connector XA, XB, XC, XD and terminal block.