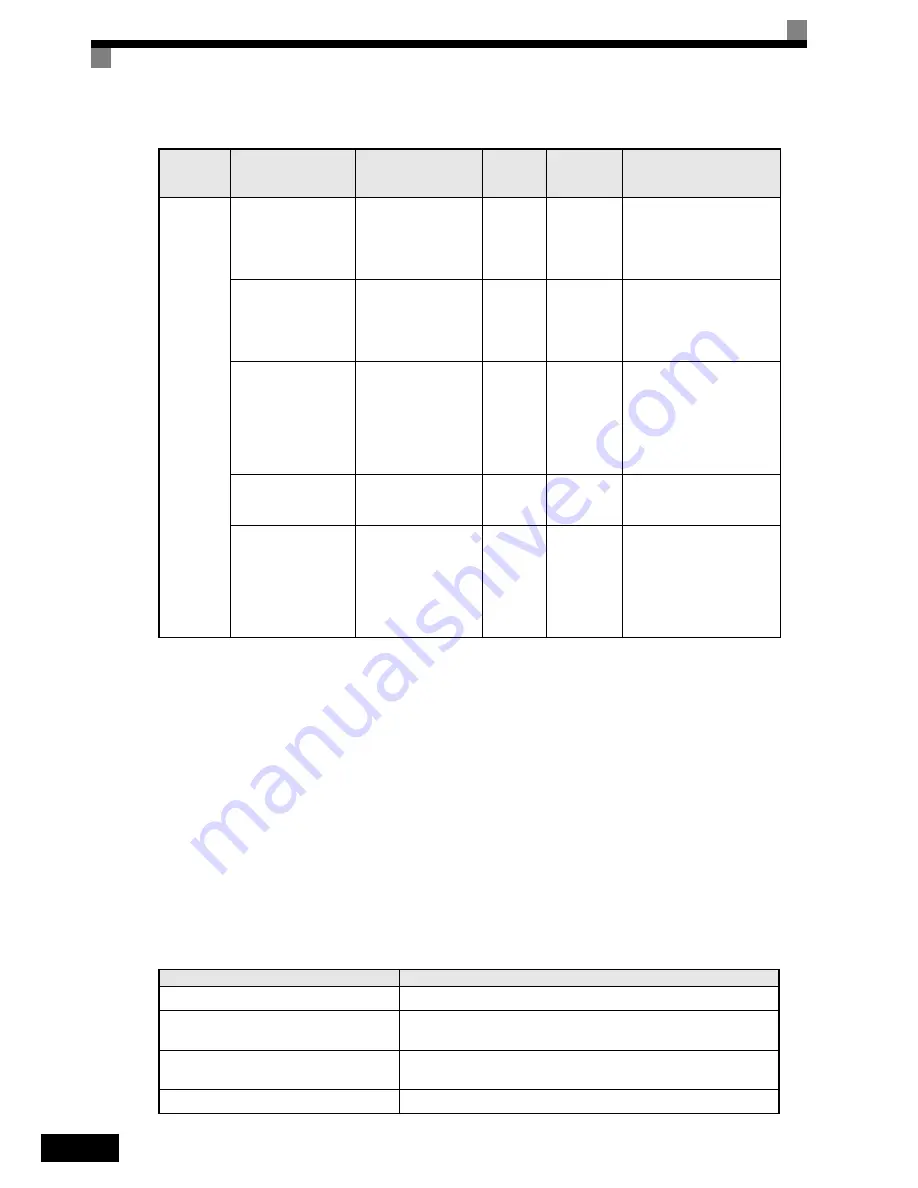
4
-18
* The setting is given for 200 V Class Inverters. Double the voltage for 400 V Class Inverters.
•
Do not change the Torque Compensation Gain (C4-01) from its default setting of 1.00 when using open-
loop vector control 1.
•
If speeds are inaccurate during regeneration in open-loop vector control 1, enable Slip Compensation Dur-
ing Regeneration (C3-04 = 1).
•
Use slip compensation to improve speed precision during V/f control (A1-02 = 0).
Set the Motor Rated Current (E2-01), Motor Rated Slip (E2-02), and Motor No-load Current (E2-03), and
then adjust the Slip Compensation Gain (C3-01) to between 0.5 and 1.5. The default setting for V/f control
is C3-01 = 0.0 (slip compensation disabled).
•
To improve speed response and stability in V/f control with a PG (A1-02 = 1), set the ASR constants (C5-
01 to C5-05) to between 0.5 and 1.5 times the default. (It is not normally necessary to adjust this setting.)
ASR for V/f control with a PG will only control the output frequency; a high gain, such as is possible for
open-loop vector control 2 or flux vector control, cannot be set.
The following user constants will also indirectly affect the control system.
Open-loop
vector con-
trol 2
(A1-02 = 4)
ASR proportional gain
1 (C5-01) and
ASR proportional gain
2 (C5-03)
• Torque and speed
response
• Controlling hunting
and vibration
10.00
10.00 to
50.00
• Increase the setting if
torque or speed response is
slow.
• Reduce the setting if hunt-
ing or vibration occurs.
ASR integral time 1
(high-speed) (C5-02)
and
ASR integral time 2
(low-speed) (C5-04)
• Torque and speed
response
• Controlling hunting
and vibration
0.500 s
0.300 to
1.000 s
• Reduce the setting if
torque or speed response is
slow.
• Increase the setting if hunt-
ing or vibration occurs.
ASR switching fre-
quency (C5-07)
Switching the ASR
proportional gain and
integral time accord-
ing to the output fre-
quency
0.0 Hz
0.0 to max.
output fre-
quency
Set the output frequency at
which to change the ASR
proportional gain and inte-
gral time when the same val-
ues cannot be used for both
high-speed and low-speed
operation.
ASR primary delay
time (C5-06)
• Controlling hunting
and vibration
0.010 s
0.04 to 0.020
Increase the setting if
machine rigidity is low and
the system vibrates easily.
Carrier frequency
selection (C6-11)
• Reducing motor
magnetic noise
• Controlling hunting
and vibration at low
speeds (3 Hz or less)
Depends
on the
capacity.
Default
value
• Increase the setting if
motor magnetic noise is
high.
• Reduce the setting if hunt-
ing or vibration occurs at
low to middle-range
speeds.
Table 4.5 Constants Indirectly Affecting Control and Applications
Name (Constant Number)
Application
Dwell function (b6-01 to b6-04)
Used for heavy loads or large machine backlashes.
Droop function (b7-01 to b7-02)
Used to soften the torque or to balance the load between two motors. Can
be used when the control mode (A1-02) is set to 3 or 4.
Acceleration/deceleration times
(C1-01 to C1-11)
Adjust torque during acceleration and deceleration.
S-curve characteristics (C2-01 to C2-04)
Used to prevent shock when completing acceleration.
Table 4.4 Adjusted User Constants (Continued)
Control
Method
Name (Constant
Number)
Performance
Factory
Setting
Recom-
mended
Setting
Adjustment Method
Содержание VARISPEED G7 -
Страница 3: ......
Страница 11: ...viii...
Страница 33: ...1 16...
Страница 105: ...4 20...
Страница 349: ...6 154...
Страница 375: ...7 26...
Страница 413: ...10 24...
Страница 417: ......