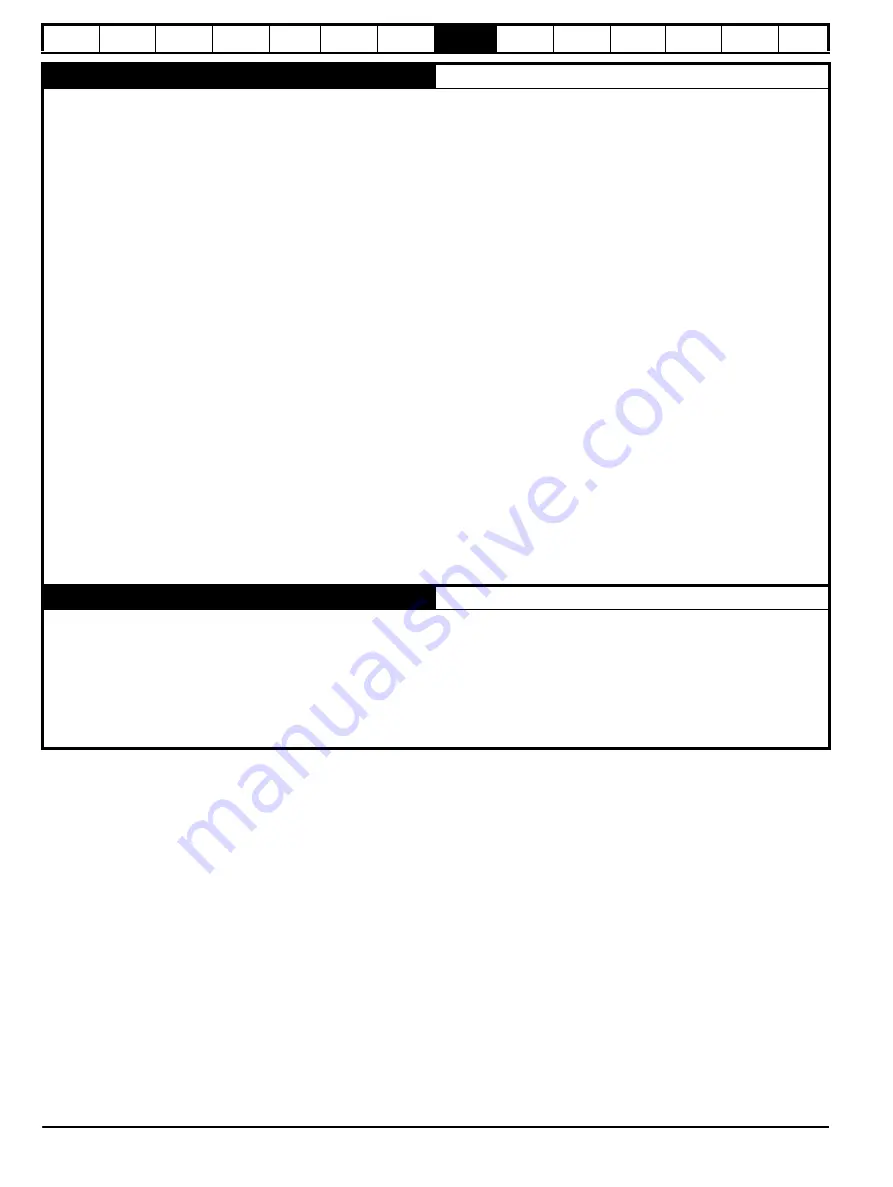
90
Digitax HD M753 Control User Guide
Issue Number: 3
Pr 00.040 {05.012}
Autotune
There are three autotune tests available in RFC-A mode, a stationary test, a rotating test and a mechanical load measurement test. A stationary autotune will
give moderate performance whereas a rotating autotune will give improved performance as it measures the actual values of the motor parameters required by
the drive. A mechanical load measurement test should be performed separately to a stationary or rotating autotune.
It is highly recommended that a rotating autotune is performed (Pr
00.040
set to 2).
•
A stationary autotune can be used when the motor is loaded and it is not possible to remove the load from the motor shaft. The stationary autotune
measures the
Stator Resistance
(05.017) and
Transient Inductance
(05.024) of the motor. These are used to calculate the current loop gains, and at the
end of the test the values in Pr
00.038
and Pr
00.039
are updated.
Maximum Deadtime Compensation
(05.059) and
Current At Maximum Deadtime
Compensation
(05.060) for the drive are also measured. Additionally, if
Enable Stator Compensation
(05.049) = 1, then
Stator Base Temperature
(05.048)
is made equal to
Stator Temperature
(05.046). A stationary autotune does not measure the power factor of the motor so the value on the motor nameplate
must be entered into Pr
00.043
. To perform a stationary autotune, set Pr
00.040
to 1, and provide the drive with both an enable signal (terminal 2 & 6) and
a run signal (terminal 11 or 13).
•
A rotating autotune should only be used if the motor is unloaded. A rotating autotune first performs a stationary autotune, a rotating test is then performed
in which the motor is accelerated with currently selected ramps up to a frequency of
Rated Frequency
(00.047) x 2/3, and the frequency is maintained at
the level for up to 40 s. During the rotating autotune the
Stator Inductance
(05.025), and the motor saturation breakpoints (Pr
05.029
, Pr
05.030
,
Pr
06.062
and Pr
05.063
) are modified by the drive. The power factor is also modified for user information only, but is not used after this point as the stator
inductance is used in the vector control algorithm instead. To perform a Rotating autotune, set Pr
00.040
to 2, and provide the drive with both an enable
signal (terminal 2 & 6) and a run signal (terminal 11 or 13).
•
The mechanical load measurement test can measure the total inertia of the load and the motor. This is used to set the speed loop gains (see Speed loop
gains) and to provide torque feed-forwards when required during acceleration.
Applied torque (sensorless mode)
This test may give inaccurate results, if the motor rated speed is not set to the correct value for the motor, or if
standard ramp mode is active. During the mechanical load measurement test a series of progressively larger torque levels are applied to the motor (20 %,
40 % ... 100 % of rated torque) to accelerate the motor up to
3
/
4
x
Rated Speed
(00.045) to determine the inertia from the acceleration/deceleration time.
The test attempts to reach the required speed within 5 s, but if this fails the next torque level is used. When 100 % torque is used the test allows 60 s for
the required speed to be reached, but if this is unsuccessful an Autotune 1 trip is initiated. To reduce the time taken for the test it is possible to define the
level of torque to be used for the test by setting
Mechanical Load Test Level
(05.021) to a non-zero value. When the test level is defined the test is only
carried out at the defined test level and 60 s is allowed for the motor to reach the required speed. It should be noted that if the maximum speed allows for
flux weakening then it may not be possible to achieve the required torque level to accelerate the motor quickly enough. If this is the case, the maximum
speed reference should be reduced. To perform a mechanical load measurement autotune, set Pr
00.040
to 4, and provide the drive with both an enable
signal (terminal 2 & 6) and a run signal (terminal 11 or 13).
Following the completion of an autotune test the drive will go into the inhibit state. The drive must be placed into a controlled disable condition before the drive
can be made to run at the required reference. The drive can be put in to a controlled disable condition by removing the Safe Torque Off signal from terminal 2
& 6, setting the
Drive Enable
(06.015) to OFF (0) or disabling the drive via the control word (Pr
06.042
& Pr
06.043
).
Pr 00.038 {04.013} / Pr 00.039 {04.014}
Current Loop Gains
The current loop gains proportional (Kp) and integral (Ki) gains control the response of the current loop to a change in current (torque) demand. The default
values give satisfactory operation with most motors. However, for optimal performance in dynamic applications it may be necessary to change the gains to
improve the performance. The
Current Controller Kp Gain
(00.038) is the most critical value in controlling the performance. The values for the current loop
gains can be calculated by performing a stationary or rotating autotune (see
Autotune
Pr
00.040
, earlier in this table) the drive measures the
Stator
Resistance
(05.017) and
Transient Inductance
(05.024) of the motor and calculates the current loop gains.
This will give a step response with minimum overshoot after a step change of current reference. The proportional gain can be increased by a factor of 1.5
giving a similar increase in bandwidth; however, this gives a step response with approximately 12.5 % overshoot. The equation for the integral gain gives a
conservative value. In some applications where it is necessary for the reference frame used by the drive to dynamically follow the flux very closely (i.e. high
speed Sensorless RFC-A induction motor applications) the integral gain may need to have a significantly higher value.
Содержание Digitax HD M753 EtherCAT
Страница 261: ......
Страница 262: ...0478 0461 03...