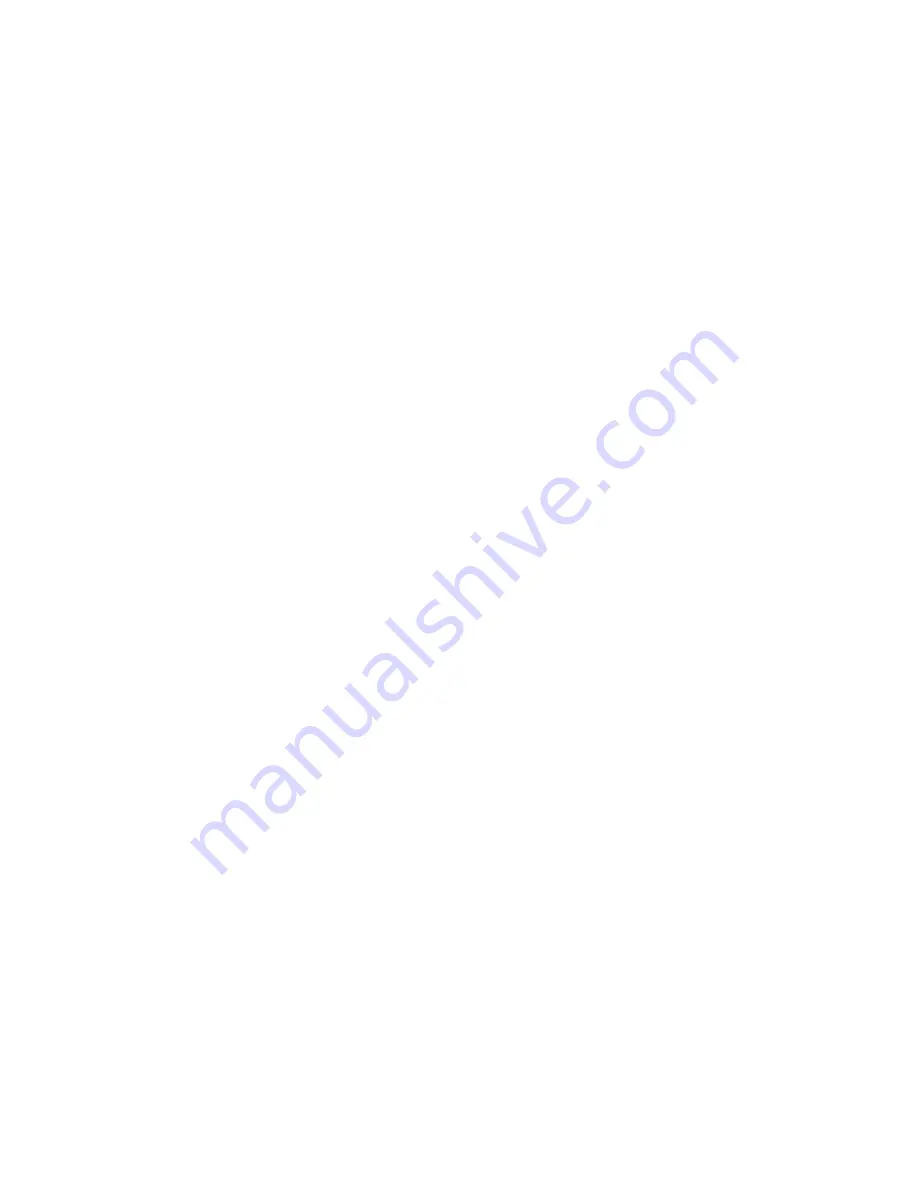
RP0169-2002
6
NACE International
made to flanges or at butt weld joints. Attachment
at other sites may adversely affect the mechanical
properties of the pipe because of the heat of
welding.
4.5.4.2 Test lead wire may be attached to
aluminum pipe by soldering. If low-melting-point
soft solders are used, a flux is required.
Flux
residues may cause corrosion unless removed.
NOTE:
The use of copper test lead wire may
cause
preferential
galvanic
attack
on
the
aluminum pipe. When copper wire or flux is used,
care must be taken to seal the attachment areas
against moisture. In the presence of moisture, the
connection may disbond and be damaged by
corrosion.
4.5.4.3 Aluminum tabs to which test lead wires
have been TIG welded can be attached by an
explosive bonding technique called high-energy
joining.
4.5.4.4 Mechanical
connections
that
remain
secure and electrically conductive may be used.
4.5.5 Attachment of Copper Test Lead Wire to Copper
Pipe
4.5.5.1 Copper test lead wire, or copper tabs
attached to copper wire, may be attached to
copper pipe by one of the following methods. The
relative thickness of the wire and the pipe wall
dictates, in part, which of the methods can be
used.
4.5.5.1.1 Arc welding (TIG, MIG, or shielded
metal);
4.5.5.1.2 Electrical resistance (spot) welding;
4.5.5.1.3 Brazing;
4.5.5.1.4 Soldering; or
4.5.5.1.5 Mechanical connection.
4.5.5.2 Attention should be given to proper joining
procedures to avoid possible embrittlement or loss
of mechanical properties of the metals from the
heat of welding or brazing.
4.5.5.3 A flux may be required, or self-produced,
when brazing with some filler metals or soldering
with some low-melting-point soft solders. Because
flux residues may cause corrosion, they should be
removed.
________________________________________________________________________
Section 5: External Coatings
5.1 Introduction
5.1.1 This section recommends practices for selecting,
testing and evaluating, handling, storing, inspecting,
and installing external coating systems for external
corrosion control on piping systems.
The function of external coatings is to control corrosion
by isolating the external surface of the underground or
submerged piping from the environment, to reduce
cathodic protection current requirements, and to
improve current distribution.
5.1.3 External coatings must be properly selected and
applied and the coated piping carefully handled and
installed to fulfill these functions.
Various types of
external coatings can accomplish the desired functions.
5.1.2.1 Desirable
characteristics
of
external
coatings include the following:
5.1.2.1.1 Effective electrical insulator;
5.1.2.1.2 Effective moisture barrier;
5.1.2.1.3 Application to pipe by a method that
does not adversely affect the properties of the
pipe;
5.1.2.1.4 Application to pipe with a minimum
of defects;
5.1.2.1.5 Good adhesion to pipe surface;
5.1.2.1.6 Ability to resist development of
holidays with time;
5.1.2.1.7 Ability to resist damage during
handling, storage, and installation;
5.1.2.1.8 Ability
to
maintain
substantially
constant electrical resistivity with time;
5.1.2.1.9 Resistance to disbonding;
5.1.2.1.10 Resistance to chemical degrad-
ation;
5.1.2.1.11 Ease of repair;
5.1.2.1.12 Retention of physical character-
istics;
5.1.2.1.13 Nontoxic to the environment; and
Содержание CP 1
Страница 1: ...CP 1 Cathodic Protection Tester Course Manual February 2005 NACE International 2000 ...
Страница 265: ......
Страница 266: ......
Страница 267: ......
Страница 268: ......
Страница 301: ...RP0169 2002 32 NACE International ISBN 1 57590 035 1 ...
Страница 535: ...TM0101 2001 24 NACE International ISBN 1 57590 137 4 ...