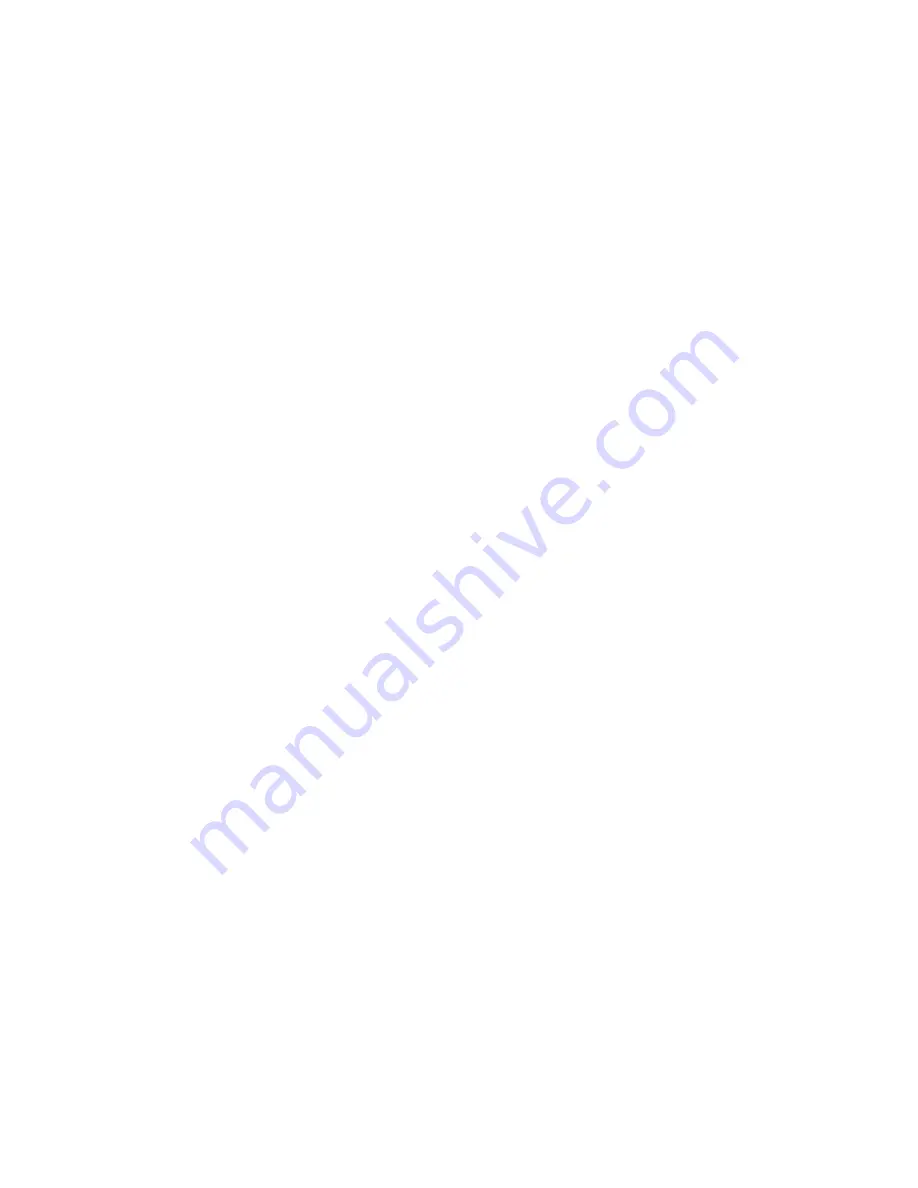
RP0176-2003
26
NACE International
ASTM D 522
28
ASTM C 633
13
ASTM D 968
29
ASTM D 3359
30
ASTM D 3363
31
ASTM D 4214
32
Equivalent tests from organizations other than ASTM
may be used.
13.4.3 The coating system ultimately selected de-
pends on many environmental, application, and per-
formance considerations, including the following:
13.4.3.1 The length of time primed steel is stored
during construction periods and resistance to
abrasion associated with handling and fabrication
with a minimum of damage.
13.4.3.2 Coating systems that can be applied and
maintained with conventional and readily available
application equipment.
13.4.3.3 Cold temperatures and inclement wea-
ther restrictions for structures placed in northern
latitudes.
13.4.3.4 Chemically cured coatings that have high
impact resistance and resistance to spills of sol-
vents and corrosive chemicals are often used on
the deck areas of offshore structures because of
anticipated exposure to weathering, abrasion
associated with drilling operations, and spills of
drilling mud, formation fluids, diesel fuels, lubri-
cants, and well-completion compounds.
13.4.3.5 Offshore coatings are exposed to high-
intensity ultraviolet light and should be resistant to
heavy chalking and color fade.
13.4.3.6 Coating systems that are easily repaired
and maintained are usually preferred.
13.4.3.7 Inorganic zinc-rich primers, when dam-
aged and exposed in service, do not readily accept
another coat of inorganic zinc-rich primer (IOZ),
and are normally repaired with an organic zinc-rich
coating or chemically cured, inhibited primer.
13.5 Storage, Handling, and Mixing of Materials
13.5.1 All materials used in the initial or maintenance
coating of offshore structures should be furnished in
the manufacturer’s original, unopened container, clear-
ly labeled to identify the contents. The materials
should be stored in a manner that prevents exposure to
weather extremes, with 10 to 32°C (50 to 90°F) being
optimum.
13.5.1.1 Thinners, diluents, or clean-up materials
should comply with the coating manufacturer’s
recommendation, or if independently purchased,
they should be of compositions approved by the
coating manufacturer.
13.5.1.2 Single-supplier responsibility should be
maintained by using primers, intermediates, and
finish coatings from the same supplier.
13.5.1.3 All coating materials should be thorough-
ly agitated prior to application. If there is settling of
the pigment, it should be redispersed with a power
agitator to form a uniform mixture. For two-compo-
nent materials, the catalyzed mixture also should
be agitated with a power mixer. For heavily pig-
mented coating, such as zinc-rich primer, agitation
should be continued during application to prevent
settling.
13.5.1.4
Mixed coating solutions should be
strained through a 250 to 600 µm (30 to 60 mesh)
screen to remove any foreign materials or undis-
persed pigment particles.
13.5.1.5 When materials incorporating a catalyst
or converter are mixed, the addition of converter
beyond that recommended by the manufacturer
has an adverse effect on the coating’s application,
curing, and performance characteristics.
13.5.1.6 Solvent can closures should be kept tight
at all times to prevent the entrance of humid air,
which can lead to condensation.
13.5.1.7 Manufacturer’s shelf life recommenda-
tions for structure coating components should be
followed.
13.6 Application Equipment
13.6.1 Most coatings are applied by spray. Conven-
tional spray pressure pots shall be equipped with dual
regulators and an air-driven agitator. All spray equip-
ment must be equipped with fluid tips, needles, and air
caps consistent with the coating manufacturer’s recom-
mendations. The air supply line to the pressure tank
must be fitted with an efficient oil and moisture separ-
ator. For applications by airless spray, a hydraulic
pump that achieves a minimum pressure-compounding
ratio of 30:1 should be used. An atomizing tip con-
sistent with the manufacturer’s recommendation should
be selected. The tip should provide the degree of
atomization and optimum fan width consistent with the
configuration of the structure to be coated.
13.6.2 Clean cans and strainers should be provided
for mixing the coating materials.
Содержание CP 1
Страница 1: ...CP 1 Cathodic Protection Tester Course Manual February 2005 NACE International 2000 ...
Страница 265: ......
Страница 266: ......
Страница 267: ......
Страница 268: ......
Страница 301: ...RP0169 2002 32 NACE International ISBN 1 57590 035 1 ...
Страница 535: ...TM0101 2001 24 NACE International ISBN 1 57590 137 4 ...