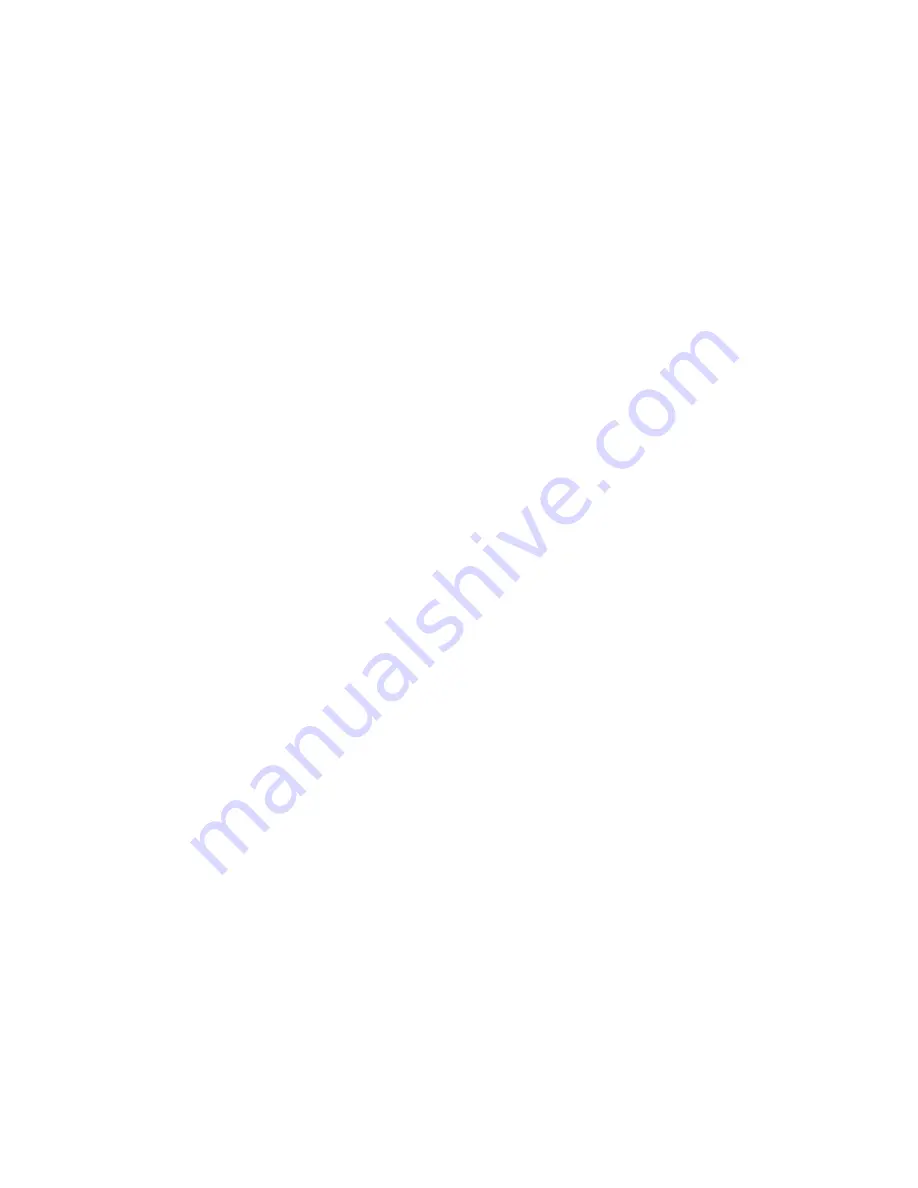
RP0176-2003
28
NACE International
(d) Type and amount of rigging scaffolds and safety
equipment required,
(e) Deck space and housing,
(f) Availability of transportation for workers,
equipment, material, and supplies,
(g) Excess equipment on structures that may require
moving, and
(h) Appropriateness of specified coating systems
based on the exposure and logistics of the structure.
13.9.3 In scheduling and coordinating structure opera-
tion, the coating work should be given special consider-
ation. Company personnel must be informed of the
coating work to prevent salt-water washdowns and
spills of oil or mud chemicals on blasted or primed sur-
faces. Workovers, drilling, or construction can seri-
ously hinder or delay the coating work.
13.9.4 Company personnel and inspectors must be
familiar with the problems and requirements of surface
preparation and application of the coating materials.
13.9.5 In applying coating to intricate shapes or in
pipe-congested areas, it is difficult to maintain thin
films. Coatings such as inorganic zinc-rich primers,
which are sensitive to excessive thickness and mud-
crack and spall at a thickness of about 100 µm (4 mils)
or more, must be avoided unless special care is exer-
cised during application.
13.10 Galvanizing
13.10.1 Hot-dip galvanizing is an effective method for
protecting complex steel shapes that would be costly
and difficult to coat by conventional means. Such
shapes as grating, handrails, stairs, meter houses,
equipment skids, and others may be protected by gal-
vanizing.
13.10.2 Galvanizing, like other zinc coatings, is sub-
ject to attack by acid and alkaline conditions, and
should not be exposed to cement, drilling mud, or well
acid.
13.10.3 Because galvanized coatings sacrifice them-
selves galvanically when exposed in the splash zone or
when immersed, causing rapid breakdown or failure,
other materials or overcoating should be used instead.
13.10.4 Galvanized metal can be overcoated by the
use of suitable primers and topcoats for better chem-
ical and salt-water exposure.
13.10.5 All galvanizing shall be applied in accordance
with ASTM A 123
33
and A 153.
34
________________________________________________________________________
Section 14: Coatings Inspection
14.1 Introduction
14.1.1 This section provides inspection procedures to
verify compliance with the governing coating specific-
ations.
14.1.2 The inspection tools suggested for use by the
inspectors are needed to provide acceptable results.
Judgment based on broad experience, however, is the
best inspection tool available.
14.1.3 A pre-job conference should be held to stipu-
late the responsibilities and relationship of the owner,
inspector, applicator, and coatings supplier.
14.2 Job Orientation
14.2.1 Inspectors should thoroughly familiarize them-
selves with the particular job to be done. Careful notes
should be made initially so that confusion is eliminated
later. Acknowledgement of receipt of project specific-
ation, and understanding of same, should be made.
14.2.2 Inspectors should acquaint themselves with the
materials to be used on the job.
14.2.2.1 The specification should state abrasive
requirements and anchor pattern according to
standards on which a mutual agreement has been
reached.
14.2.2.2 All coating materials should be checked
at the job site for conformance to specifications.
Prior to the initiation of the job, the inspector
should be provided the applicable product tech-
nical and material safety information; such inform-
ation shall be made readily available by the coat-
ings supplier. Incompatibilities should be reported
prior to initiation of the job.
14.2.3 The inspector should make an initial inspection
of all equipment on the job site to ensure and docu-
ment that it meets the job requirements.
14.2.3.1 Special attention should be paid to abra-
sive-blasting equipment. The inspector should
verify and enforce the specifications for abrasive-
blast equipment to ensure that the compressors
are sized properly for the number of nozzles and
hoses, and that gaskets and nozzles are properly
sized and in good condition. Air quality should be
checked for cleanliness and dryness (see Para-
Содержание CP 1
Страница 1: ...CP 1 Cathodic Protection Tester Course Manual February 2005 NACE International 2000 ...
Страница 265: ......
Страница 266: ......
Страница 267: ......
Страница 268: ......
Страница 301: ...RP0169 2002 32 NACE International ISBN 1 57590 035 1 ...
Страница 535: ...TM0101 2001 24 NACE International ISBN 1 57590 137 4 ...