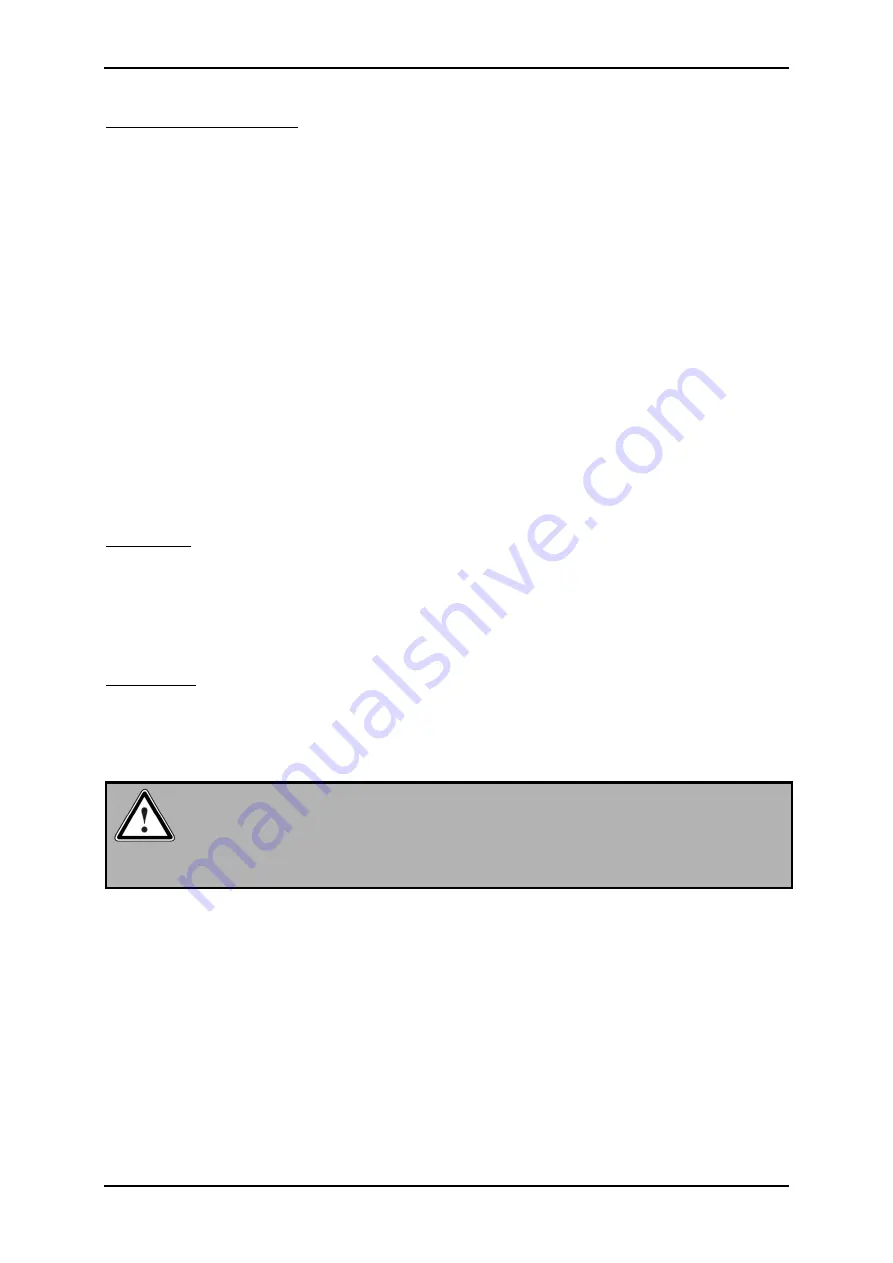
Functional safety technology
Page 70
Product Manual „Servo drives ARS 2320, ARS 2340, ARS 2320W, ARS 2360W“
Version 8.0
3. Floating feedback contact:
The integrated circuit for the “Safe Torque-Off (STO)” function also has a floating feedback contact
([X3] pins 5 and 6) for the existence of the driver supply. This contact is designed as a normally closed
contact. It, for example, has to be connected to the superordinated control. At regular intervals (for
example PLC cycle or with each “Safe Torque-Off (STO)” request), the PLC has to perform a
plausibility check between the triggering of the driver supply relay and the feedback contact (contact
open = driver supply available).
In the case of an error during the plausibility check, further operation must be prevented, for example
by eliminating the controller enabling (servo drive enabling) or by shutting down the power contactor.
6.2.2
Holding brake activation
In the case of activation of the “Safe Torque-Off” function, the holding brake is switched currentless
(brake applied); (see
Figure 11: Block diagram “STO” as per EN ISO 13849-1, Category 3
Performance Level d
).
1st Channel:
During operation the holding brake is controlled with the DIN5 (controller enabling) (see timing
diagram below). The first shut-down path “output stage enabling” acts on the brake driver via the µP
and switches the holding brake currentless (brake applied).
2nd Channel:
The second shut-down path “triggering of driver supply relay” directly acts on s MOSFET which
deactivates the holding brake (brake applied).
DANGER!
The user is responsible for the dimensioning and the safe functioning of the holding brake.
The functioning of the brake must be checked and ensured by means of a suitable brake
test.
Содержание ARS 2320
Страница 1: ......