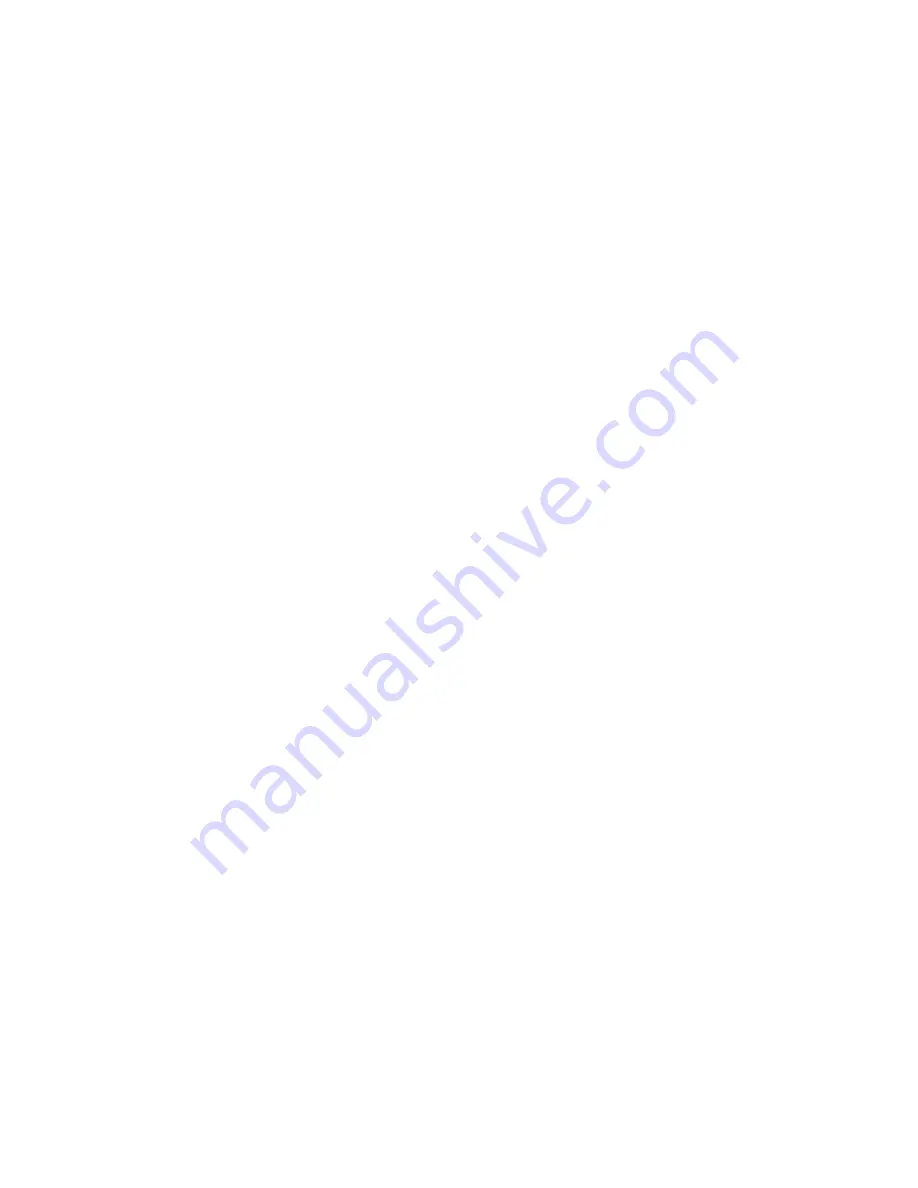
GRAUPNER GmbH & Co. KG D-73230 KIRCHHEIM/TECK GERMANY
Änderungen vorbehalten! Keine Haftung für Druckfehler! Ident-Nr. 0057999
Made in Thailand
04/2003
75
75
glass tape over the guide tubes in the same way, remembering to roughen the joint surfaces beforehand
using abrasive paper, as described in the introduction to these instructions, to ensure that the glued joints
are really strong. It is important to glue the guide tubes and the plywood formers in place with great care
(this applies to all glued joints), because the aerodynamic conditions place severe loads on all hatches and
hatch retainer systems when the model is flying.
Speedbrake
−
Cut out the speedbrake / hatch along the rectangular markings. In our pictures the cut lines feature
radiussed corners, but these are more difficult to cut. Tape a steel ruler on the model (Figs. 2,
8a, 8b
) so
that you can score along the marked lines with a sharp knife, before cutting right through with a fine
sawblade or knife (Figs. 2a,
8b
).
−
Caution:
the speedbrake hatch is attached permanently using an elasto-hinge (living hinge), like the turbine
hatch.
Take care not to cut through the hinge when wielding the knife or saw.
−
The hatch can now be opened - work cautiously here, easing it up by moving it carefully and repeatedly.
You may need to widen the gap at the integral hinge line using abrasive paper or a triangular file until the
hatch can be opened through 70 - 80° (Figs. 2b,
8c
).
−
If you accidentally detach the speedbrake completely, i.e. you cut through the elasto-hinge, you can re-
attach it using the two pinned hinges (No. 31) and the steel rod (No. 32) supplied in the kit: tape the
speedbrake to the fuselage as shown in (Fig. 2d), cut holes for the pinned hinges (No. 31), and align the
pivot axis of the hinges (No. 31) using the steel rod (No. 32). Glue the hinges in place on the inside face
using 5-minute epoxy. Apply glass cloth (No. 30) over the hinges to reinforce the joints.
Speedbrake linkage
−
Prepare the speedbrake linkage and servo (
Figs. 9, 10
). Fit the servo in the longitudinal member and secure
it using the screws supplied with the servo (right-hand side, as seen from the tail). Cut down the Novotex
actuating lever (No. 15) as shown.
−
Tack the Novotex lever (No. 15) to the speedbrake using thick cyano, then reinforce the joint with small
pieces of glass cloth and epoxy (Figs. 8b,
10
). Caution: maintain the stated distance between the pushrod /
servo and the Novotex lever (No. 15).
−
Cut the pushrod between servo and speedbrake to the correct length and adjust it carefully (the Graupner
digital Servo Tester, Order No. 763, is useful here).
−
Complete the pushrod as described under “General information on control linkages”.
Rudder servos
−
Screw the rudder servos to the factory-installed formers, working through the turbine access hatch (Figs. 9,
20b
).
−
Fit output arms of adequate length on the rudder servos; they must project through the pre-cut pushrod slots
on the top surface of the fuselage. Fit extension leads of appropriate length to the servo leads (Figs. 9a,
20c
)
(servo extension leads, Order No. 3935.75).
−
(
Fig. 20a
) It may be necessary to file back the projecting parts of the servo to compensate for
manufacturing tolerances (
Fig. 20
). The rubber grommets can also be omitted if necessary; secure the
servos with self-tapping screws and washers.
Retractable undercarriage
−
The retract units are fixed to factory-installed plywood supports inside the machined openings in the wings,
using the self-tapping screws (4 x 20, cross-head, 12 off) supplied with the retract sets, Order No. 175 /
174.
Be sure to drill 2.3 mm Ø pilot-holes beforehand, otherwise the plywood plates may split or
burst
. (Figs. 3,
11
)
−
Align the retract units with the machined openings, i.e. the main retract units should be parallel with the
spring struts when retracted (Figs. 3a,
12
). Position the noseleg unit accurately (Figs. 3b, 3c,
11, 11a
), mark
the hole positions, drill pilot-holes, and screw the unit in place.
−
If necessary sand the shape of the retract unit openings to match the outline of the units when retracted. It is
essential to leave sufficient space between the undercarriage legs and wheels in the underside of the
fuselage to ensure that the wheels can still be extended and retracted without fouling at any point, even if
the legs are slightly bent or dirty.