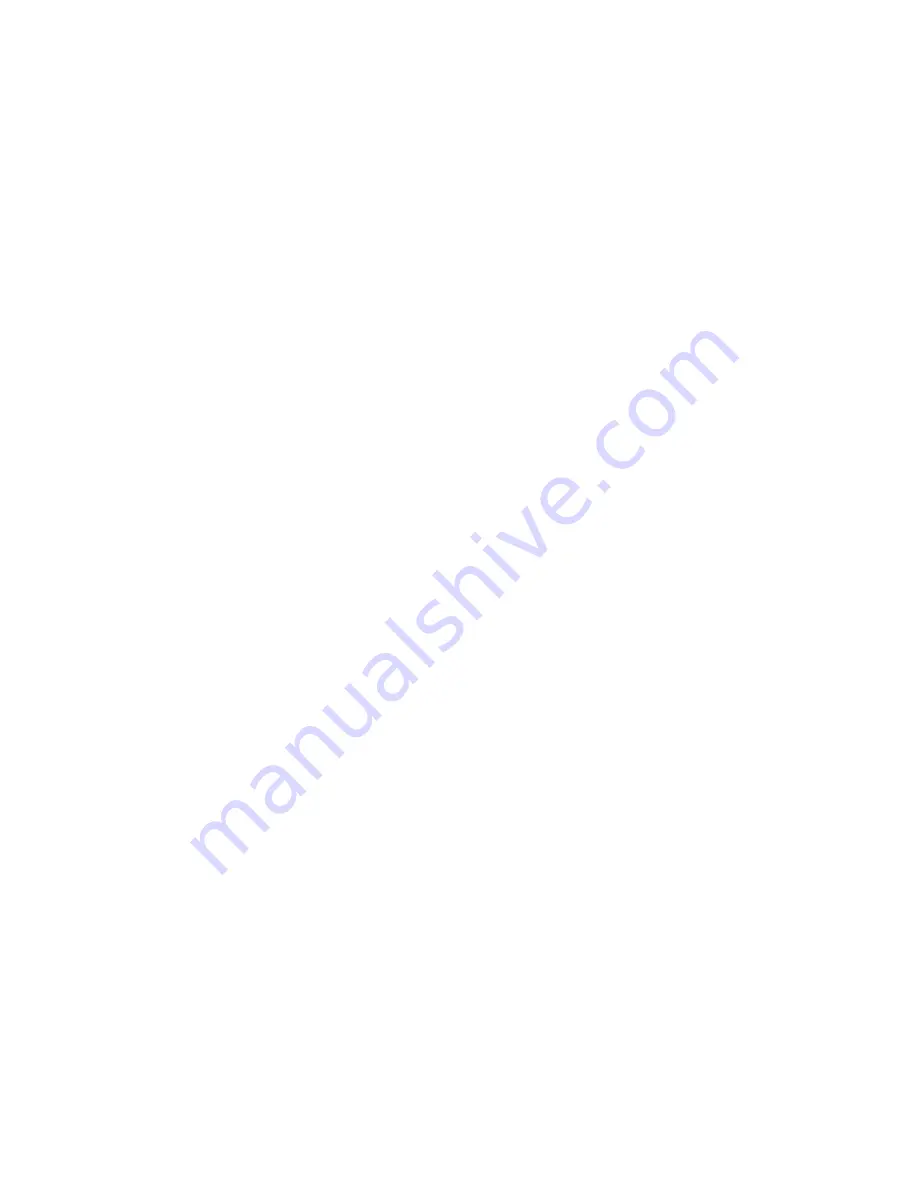
GRAUPNER GmbH & Co. KG D-73230 KIRCHHEIM/TECK GERMANY
Änderungen vorbehalten! Keine Haftung für Druckfehler! Ident-Nr. 0057999
Made in Thailand
04/2003
74
74
Note: you must not use cyano for gluing the horns to the control surfaces. The horns must be bonded to the
elevons, rudders and speedbrake, using epoxy laminating resin or UHU endfest 300.
If you are using UHU plus endfest 300 or epoxy laminating resin, be sure to use an adequate quantity of the
adhesive. In the case of the horn joints, this means completely filling the machined horn slots with resin. Use
only the adhesives expressly recommended in the instructions!
Note
Areas of the fuselage which are to be glued should be rubbed down with medium-grit abrasive paper to remove
any lingering traces of mould release agent. Aim at reducing the glossy surface to an even matt finish, especially
when dealing with smooth, shiny GRP parts, otherwise there is little chance of obtaining durable glued joints.
Parts to be glued must be dry and free of grease and dust.
For technical reasons many of the factory-fitted plywood parts are not completely bonded to the GRP skin; this
applies in particular in the area around the turbine installation. Check all joints very carefully, and apply
thickened UHU endfest 300 (slow-setting epoxy) or laminating resin to the joints to strengthen them. It is
important to check each joint individually!
The plywood parts supplied in the kit are machine-cut to shape, but they may need fine trimming to obtain a
perfect fit. This applies in particular to the small parts which make up the servo mounts.
Mechanical linkages
All the
linkages / pushrods
for the elevons, rudders and speedbrake should be cut to the correct length from the
M3 x 1000
studding
(threaded rod) supplied. The M3 clevises must be
locked / secured
using M3 locknuts. Of
course, the M3 clevises can also be
soldered
or
glued
to the pushrods (Figs. 13, 13a, 14a, 14b, Harpoon 1
instructions), (Figs. 9, 28, Harpoon 2 instructions).
The
pushrods
which actuate the
canards
and
thrust vector system
are also cut from the M3 studding, but are
then
reinforced
using suitable lengths of
carbon fibre tube
, cut from the 5 Ø x 3 Ø x 1000 mm carbon fibre
tubing supplied. Schematic example: Fig. 13, Harpoon 1 instructions.
In the interests of safety we also advise that you shrink a length of heat-shrink sleeve (included in the kit) over
all clevis / pushrod joints. Example: Fig. 31, supplementary instructions).
General information:
when making up pushrods and other linkages, ensure that the servos are at neutral / centre
beforehand, unless otherwise stated. The output levers must also be positioned at 90° to the pushrods. Properly
aligned pushrods and accurately centred servos make the model set-up procedure much easier, and you will
certainly appreciate this when you start programming and adjusting the control surfaces. The Graupner Servo
Tester, Order No. 763, is always a useful aid at such times.
Illustrations are indicated by “Fig.” numbers; where printed
bold
they refer to the
supplementary instructions
,
where printed in normal weight they refer to the original Harpoon 1 instructions.
Turbine access hatch
−
The hatch is machine-cut as standard, and attached to the fuselage using an “elasto-hinge” (living hinge). It
is held closed by two steel pins (No. 28) fitted from the rear (turbine exhaust end).
−
Drill a pair of 3.2 mm Ø holes from the rear, on either side of the turbine opening, to accept the guide tubes
(No. 29 - 3.2 Ø x 2.2 Ø x 330 mm). Check that they are parallel and symmetrical - please measure this -
before gluing them in place permanently. The correct position is shown in Figs. 1,
1
.
−
Glue the plywood strips (No. 17) on both sides of the fuselage hatch opening; they should project slightly
into the aperture in order to form stop-strips for the hatch (Figs. 1a,
6
).
−
Close the hatch and tape it shut, flush with the fuselage skin.
−
Now insert the guide tubes (No. 29) into the previously drilled 3.2 mm Ø holes. Check by eye and with a
ruler that they are parallel, then secure them with thick cyano (use activator spray - Figs. 1b,
2
).
−
Cut through the two previously installed tubes (No. 29) on both sides, working through the gap between the
hatch and the fuselage (Fig. 1c); the turbine hatch can now be opened again.
−
The hatch is held against the fuselage using the two 2 Ø x 250 mm steel rods (No. 28 - Figs. 2,
5
). Before
you insert the steel rods, remove a metal linkage ball from two ball-links (No. 57) and solder them to one
end of the rods (
5
) - these form “handles”, and avoid the rods slipping back inside the guide tubes (Figs. 1d,
5
).
−
Glue / tack the plywood formers (No. 19 - Figs. 1e,
4, 7a
) parallel to the guide tubes (No. 29) using cyano.
Note that you may have to trim the formers to conform to the curvature of the fuselage hatch.
−
Mix up some thickened epoxy and reinforce the joints between the guide tubes and the plywood parts of the
access hatch by gluing the woven glass tape (No. 30) over them, as shown in Figs. 1f,
7
. Apply patches of